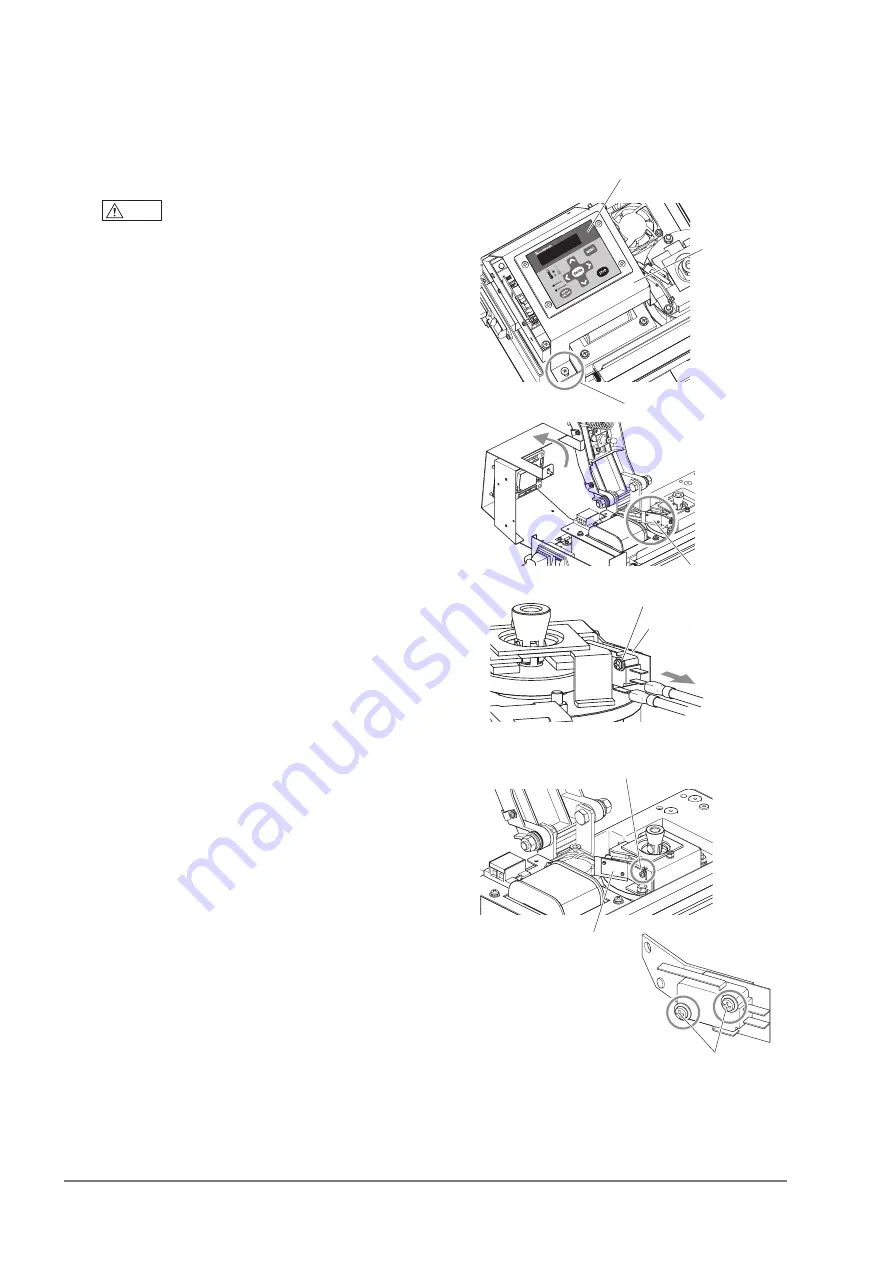
MS-350 NP Operating Instructions Ver 4.02E
34
Essential tools: Phillips screwdriver
The microswitch is also sold individually.
1
Remove the screw that fix the control unit
frame as in the right illustration.
2
Raise the control unit frame and tilt it away
from you as in the right illustration.
3
Disconnect the harnesses attached to the
microswitch.
4
Remove the microsiwtch bracket by loosening
the screw in the right illustration.
Remove the microswitch from the bracket by
loosening two screws.
5
Attach the new microswitch to the microswitch
bracket with two screws removed in 4.
6
Reattach the microswitch bracket to the initial
position.
7
Insert the harnesses to the microswitch.
8
Return the control unit frame to the initial
position and fix it with the screw removed in 1.
10-8 Microswitch replacement
Remove the screw
Control unit
Control unit frame
Remove the screw
Remove the screws
Microswitch bracket
Microswitch bracket
Microswitch bracket
Microswitch
Warning
Make sure to disconnect the power plug
from the outlet before replacing the
microsiwtch.