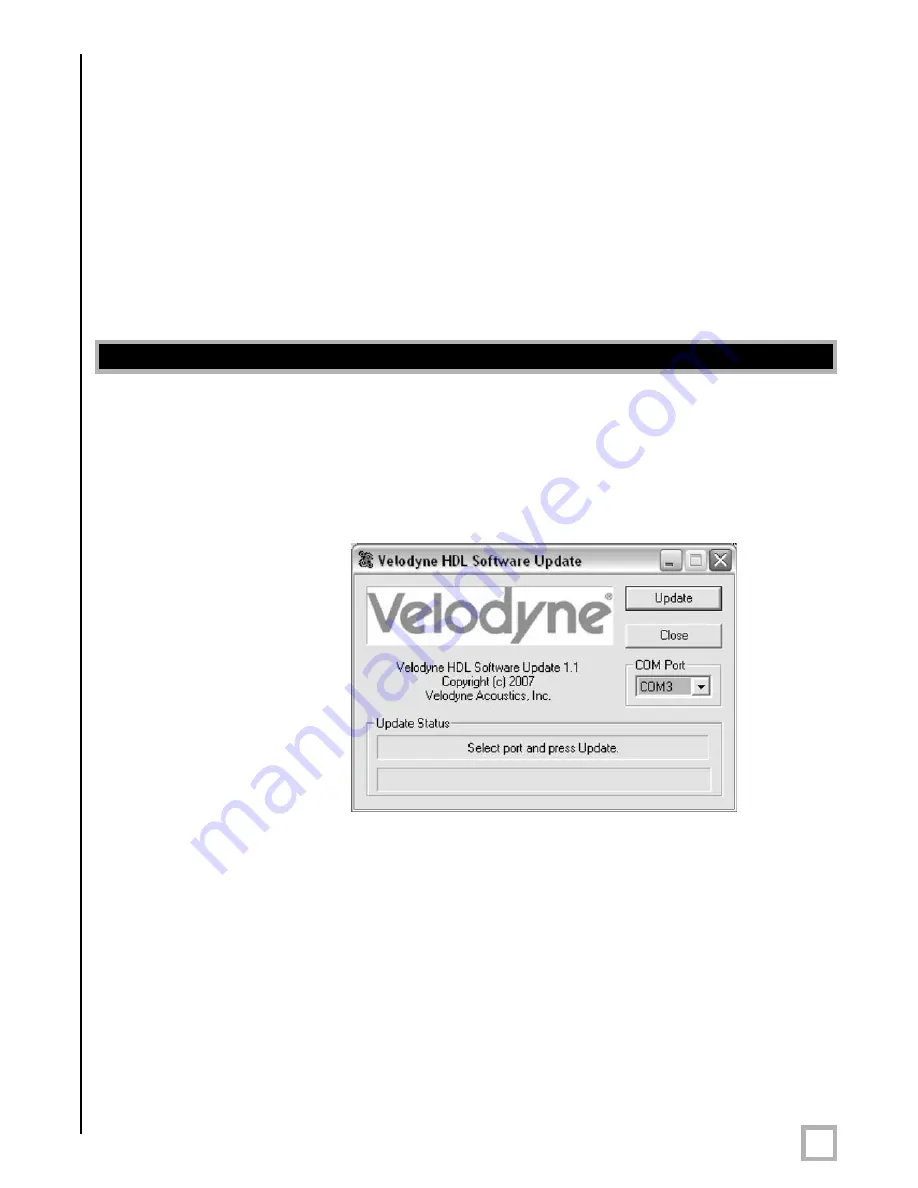
8
.
w w w . v e l o d y n e . c o m
HDL-64E User’s Manual
C o n t r o l l i n g t h e S p i n R a t e
The HDL-64E can spin at rates ranging from 300 RPM (5 Hz) to 900 RPM (15 Hz). The default
is 600 RPM (10 Hz). Note that changing the spin rate does not change the data rate – the
unit will send out the same number of packets (at a rate of one million data points per second)
regardless of spin rate. The image resolution will increase or decrease depending on rotation
speed. See Appendix B for angular resolution figures for various spin rates.
To control the HDL's spin rate, connect the serial cable to an available RS-232 COM port and
issue a serial command of the format #HDLRPMnnn$ where nnn is an integer between 300
and 900. The characters are case sensitive and must be CAPS. The HDL-64E will adopt the
new spin rate. Use the following serial parameters: Baud 9600, Parity: None, Data bits: 8,
Stop bits: 1. The HDL-64E has no echo back feature, so no serial data will be returned from
the HDL-64E.
Velodyne may issue firmware updates from time to time. To apply the update, connect the
DB9 RS-232 cable to a standard Windows-compatible PC’s serial port. The HDL-64E must
be powered up and spinning during the update.
Execute the file supplied by Velodyne – all the software and firmware is included to update the
unit. Once the file is executed, the following screen will appear:
Figure 5. HDL software update
screen capture.
Press update and the unit will update. If the update was successful, the unit will begin to spin
down for a few seconds then power back up with the new firmware running. If the first update
is not successful, it is recommended to try the update again several times before seeking
assistance from Velodyne.
NOTE: The entire new firmware is uploaded and checksummed before being applied to the flash
memory inside the HDL-64E. If the checksum is corrupted, no software update occurs. This
protects the unit in the event of power or data loss during the firmware update.
Firm ware Updat e