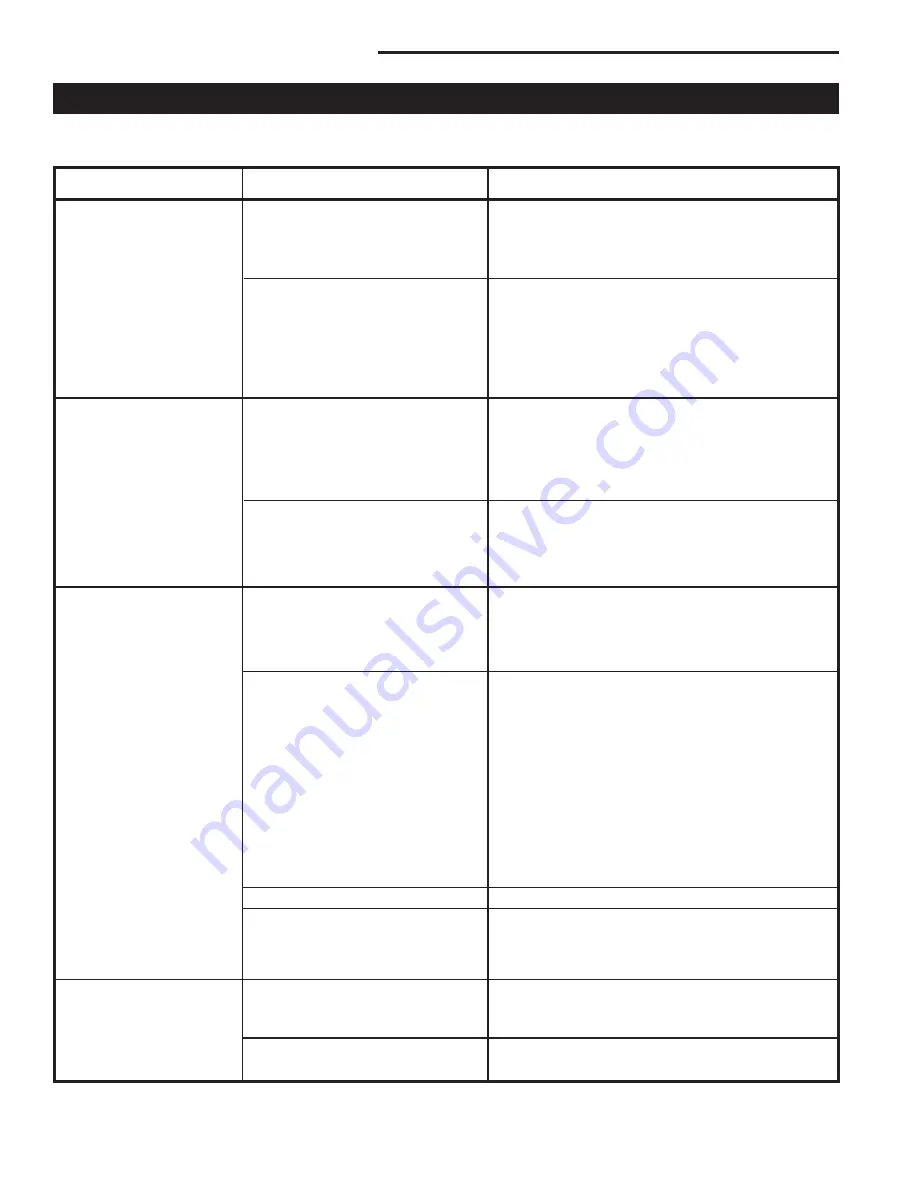
32
Stardance Direct Vent/Natural Vent Gas Heater
20012734
Troubleshooting the Gas Control System (SDDVT Series)
NOTE
: Before trouble shooting the gas control system, be sure external gas shut off is in the “On” position.
SIT NOVA 820 MILLIVOLT VALVE
Symptom
1. Spark ignitor will not light
2. Pilot will not stay lit after
carefully following lighting
instructions
3. Pilot burning, no gas to
main burner
4. Frequent pilot outage
problem
Possible Causes
A. Defective or misaligned electrode
at pilot
B. Defective ignitor (Push Button)
A. Defective pilot generator (thermo-
couple), remote wall switch
B. Defective automatic valve
A. Wall switch or wires defective
B. Thermopile may not be generat-
ing sufficient millivoltage
C. Plugged burner orifice
D. Defective automatic valve opera-
tor
A. Pilot flame may be too low or
blowing (high) causing the pilot
safety to drop out
B. Possible blockage of the vent
terminal
Corrective Action
Using a match, light pilot. If pilot lights, turn off pilot and
push the red button again. If pilot will not light - check
gap at electrode and pilot-should be 1/8” to have a
strong spark.
With the control knob in the pilot position, push the
control knob all the way and hold. Check for spark at
electrode and pilot. If no spark to pilot, and electrode
wire is properly connected, replace the battery in the
ignitor module and try again. Refer to Maintenance
Section. If the problem still exists, replace the ignitor
module box.
Check pilot flame. Must impinge on thermocouple/ther-
mopile. NOTE: This pilot burner assembly utilizes both
a thermocouple and a thermopile. The thermocouple
operates the main valve operation (On and Off). Clean
and or adjust pilot for maximum flame impingement on
thermopile and thermocouple.
Turn valve knob to “Pilot”. Maintain flow to pilot; millivolt
meter should read greater than 10mV. If the reading
is okay and the pilot does not stay on, replace the gas
valve. NOTE: An interrupter block (not supplied) must
be used to conduct this test.
Check wall switch and wires for proper connections.
Jumper wire across terminals at wall switch, if burner
comes on, replace defective wall switch.. If okay,
jumper wires across wall switch wires at valve, if burner
comes on, wires are faulty or connections are bad.
1. Be sure wire connections form thermopile at gas
valve terminals are tight and thermopile is fully
inserted into pilot bracket.
2. One of the wall switch wires may be grounded. Re-
move wall switch wires form valve terminals if pilot
now stays lit, trace wall switch wiring for ground.
May be grounded to fireplace or gas supply.
3. Check thermopile with millivolt meter. Take reading
at thermopile terminals of gas valve. Should read
250-300 millivolts (minimum 150) while holding
valve knob depressed in pilot position and wall
switch “Off”. Replace faulty thermopile if reading is
below specified minimum.
Check burner orifices for debris and remove.
Turn valve knob to “On”, place wall switch to “On”
millivolt meter should read greater than 150mV. If the
reading is okay and the burner does not come on,
replace the gas valve.
Clean and/or adjust pilot flame for maximum flame
impingement on thermopile and thermocouple.
Check the vent terminal for blockage (recycling the flue
gases).