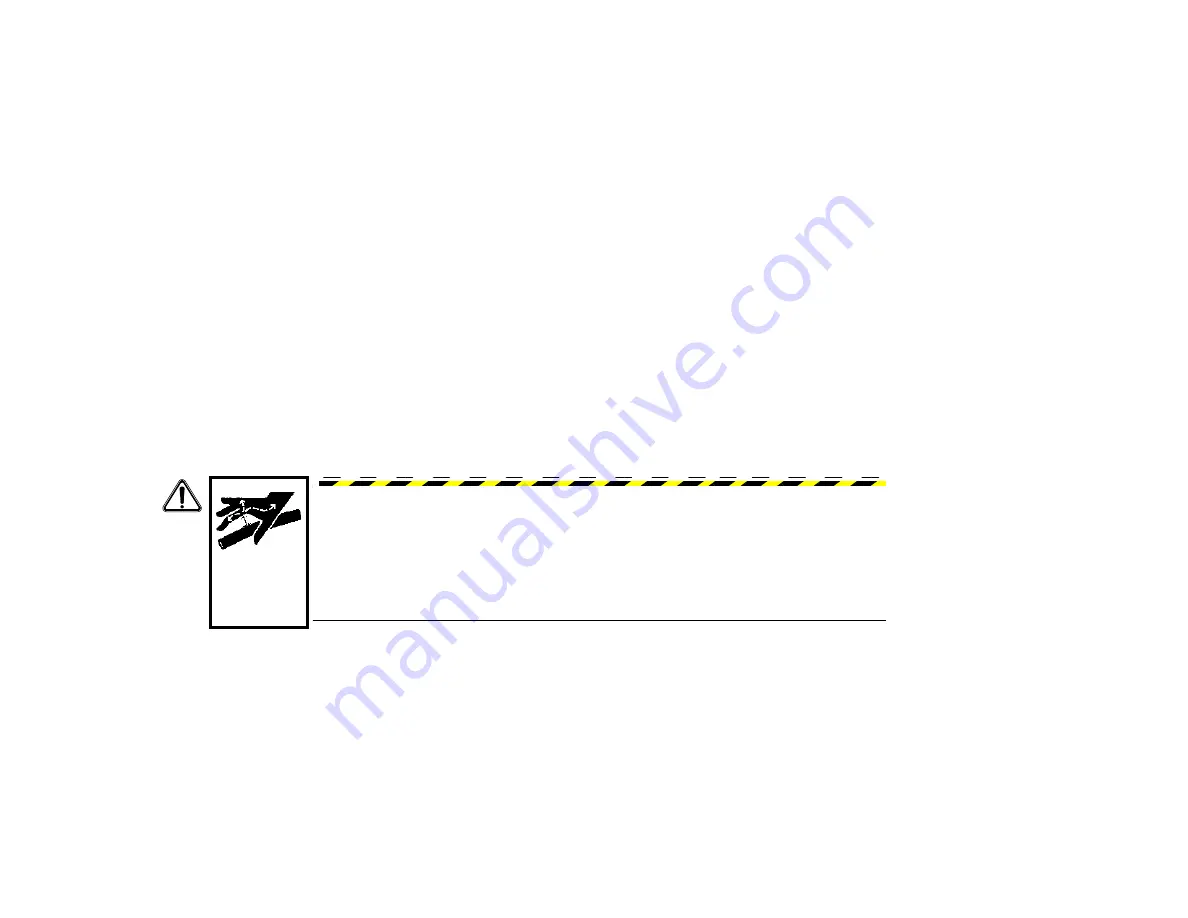
35-2 100 Service Hours
BC1000XL Brush Chipper Maintenance
Safety Signs - Maintain
Safety signs located on your machine contain important and useful information that will help you operate your
equipment safely. Refer to the
Parts Manual
for locations and
Controls
section of the
Operator’s Manual,
for other
information.
To assure that all signs remain in place and in good condition, follow instructions given below:
•
Keep signs clean. Use soap and water - not mineral spirits, abrasive cleaners, or other similar cleaners that
will damage the decal.
•
Replace any damaged or missing signs. When attaching signs, the temperature of the mounting surface
must be at least 40°F (5°C). The mounting surface must also be clean and dry.
•
When replacing a machine component with a sign attached, replace sign also.
•
Replacement signs can be purchased from your Vermeer equipment dealer.
H
YDRAULIC
S
YSTEM
- C
HECK
Ensure all connections are tight and hoses are in good condition before applying pressure to the system.
Check hydraulic lines, fittings, and hose sleeves for leaks or damage. Check for rubbing or pinching of lines
which might damage the line. Repair or replace as necessary. Check hose protective sleeving and replace if worn
or damaged.
WARNING: Pressurized fluid can penetrate body tissue and result in serious injury or
death. Leaks can be invisible. Keep away from any suspected leak. Relieve pressure in the
hydraulic system before searching for leaks, disconnecting hoses, or performing any other
work on the system. If you must pressurize the system to find a suspected leak, use an
object such as a piece of wood or cardboard rather than your hands. When loosening a
fitting where some residual pressure may exist, slowly loosen the fitting until oil begins to
leak. Wait for leaking to stop before disconnecting the fitting. Fluid injected under the skin
must be removed immediately by a surgeon familiar with this type of injury.
3_06
3_01
Summary of Contents for BC1000XL
Page 1: ...BC1000XL Brush Chipper BC1000XL_m3_06 Serial No 5001 Order No 105400V87 Maintenance Manual ...
Page 4: ...This page intentionally left blank ...
Page 8: ...This page intentionally left blank ...
Page 12: ...This page intentionally left blank ...
Page 38: ...This page intentionally left blank ...
Page 52: ...This page intentionally left blank ...
Page 76: ...This page intentionally left blank ...
Page 94: ...This page intentionally left blank ...