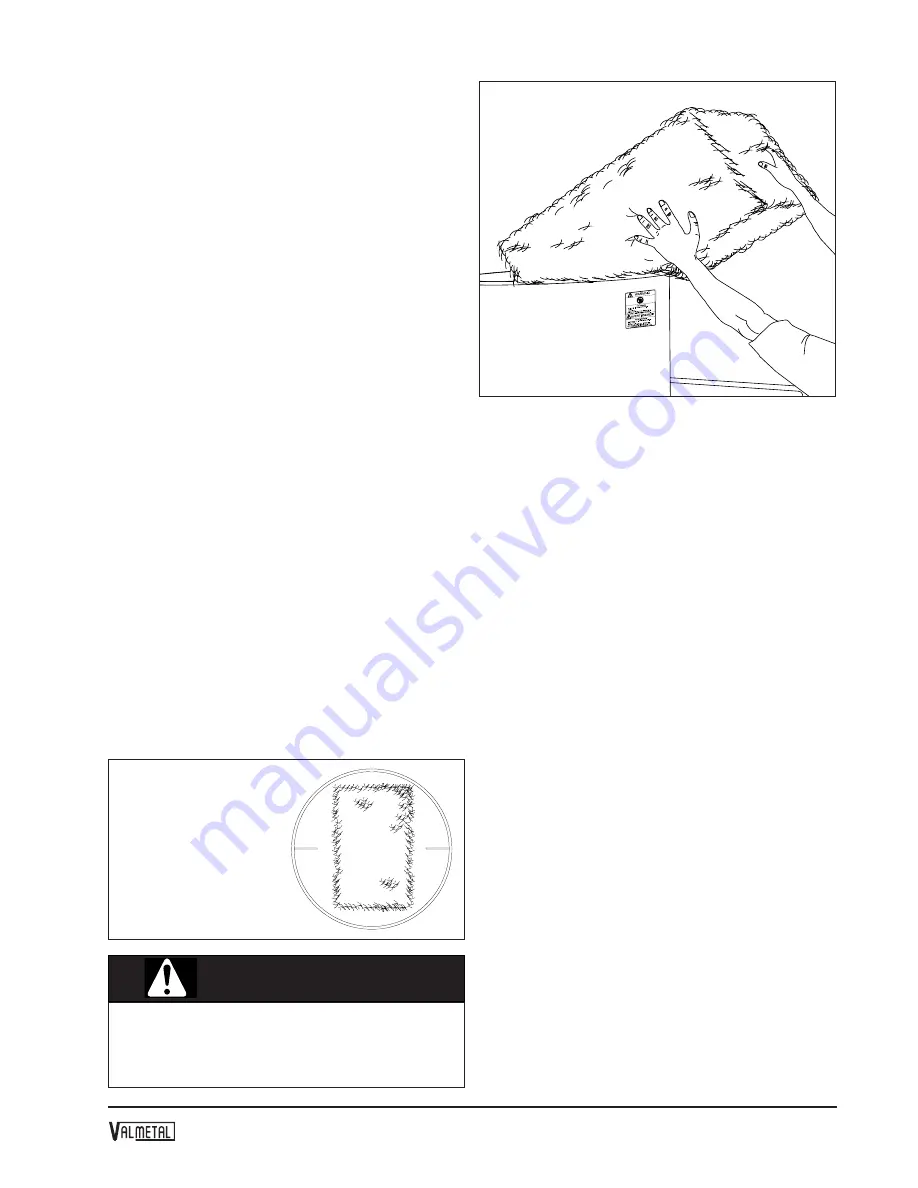
15
4.6
OPERATING
The Valmetal Self propelled bedding chopper can
quickly and efficiently shred compacted bulk material
to distribute and spred evenly over a surface
. When
using the machine, follow these procedures:
IMPORTANT!
New operators or people who have not operated the
unit for a period of time should review the location and
function of all controls before starting. It is recom-
mended that they move the machine to a large open
area and practice operating. This practice will famil-
iarize them with the controls of the machine.
1. Clear the area of bystanders, especially small
children, before starting.
2. Review and follow the Pre-Operation Checklist
(see Section 4.4).
3. Do not operate the machine in a closed building
unless there is adequate ventilation.
4. Be sure that all guards and access doors are in
place and secured before starting.
5. Do not climb into the tub or place hands in any
opening when the engine is running.
6. Be sure that the tub rotation and knife drive con-
trols are disengaged and the tub grate is in its
highest position.
7. Place a bale into the tub
(figure 8 and 9).
8. Remove the strings and dispose of them away
from the machine and working area.
9. If required, load up to 2 other bales.
10. Starting engine
a. Turn the switch to the ON position.
b. Open the fuel supply valve.
c. Move the throttle into its mid-range position.
d. Close the choke if the engine is cold or if the
unit has not been run for a while.
e. Pull sharply on the starter rope to start the
engine or turn the ignition switch to the
START position.
f.
Gradually open the choke as the engine
warms to operating temperature.
g. Open the throttle to provide maximum power
and RPM when operating.
11. Use the direction/speed lever and maneuver the
machine into position.
Attention: Use care when driving over ruts,
bumps or rough ground. Since the machine has
a 3 point stance, it can tip rather easily if travelling
too fast. Drive slow!
Do not drive the machine across a slope. Always
drive directly up or down to prevent tipping.
WARNING
Never attempt to remove strings while the
engine is running. If the strings get caught in
the knives, you could easily be pulled into the
tub before you can let go!
Fig. 9
Loading the tub
Fig. 8 Right way to
place a bale
into the tub