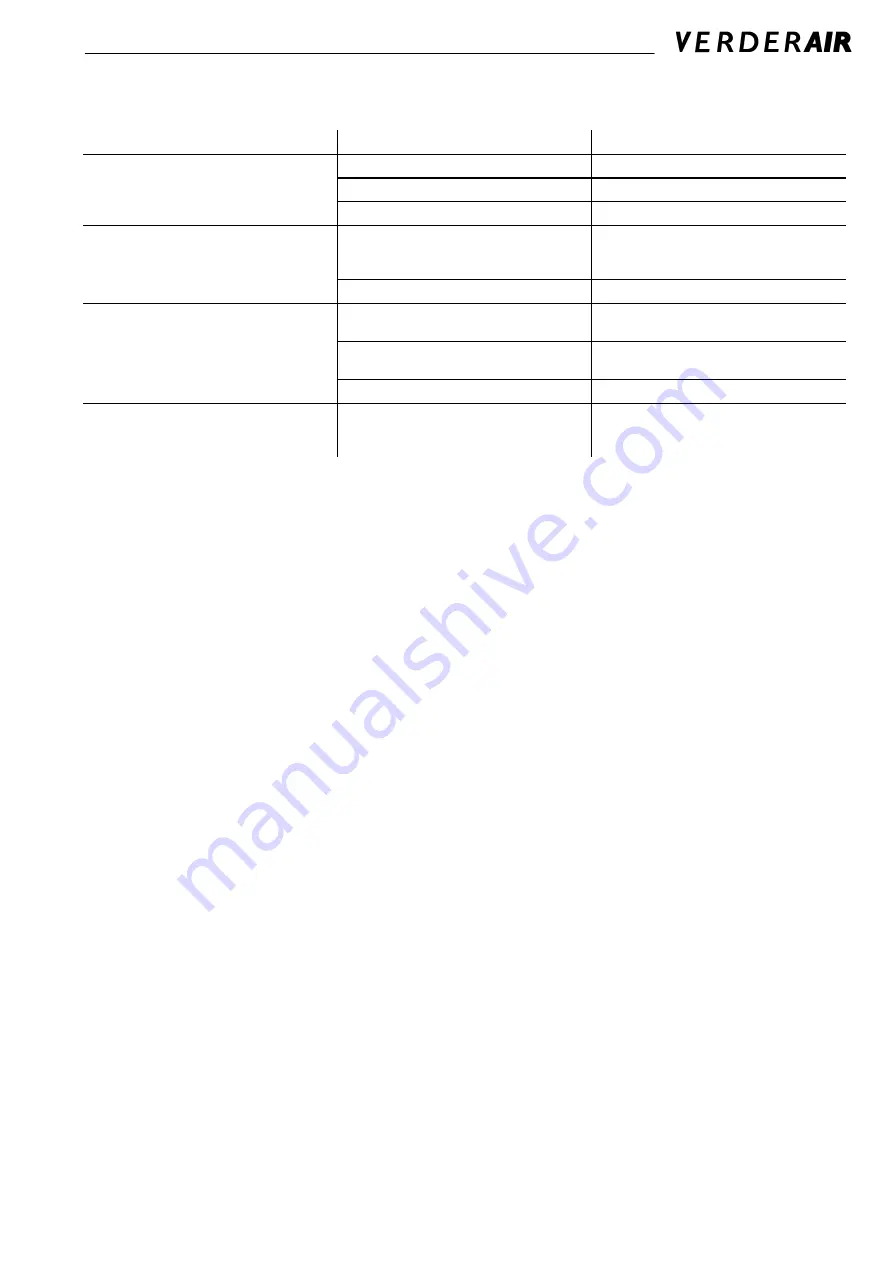
819.4470
13
Troubleshooting
PROBLEM
CAUSE
SOLUTION
Fluid in exhaust air.
Diaphragm ruptured.
Replace. See pages 17–19.
Loose diaphragm shaft bolt (107).
Tighten or replace (pages 17–19).
Damaged o-ring (108).
Replace. See pages 17–19.
Pump exhausts excessive air at stall.
Worn air valve block (7), o-ring (6),
plate (8), pilot block (18), u-cups (10), or
pilot pin o-rings (17).
Repair or replace. See pages 14–15.
Worn shaft seals (402).
Replace. See pages 17–19.
Pump leaks air externally.
Air valve cover (2) or air valve cover
screws (3) are loose.
Tighten screws. See page 15.
Air valve gasket (4) or air cover gas-
ket (22) is damaged.
Inspect; replace.
See pages 14–15, 20–21.
Air cover screws (25) are loose.
Tighten screws. See pages 20–21.
Pump leaks fluid externally from ball
check valves.
Loose manifolds (102, 103), damaged
seal between manifold and seat (201),
damaged o-rings (202).
Tighten manifold bolts (106) or replace
seats (201) or o-rings (202). See
page 16.