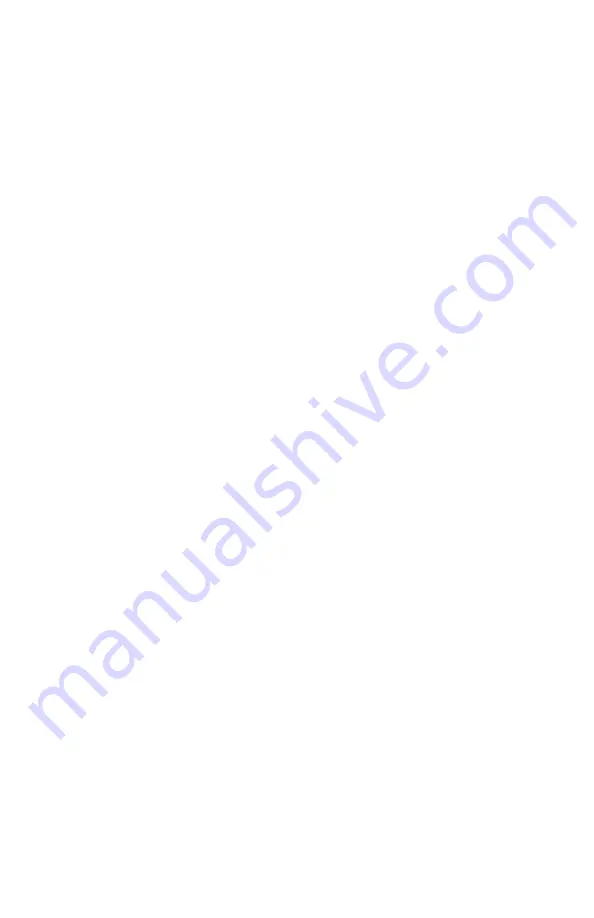
7
CLEANING AND MAINTENANCE
TABLET HOPPER
1. Unplug both of the solenoid valves and turn the water supply to the feeder off.
2. Open the top and remove any remaining tablets in the hopper and place into a clean dry pail.
3. Rinse, brush, and clean out the tablet hopper and tablet tray with water. The entire tablet hopper
can be removed by disconnecting the solenoid valve plug adapter before lifting the hopper off of
the solution tank.
SOLUTION TANK
1. Disconnect the solenoid valve plug adapter. Lift off the Tablet Hopper to gain access to the
solution tank. Alternatively, limited access to the lower solution tank can be gained by removing
the access panel adjacent to the level switch assembly.
2. Rinse, brush and clean out the solution chamber with fresh water.
3. Rinse brush and clean all feeder parts with fresh water. The float assembly and other parts can
be damaged with rough handling. Use caution when cleaning these parts.
4. When all parts have been cleaned, the interior of the tubing, venturi check valve and venturi can
be cleaned by adding a mild solution of acid to the feeder and allowing it to be drawn through the
piping by the action of the venturi.
DANGER:
Be sure that all chlorine has been removed
from the feeder prior to addition of any product containing acid.
Mixing of chlorine and
muriatic acid can produce hazardous conditions leading to personal or bodily injury.
5. After addition of acid to the feeder, allow the feeder to operate with fresh water for several cycles
to remove all acid from the feeder. All acid must be removed from feeder prior to the addition of
chlorine.
6. Refill feeder with appropriate amount of Vantage Calcium Hypochlorite Tablets, replace feeder lid,
plug in both solenoid valves, turn on water and adjust flow rate for proper chlorine output.
7. Check feeder operation to ensure feeder is working properly.