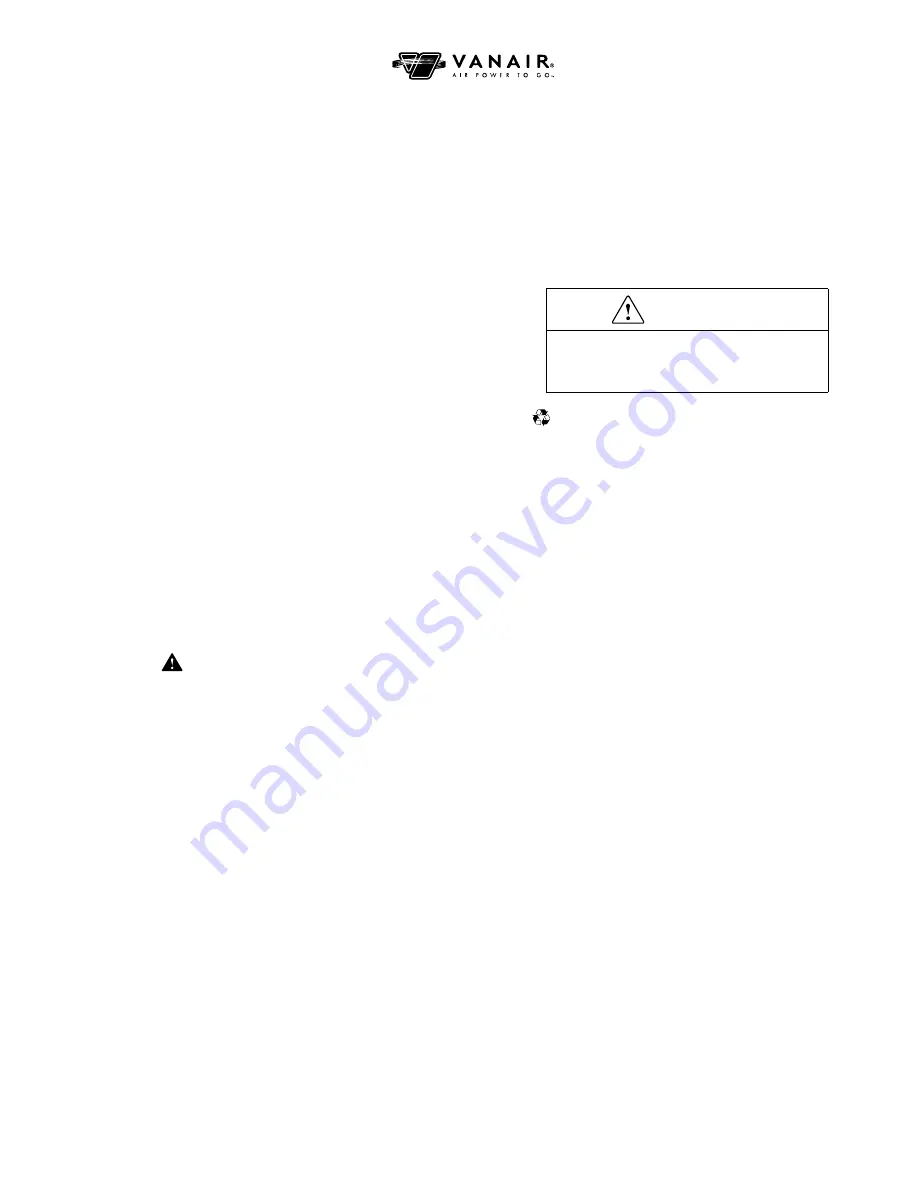
VIPER DIESEL
SECTION 1: SAFETY
090058-OP_r0 (AUGUST-2014)
PAGE - 3
VANAIR MANUFACTURING, INC.
(800) 526-8817 • www.vanair.com
•
Keep the equipment clean when
performing maintenance or service
actions. Cover openings to prevent
contamination.
•
DO NOT
operate the compressor if
cooling air is not available (fan/cooler not
operating) or if lubricant levels are below
their specified minimum levels.
•
Ensure all plugs, hoses, connectors,
covers, and other parts removed for
maintenance actions are replaced
before applying power to the
compressor.
•
Avoid touching hot surfaces and
components.
•
Ensure that electrical wiring, terminals;
hoses and fittings are kept in serviceable
condition through routine inspections
and maintenance. Replace any
damaged or worn components.
•
DO NOT
install safety devices and/or
replacement parts other than authorized
Vanair
®
replacement parts.
•
Keep personnel out of line with, and
away from discharge opening of valves,
hoses and tools.
•
Immediately clean up any lubricant or
spills.
1.3.4
SAFETY DECALS
Safety decals are placed onto, or located
near, system components that can present a
hazard to operators or service personnel. All
pertinent decals listed in
Section
7.11A,
Decal Locations
are located near a
component, which is subject to respect in
terms of safety precautions. Always heed the
information noted on the safety decals.
1.4
DISPOSING OF MACHINE
FLUIDS
Always dispose of machine fluids under the
guidance of all applicable local, regional and/
or federal law.
Vanair
®
encourages recycling when allowed.
For additional information, consult the
container label of the fluid in question.
WARNING
DO NOT REMOVE OR COVER ANY
SAFETY DECAL. Replace any safety
decal that becomes damaged or illegible.