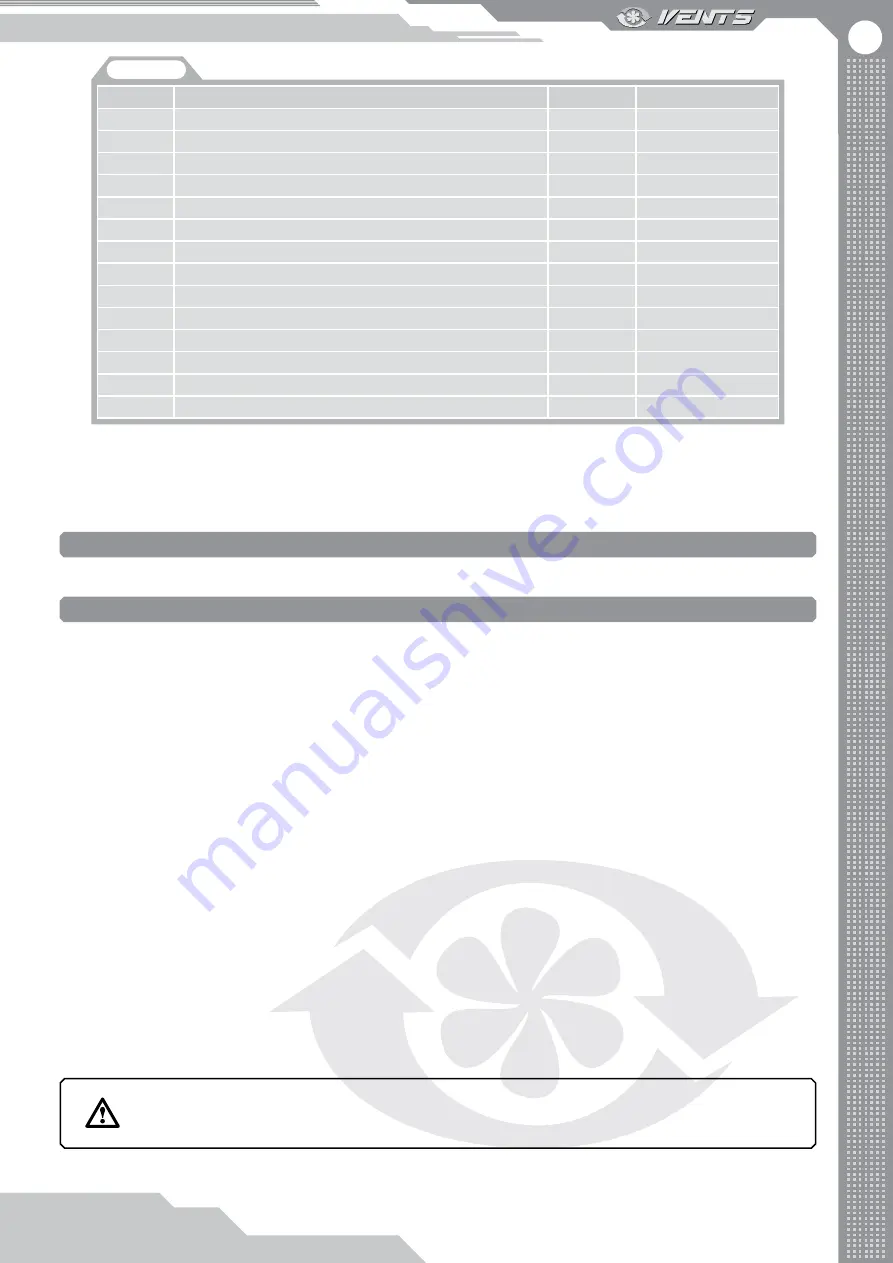
19
UNIT CONTROL
The unit is equipped with a built-in electronic automatic control unit and a control panel (ref. Control panel user’s manual).
MAINTENANCE
Maintenance operations of the unit are required 3-4 times per year. Maintenance includes regular cleaning and the following
operations:
1. Filter maintenance (3-4 times per year).
Dirty filters increase air resistance in the system and reduce supply air volume. The filters require cleaning not less than 3-4 times per
year. Vacuum cleaning is allowed. After two consecutive cleanings filters must be replaced. Contact the unit Seller to purchase new
filters.
2. Heat exchanger inspection (once per year).
Some dust may accumulate on the heat exchanger block even in case of regular maintenance of the filters. To maintain the high heat
exchange efficiency, regular cleaning is required. To clean the heat exchanger pull it out of the unit and clean it with flush it with warm
detergent solution. After cleaning install the dry heat exchanger back to the unit.
3. Fan inspection (once per year).
Even in case of regular maintenance of the filters, some dust may accumulate inside the fans and reduce the fan performance and
supply air flow.
Clean the fans with a soft brush or cloth. No water and abrasive detergent, sharp objects or solvents are allowed for cleaning to prevent
the impeller damage.
4. Condensate drainage inspection (once per year).
The drain pipes may get clogged with the extracted particles. Pour some water inside the drain pan to check the pipe for clogging.
Clean the U-trap and the drain pipe if required.
5. Supply air flow control (twice per year).
Leaves and other pollutions can clog the supply air grille and reduce the unit performance and supply air volume. Check the supply
grille twice per year and clean it as required.
6. Ductwork system inspection (once in 5 years).
Even if you follow all the listed maintenance guidelines, some dust can get accumulated inside the air ducts and reduce the unit
performance. Duct maintenance means regular cleaning or replacement.
5. Exhaust louvre shutters and intake diffusers cleaning (as required).
Remove the diffusers and the grilles and wash them with warm water and mild detergent solution. Do not change locations of the
diffusers and the louvre shutters.
INSPECT THE HOOD AND THE INTAKE GRILLE ONCE PER YEAR AND CLEAN AS
REQUIRED.
* - The appliances are not supplied with the unit, are available on the separate order.
** - Cable length from P1 must not exceed 10 meters.
** - Max. connecting cable length is 20 m!
**** - The system can operate without a heat medium pressure relay in the DD1 heater, in this case a jumper should be installed
between the contacts 11 and 12 for VUT 800…1000 WH or between the contacts 14 and 15 for VUT 1500…2000 WH.
Table 4
Design.
Name
Type
Wire***
M1
Supply fan
max. 1 kW
M2
Extract fan
max. 1 kW
M3*
Circulation pump
max. 0.3 kW
3x0,75 mm
2
DD1*
Pump dry run protection relay****
NC
2x0,75 mm
2
SM1*, SM2
Air damper actuator
LF 230
2x0,75 mm
2
SM4*
Water heater valve actuator
LR 24 SR
3x0,75 mm
2
SM3
Heat exchanger bypass damper actuator
LM 230
PK1*
Contact from fire alarm panel
NO
2x0,75 mm
2
P1*
Control panel**
SAS908PIT
TE1
Intake air temperature sensor
ST-01
TE2
Exhaust air temperature sensor
STa-02
TE3
Return heat medium temperature sensor
STw-02
TE4
Water heater freeze protection sensor
STw-02
TE5
Supply air temperature sensor
STa-02