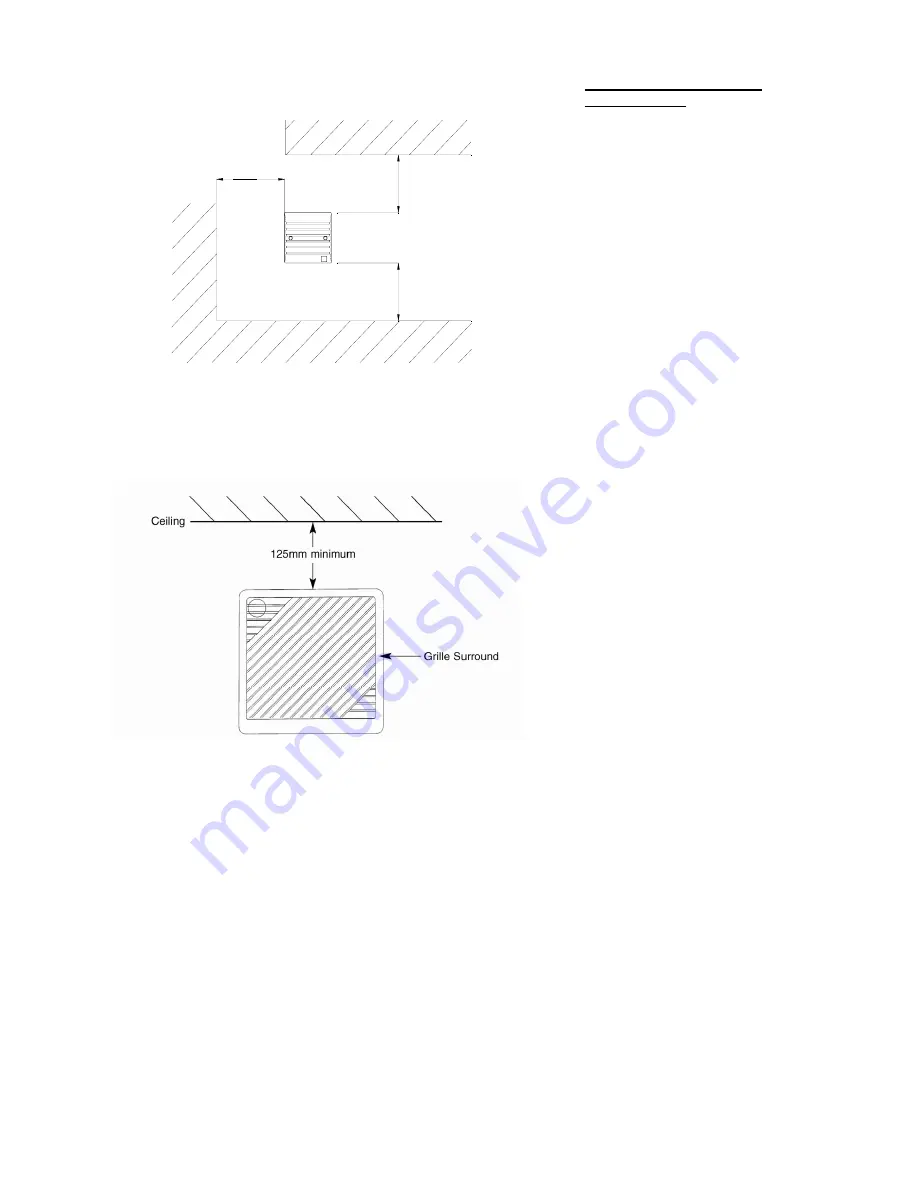
Fig.2
Fig.3
2.0 Site Requirements
2.1 Information
1. The unit is designed for installation in
external walls with a thickness of up to 310mm.
For wall thicknesses above 310mm, the ‘L’
version of the appropriate model must be used
(see page 12 ). The ‘L’ models are suitable for wall
thicknesses up to 425mm.
2. The unit must be sited and connected by a
suitably competent person and be in
accordance with current U.K. Building
Regulations and I.E.E. Wiring Regulations (BS
7671).
3. The unit must be installed in conjunction with
the separate power supply supplied,
which is intended for permanent connection to
the mains electrical supply. The unit and the
power supply are intended for fixed
wiring installation.
4. The power supply requires free air
circulation for effective operation It must not be
recessed into the mounting surface or covered
with any form of insulation, which might be used in
a ceiling or roof void. The unit must be sited such
that the ambient temperature will not exceed 40°C.
please ensure that the air vents on the enclosure
are not blocked or covered up.
5. Wiring to the unit in the U.K. must be via
a switched fused spur.
6. The spur should have a minimum contact gap
of 3mm in all poles.
7. Ensure that the mains electrical supply is
compatible with the rating label attached to the
product.
8. The unit must be sited such that the ambient
temperature will not exceed 40°C.
9. Do not site the appliance in the vicinity of
excessive levels of airborne oil or grease. or
directly over a cooker.
10. If the unit is installed in a room containing a
fuel burning appliance, the installer must ensure
that air replacement is adequate for both
appliances.
11. The unit must not be installed at a level
below 500mm from the floor.
12. The internal grille surround must be sited at
least 125mm away from the room ceiling (Fig. 3).
and 300mm away from any adjacent vertical
surface.
13. The external cowl of the unit must be sited
at least 500mm away from any flue of gas or
solid fuel appliances. This is to avoid back flow
of gases entering the room.
14. All safety regulations and requirements
must be strictly followed to prevent hazards to
life and property both during and after
installation and during subsequent maintenance
or servicing.
15. Ensure the mains electrical supply is
switched off before commencing installation or
maintenance.
2.0 Site Requirements
50mm minimum
50mm minimum
50mm minimum
Summary of Contents for HR25 Solo
Page 15: ......