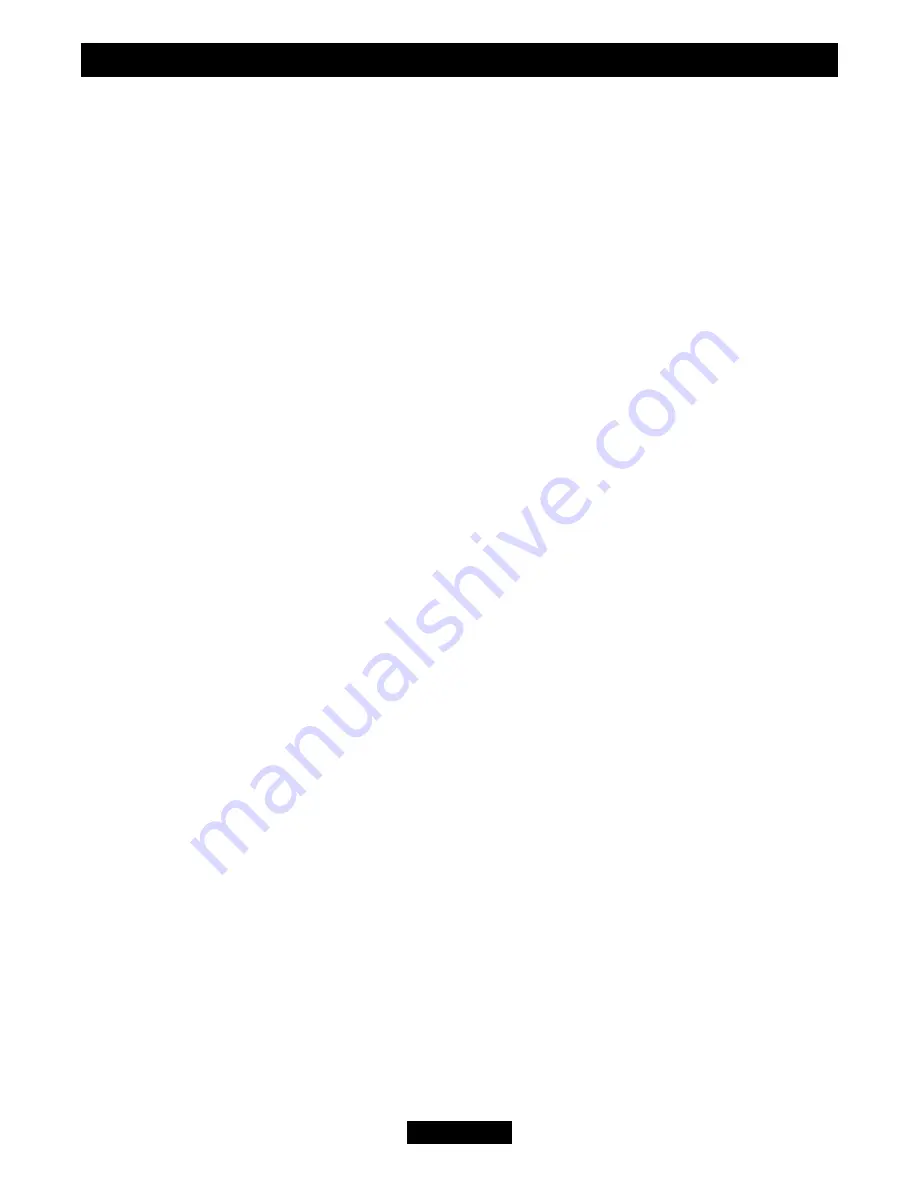
12.10 To remove the shut-off valve assembly.
1.
Remove the ‘T’ piece as in section 12.9.
2.
Detach the thermocouple and loosen the interrupter block from the valve, once
loosened it will be possible to remove the thermocouple leads. Pull the tags and not
the leads as this can cause damage. Remove the interrupter block.
3.
Detach the pilot pipe from the valve.
4.
Remove and fit the brass nut from the top of the removed valve onto the
replacement.
5
. Refit in the reverse order. If replacing the shut-off valve, remove the locking nut
from the top of the valve and fit it to the replacement valve.
When refitting the thermocouple and interrupter block, make sure that the microswitch
wires are properly secured to give a good electrical contact.
12.11 To grease the gas flow rate controller.
1.
Remove the fascia as in section 12.2.
2.
Disconnect the slider control by removing the knurled screw from the connector
arm.
3.
Remove the nut and washer securing the control pivot bracket to the controller at
the front. Support the pivot bracket while removing the nut to prevent possible
damage to the microswitch.
4.
Remove the hexagonal bolt securing the control pivot bracket to the controller at
the rear.
5.
Remove the control pivot bracket.
6.
Remove the hexagonal nut securing the controller to the mounting bracket.
7
. Loosen the brass nut that holds the shut-off valve to the securing bracket, rotate
the bracket forward and clear of the shut-off valve.
8.
Remove the two screws from the head of the tap.
9.
Rotate the plug and pull it out of the tap.
10.
Clean and grease the plug lightly with suitable grease. Do not apply excessive
grease. Particularly, make sure that the gas ports are not restricted by grease.
11.
Push the plug back into the tap body. Line up the slot in the plug with the mark
previously made on the tap body.
12.
Reassemble in the reverse order making sure that the components are correctly
engaged. Check the operation of the tap.
12.12 To remove the slider mechanism.
1.
Remove the fascia as in section 12.2.
2.
Disconnect the slider control by removing the knurled screw from the connector
arm.
3.
Unscrew and remove the two screws from the left side of the slider body.
4.
The slider mechanism can now be removed from the fire. To do this move the
bottom of the mechanism to the right and upward, this will allow the slider button to
pass through the lower opening in the slider cover.
Page 29
©
GDC Group Ltd. 2011
INSTALLER GUIDE