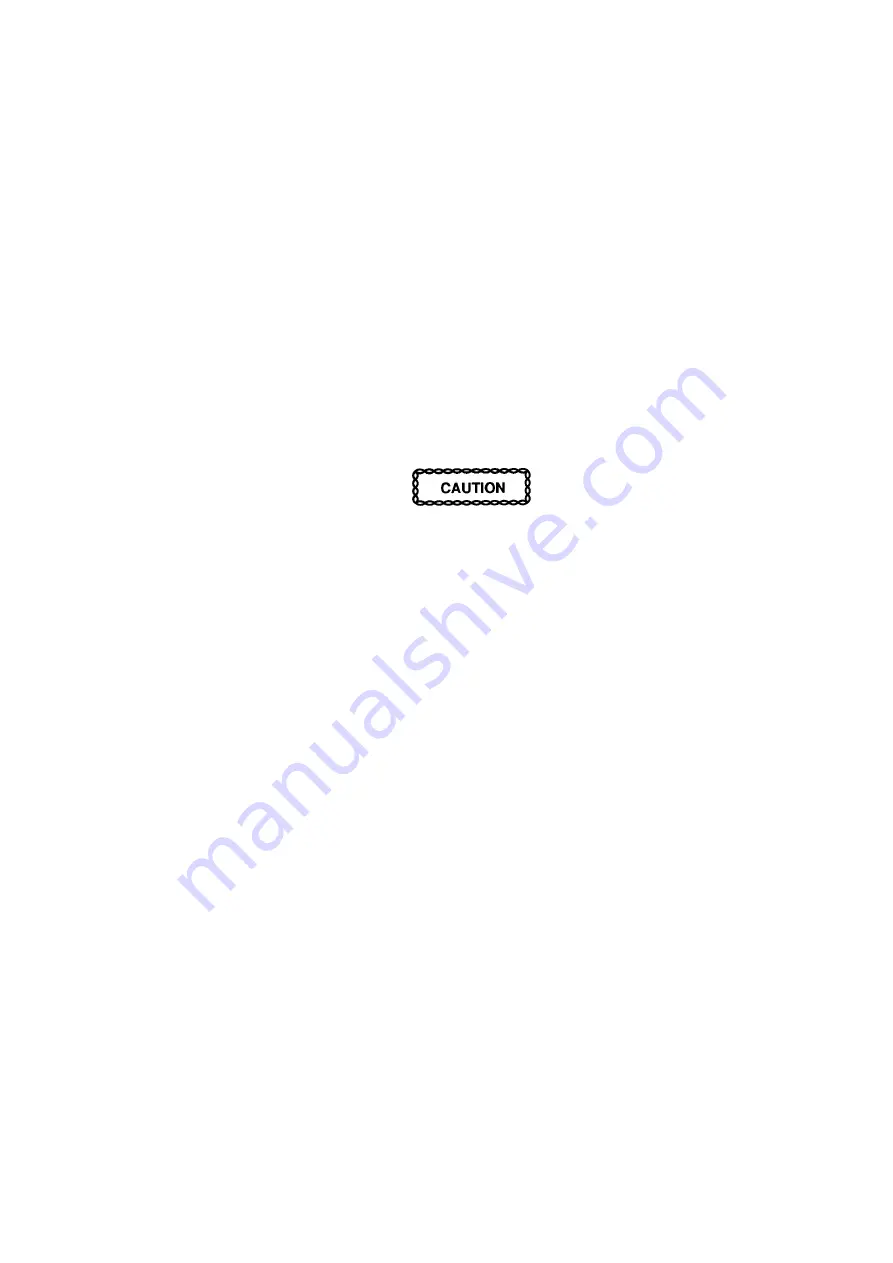
UNCONTROLLE
D IF P
R
INTE
D
ELECTRICAL AND MECHANICAL
ENGINEERING INSTRUCTIONS
VEHICLE H 983
Issue 1, Jul 11
11
d.
Inspect the bearing cone for:
(1)
discolouration of the tapered rollers;
(2)
chipping or scoring of the case hardening;
(3)
flaking of the case hardening;
(4)
acceptable wear limits on the wear back surface (the large end of the tapered roller); and
(5)
the condition of the tapered roller cage.
NOTE
Discard the bearing cup and cone if any defects are found. These must be replaced
as a matched set.
49.
Bearing Cup Installation.
To install bearing cups proceed as follows:
a.
Check that the wheel hub is free from any damage.
b.
Pack the bearing cones with grease.
c.
Place a faint smear of grease around the inner surface of the hub through which the cup is to pass.
Drifts used for fitting bearing cups must be free of all burrs and jagged edges,
to prevent brass chips being dislodging into the wheel hub and bearings.
d.
Place the bearing cup (Figure 3, 4 or 6), smaller internal diameter innermost, in position on the hub and
drive it into position using a suitable hammer and brass drift.
NOTE
Make sure that the drift is placed in alternate positions around the cup, to ensure that
the cup is driven evenly into the hub. The cup is fully in position when a solid
metallic knock is heard in all positions around the cup.
e.
Inspect the bearings for brass chips (remove if found).
50.
Hub Seal Installation.
Install the hub seal as follows:
a.
Check that the stub axle land is clean and free from dirt and other foreign material.
b.
Coat the axle land with a thin coat of Loctite 515 Forma gasket compound, Hylamar or other brand
name non-hardening gasket material
c.
Drive the inner hub seal (Figure 3, 1 and 2) into position on the stub axle using the hub seal installing
tool (Table 2, Serial 1).
NOTE
The hub seal is pushed into the wheel hub during installation of the wheel hub.