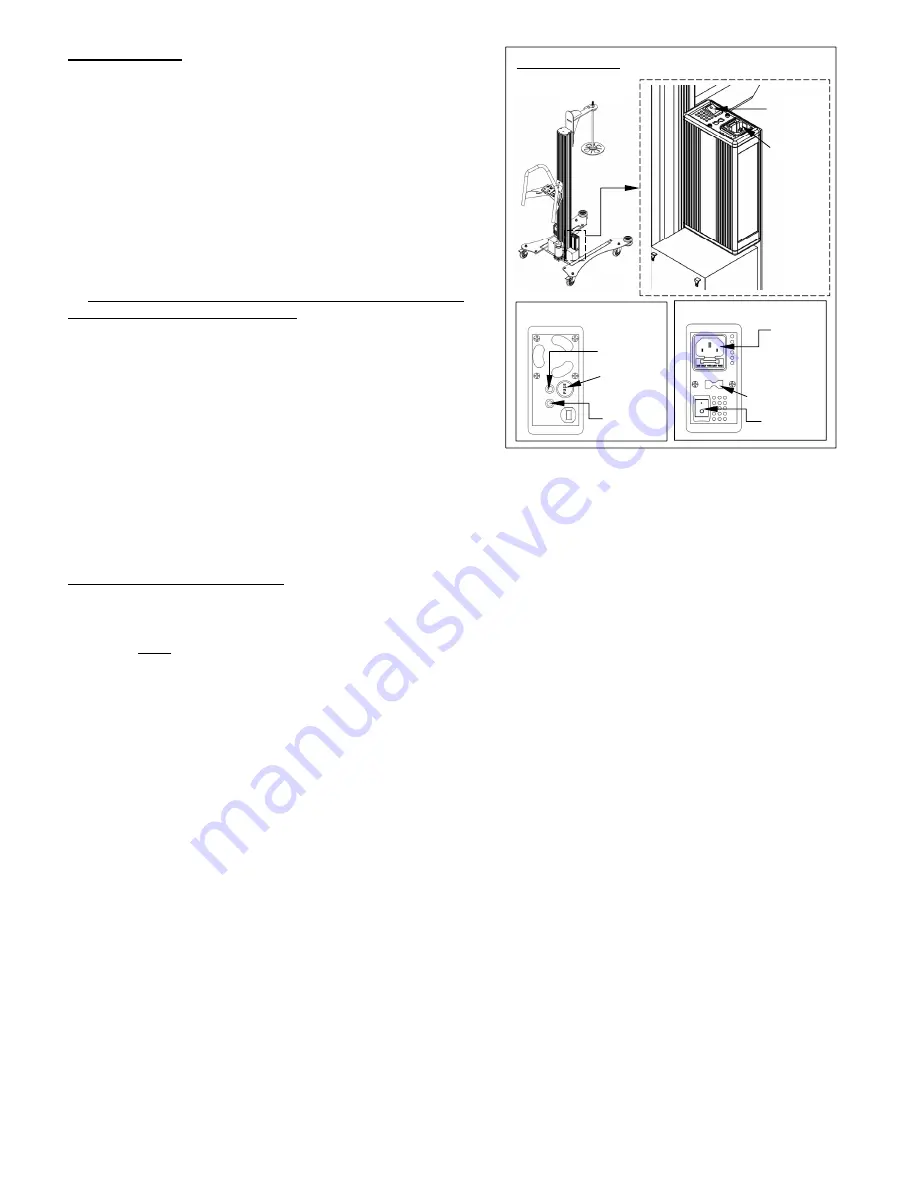
Rev.
5/19/2015
PEL-88-A-SWA,
MANUAL.doc
Copyright 2015 Vestil Manufacturing Co.
Page 9 of 11
System power:
Power is supplied by two 12V batteries. Both batteries are
completely sealed and are therefore maintenance free.
To recharge the batteries, every wrapping machine includes a
24V charger. The charger operates on 115 VAC and requires a
3-prong (grounded) extension cord. The charger monitors and
reacts to the battery voltage during the recharging process.
When the batteries are fully charged, a green LED on the bottom
of the charger turns on (see diagrams to the right). The battery
charge gauge (see “Touchpad control” on p. 6) displays the
amount of battery charge remaining as a percentage of full
(100%) charge. To determine the true level of charge, wait at
least 1/2 hour after turning off the charger. If the voltage is
12.65V or more, then the batteries are fully charged.
Charge the batteries for at least 4 hours before using the
wrapping machine for the first time.
How frequently the batteries require charging depends on the
load applied to the batteries (i.e. how many times the carriage is
moved and how quickly—faster speed will drain the battery more
rapidly) and the duration and frequency of use. Experience will
dictate when the batteries should be charged.
Whenever recharging is begun, it should continue until the
batteries are fully charged. Do not interrupt the charging cycle.
Fully charging the batteries every time recharging is undertaken
maximizes battery life.
Recommendations regarding battery charging: 1) Recharge the batteries
at least
once every 2 weeks; 2) Leave
the charger plugged in when the unit is not in use (the battery charger can remain connected to the batteries for long
periods without causing damage to the batteries); 3) Disconnect the batteries when the unit will be unused for 1 month
or longer; 4) ALWAYS keep the wrapping machine dry.
Inspections & Maintenance:
If any of the inspections described below reveal problems, tag the unit “Out of Service”. Restore the machine to
normal operating condition BEFORE using it again.
A. Before each use, inspect the following components. Each component must be in normal operating condition. To
establish normal operating condition, make a thorough record of the appearance, sound, and function of the various
parts of the wrapping machine when you first receive it. Compare later observations to the record to determine
whether the machine is in normal operating condition.
1. Frame: examine the frame, roller brackets, and handle weldment. Look for damaged welds, warps, cracks, or
other deformations.
2. Casters: examine each caster. Confirm that casters are not severely worn, swivel freely, and that the brakes
firmly engage the wheels.
3. Carriage mechanism: cycle the carriage by raising it to the top of the mast and then lowering it completely. The
carriage should move smoothly and at a uniform rate up-and-down the mast. Watch for binding and listen for
unusual sounds.
4. Fasteners: check bolts and nuts. Make sure all fasteners are tightly connected.
5. Roller bearings: look inside the channel of the mast and examine the roller bearings of the carriage (see FIGS.
1 and 3). Clean the interior of the mast to remove debris that might interfere with the rollers.
B. At least once per month:
1. Wiring: inspect the electrical system and look for loose connections and damage.
2. Clean the machine: remove dirt and other matter from all surfaces.
3. Labels: refer to the “Labeling Diagram” on p. 10. Make sure that all labels are in place and readable.
4. Batteries: remove corrosion from the posts if present.
Battery charger:
Power
switch
Outlet for
charging
cord
Bottom face of charger:
Top face of charger:
Charging
LED
Power
LED
6.3A/250V
fuse
Power
switch
Flanged
inlet for
charging
cord
115-230VAC
selectable