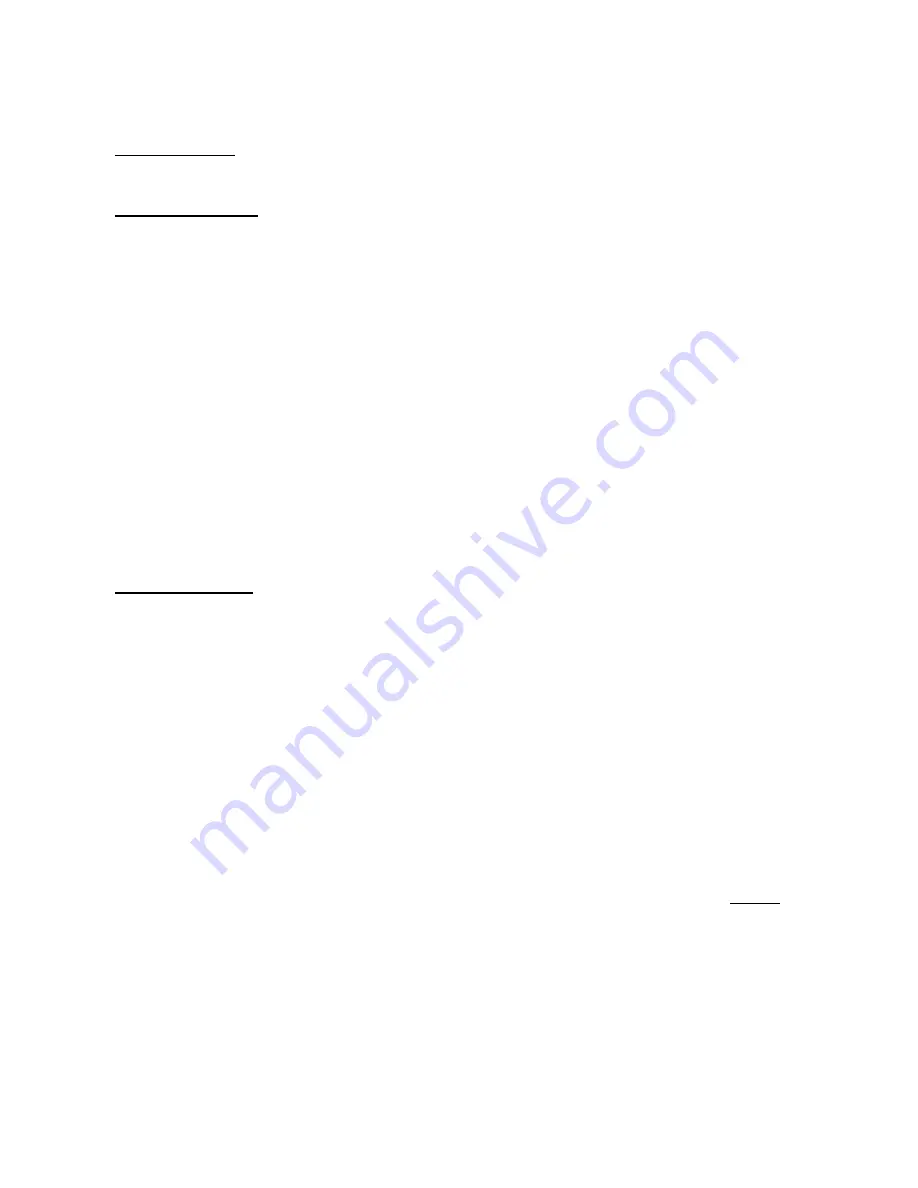
Rev. 1/4/2017
AHSN, MANUAL.doc
Copyright 2017 Vestil Manufacturing Corp.
Page 24 of 26
Inspections and Maintenance:
Apply crane inspection procedures established in 29 CFR 1910.179 (accessible by visiting http://www.osha.gov/ and
navigate to “Regulations”; then to “General Industry” standards, section 1910.179; specifically 29 CFR 1910.179(j)
describes the various inspections the end user is responsible for performing on this crane):
1.
Initial inspection
— before a new or modified crane may be used for the first time, it must be inspected to
insure normal condition. Conduct a “Frequent inspection” as described next.
After the first use, the crane end-user/owner must conduct the following 2 types of inspection:
2.
Frequent inspection
[29 CFR 1910.179(j)(1)(ii)(a)] — Daily to monthly intervals.
The following items shall be inspected for defects at the intervals specifically indicated, including observation
during operation
for any defects which might appear between inspections. All deficiencies such as those listed
shall be carefully examined to determine whether they constitute a safety hazard:
[Inspect daily]
All functional operating mechanisms (wheels/casters, uprights, leg tubes, pins, and
yokes) for maladjustment interfering with proper operation. Verify that the wheels/casters roll smoothly
by pushing/pulling the crane 4-6 feet in one direction.
[Inspect daily]
Look for deterioration or leakage in lines, tanks, valves, drain pumps, and other parts of
air or hydraulic systems. [not applicable]
[Inspect daily (visually); inspect monthly and make
a certification record
,
which includes the date
of inspection, the signature of the person who performed the inspection and the serial number
(or other identifier) of the hook inspected]
Hooks with deformation or cracks. Immediately discard
hooks with cracks or that have a throat opening that is more than 15 percent in excess of normal throat
opening, or that are twisted more than 10° from the plane of the unbent hook.
[Inspect daily (visually); monthly inspection with a certification record which includes the date of
inspection, the signature of the person who performed the inspection and an identifier of the
chain which was inspected]
Hoist chains, including end connections, for excessive wear, twist,
distorted links interfering with proper function, or stretch beyond hoist manufacturer's recommendations.
[Inspect weekly]
All functional operating mechanisms (wheels/casters, uprights, leg tubes, pins, and
yokes, bolts and nuts, including anchor bolts and nuts) for excessive wear.
[Inspect weekly]
Rope reeving for noncompliance with hoist manufacturer's recommendations.
3.
Periodic inspection
[29 CFR 1910.179(j)(1)(ii)(b)] — 1 to 12-month intervals.
Complete inspections of the crane shall be performed at intervals depending upon its activity, severity of
service, and environment, or as specifically indicated below. Perform all of the requirements described for
frequent inspections and the following bulleted items. Carefully examine the crane for any problems such as
those listed below to determine whether they constitute a safety hazard:
Deformed, cracked, or corroded members.
Loose bolts or rivets.
Cracked or worn sheaves and drums.
Worn, cracked or distorted parts such as pins, bearings, shafts, gears, rollers, locking and clamping
devices.
Excessive wear on brake system parts, linings, pawls, and ratchets.
Load, wind, and other indicators over their full range, for any significant inaccuracies.
Gasoline, diesel, electric, or other power plants for improper performance or noncompliance with
applicable safety requirements.
Excessive wear of chain drive sprockets and excessive chain stretch.
Electrical apparatus, for signs of pitting or any deterioration of controller contactors, limit switches and
pushbutton stations.
Cranes not in regular use:
for each of the 3 bullet points below, in addition to the
crane
inspection all rope which has
been idle for a period of a month or more due to shutdown or storage of a crane on which it is installed must be given
a thorough inspection before it is used. An appointed person, whose approval is required before the rope may be
used, must inspect the rope for all types of deterioration. A certification record must be available for inspection. The
record must include at least the date of inspection, the signature of the person who performed the inspection and an
identifier for the rope inspected.
A crane which has been idle for a period of 1 month or more, but less than 6 months, shall undergo a
“Frequent inspection” before being returned to service.
A crane which has been idle for a period of over 6 months shall be given a “Complete inspection” before
placing in service.
Standby cranes shall be given a “Frequent inspection” at least semi-annually (twice per year; 1
inspection each 6 months).