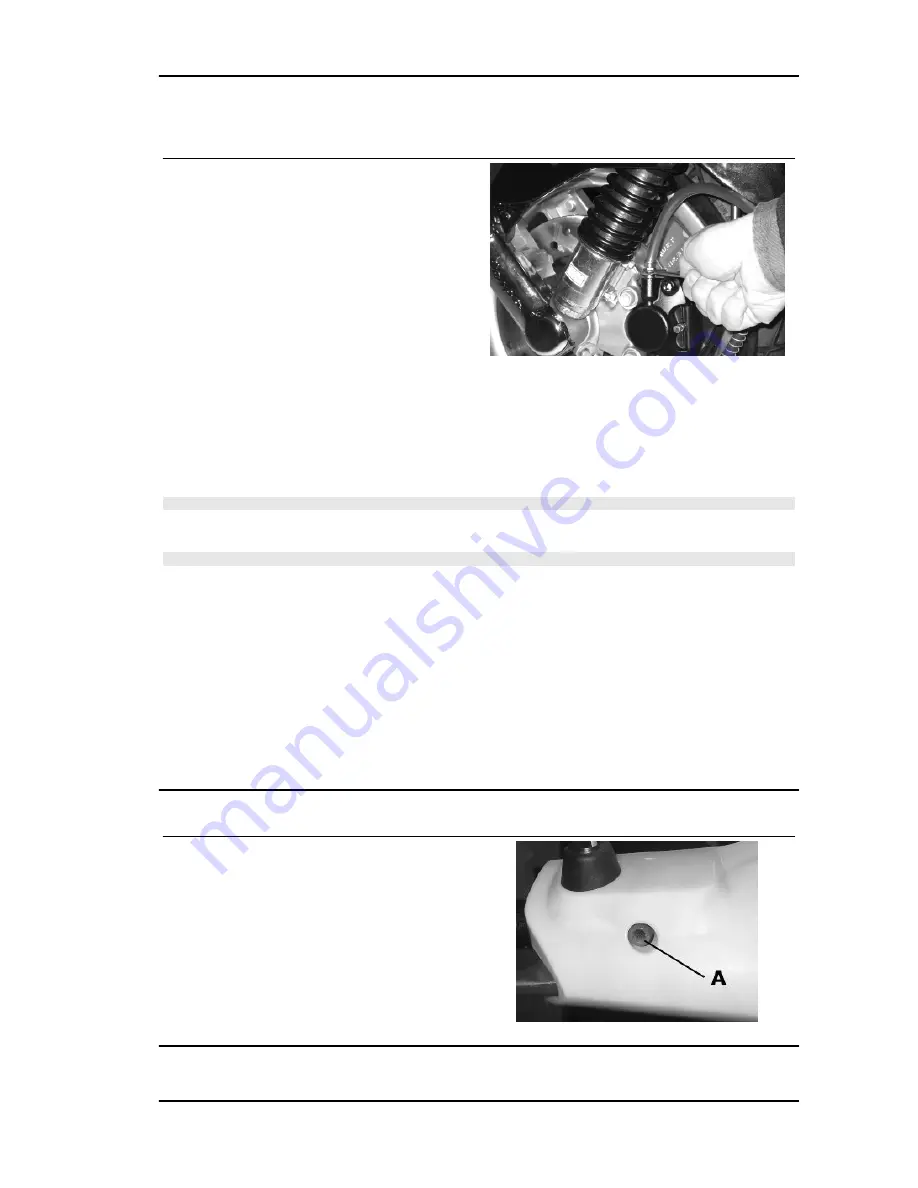
Front
- Remove the rubber cap from the bleed screw.
- Insert a rubber pipe in the bleed screw to permit
the brake fluid to be recovered.
- With the right-hand brake lever, load the system
and bring it up to the required pressure.
- Keeping the right-hand brake lever pulled, loosen
the bleed screw to purge the air. Then tighten the
bleed screw
- Release the brake lever
- Repeat the operation until only brake fluid comes out of the rubber pipe.
- Remove the fluid recovery pipe and refit the rubber cap over the bleed screw.
- Top up the brake fluid to the right level in the reservoir.
If necessary, bleeding can be done using a special vacuum pump
N.B.
DURING PURGING FREQUENTLY CHECK THE LEVEL TO PREVENT AIR GETTING INTO THE
SYSTEM THROUGH THE PUMP.
N.B.
DURING THE BLEEDING OPERATIONS, MAKE SURE THE BRAKE FLUID DOES NOT COME INTO
CONTACT WITH THE BODYWORK SO AS NOT TO DAMAGE IT. FURTHERMORE, DURING THE
BLEEDING OPERATIONS REGARDING THE BRAKE CALLIPERS, MAKE SURE THE BRAKE
FLUID DOES NOT COME INTO CONTACT WITH THE DISC BRAKES AND WITH THE BRAKE
PADS. FAILURE TO OBSERVE THIS PRECAUTION WILL ENDANGER THE PROPER WORKING
AND EFFICIENCY OF THE BRAKING SYSTEM
Specific tooling
020329Y
Mity-Vac vacuum-operated pump
Locking torques (N*m)
System bleed calliper fitting:
20 to 25 Nm
Brake fluid level check
Proceed as follows:
- Rest the vehicle on its centre stand with the han-
dlebars perfectly horizontal;
- Check the level of liquid with the related warning
light «
A
».
A certain lowering of the level is caused by wear
on the brake pads.
Vespa LX 125 - 150 4T Euro 3
Braking system
BRAK SYS - 167
Summary of Contents for LX 125 4T Euro 3
Page 1: ...SERVICE STATION MANUAL 633977 EN Vespa LX 125 150 4T Euro 3 ...
Page 4: ......
Page 6: ...INDEX OF TOPICS CHARACTERISTICS CHAR ...
Page 19: ...INDEX OF TOPICS TOOLING TOOL ...
Page 29: ...INDEX OF TOPICS MAINTENANCE MAIN ...
Page 34: ...INDEX OF TOPICS TROUBLESHOOTING TROUBL ...
Page 40: ...INDEX OF TOPICS ELECTRICAL SYSTEM ELE SYS ...
Page 69: ...INDEX OF TOPICS ENGINE FROM VEHICLE ENG VE ...
Page 73: ...INDEX OF TOPICS ENGINE ENG ...
Page 120: ...Conceptual diagrams Engine Vespa LX 125 150 4T Euro 3 ENG 120 ...
Page 145: ...INDEX OF TOPICS SUSPENSIONS SUSP ...
Page 160: ...INDEX OF TOPICS BRAKING SYSTEM BRAK SYS ...
Page 171: ...INDEX OF TOPICS CHASSIS CHAS ...