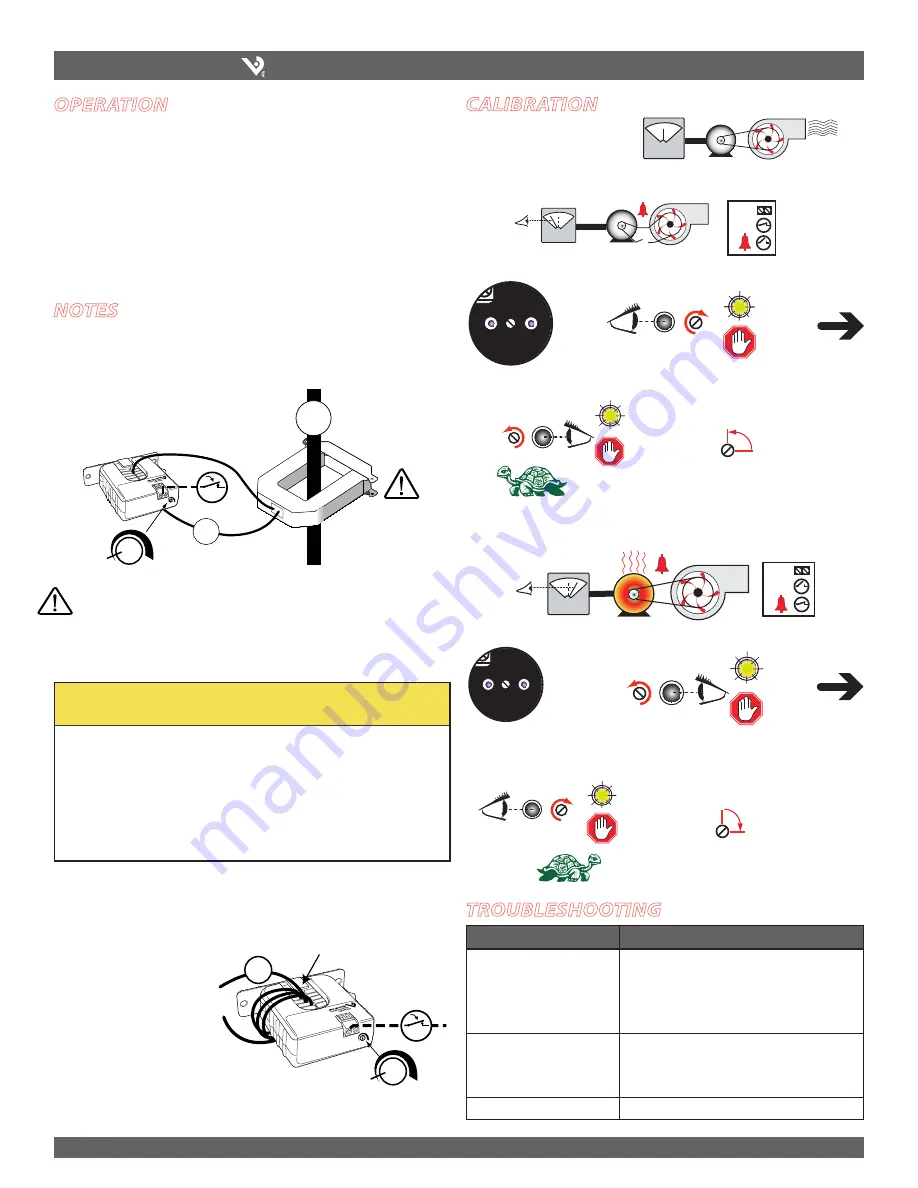
6%2)3).$5342)%3
CURRENT MONITORING
INSTALLATION GUIDE
Z201495-0A
page 2
©2007 Veris Industries USA 800.354.8556 or 503.598.4564 / [email protected]
03071
The H909 is a current-sensitive switching device which monitors current (amperage)
in the conductor passing through it. A change in amperage in the monitored
conductor which crosses the switch (setpoint) threshold plus the hysteresis value will
cause the resistance of the status output to change state, similar to the action of a
mechanical switch. In this model, the setpoint is adjustable through the action of a
twenty (20) turn potentiometer (see the CALIBRATION section). The status output is
suitable for connection to building controllers, or other appropriate data acquisition
equipment operating at up to 30 volts. The H909 requires no external power supply to
generate its output.
operation
notes
troubleshooting
calibration
For load currents less than sensor minimum rating:
Wrap the monitored conductor through the center hole and around the sensor body
to produce multiple turns through the "window." This increases the current measured
by the transducer.
• Controller must be
programmed to account
for the extra turns. e.g., if
four turns pass through the
sensor (as shown) the normal
controller reading must be
divided by 4.
"
" TFOTPSNJO
Y
"
DANGER:
5A CTs CAN pREsENT hAzARDous volTAGEs.
INsTAll CTs IN ACCoRDANCE wITh mANufACTuRER's
INsTRuCTIoNs.
TERmINATE ThE CT sECoNDARy bEfoRE ApplyING CuRRENT.
H6800-5A CT
"
"
"
"
"
> 135A (H909 max.)
For load currents greater than sensor maximum rating:
Use a 5 Amp (H681x series) Current Transformer (CT) as shown.
Problem
Solution
No Reading at Controller
• Check sensor calibration (see above)
• Check for control voltage at sensor (<120V)
• Check for amperage in monitored conductor (> 2.5A)
• Assure that sensor core mating surfaces are clean and
that the core clamp is completely closed
Setpoint screw has no stops
The setpoint screw has a slip-clutch at both ends of its
travel to avoid damage. Twenty turns CCW will reset
the sensor to be most sensitive. Repeat calibration
above.
Both LEDs are lit
Setpoint screw is too far clockwise. See solution above.
Establish normal load conditions.
A. To monitor under-current (belt loss, coupling shear, status)
"
OK!
!
OK!
"
OK!
Turn setpoint screw clockwise until Status OPEN LED turns ON.
S-l-o-w-l-y turn the screw counter-clockwise until the Status CLOSED LED just turns ON.
Turn the screw an
additional 1/4 turn
counter-clockwise for
operational margin.
B. To monitor over-current (mechanical problems, seized impeller)
"
OK!
!
3.
Turn the setpoint
screw an additional
1/4 turn clockwise for
operational margin.
1.
Turn setpoint screw counter-clockwise
until Status CLOSED LED turns ON.
2.
S-l-o-w-l-y turn the setpoint screw clockwise
until the Status OPEN LED just turns ON.
CAUTION
RIsK of EQuIpmENT DAmAGE
• Derate the product’s maximum current for the number of turns
through the sensing window using the following formula.
Rated Max. Amps ÷ Number of Turns = Max. monitored Amps
e.g. : 100A ÷ 4 Turns = 25 Amps max. in monitored conductor
• Failure to follow these instructions can result in overheating
and permanent equipment damage.
OK!
45"564
OK!
45"564
4FUQPJOU
4UBUVT
0QFO
4501
4FUQPJOU
4UBUVT
0QFO
4UBUVT
$MPTFE
4FUQPJOU
4UBUVT
$MPTFE
4501
4FUQPJOU
3.
+
Find Setpoint
adjustment screw
1.
2.
4FUQPJOU
4UBUVT
$MPTFE
4501
4FUQPJOU
4UBUVT
0QFO
4UBUVT
$MPTFE
Find Setpoint
adjustment screw
4FUQPJOU
4UBUVT
0QFO
4501
+
4FUQPJOU