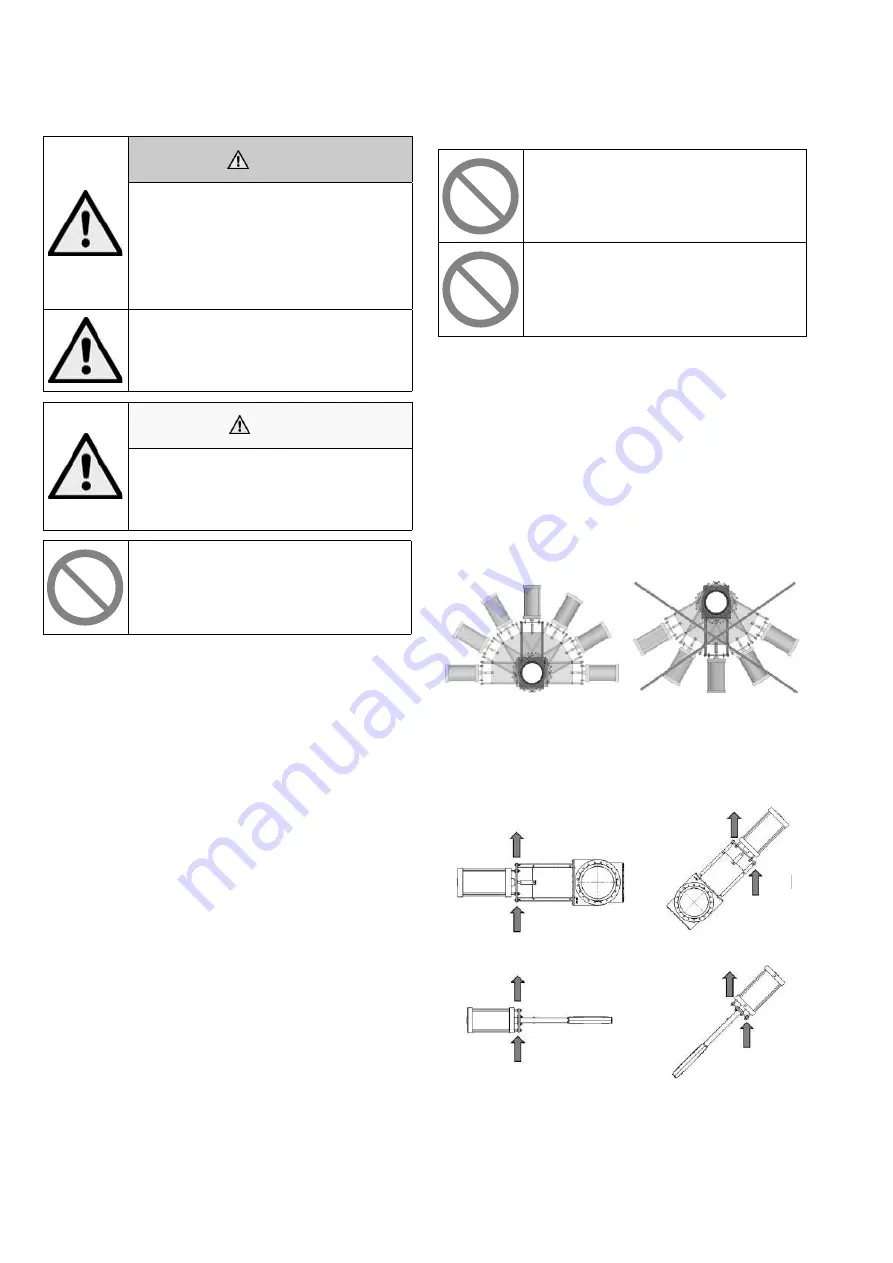
4SK70EN - 5/2023
12
4 Installation
WARNING!
Crushing and cutting hazard.
Do not put your hands or fingers into the tower or
port areas when the valve cycles.
Do not energize the actuator before the valve is
properly attached to the pipeline.
Disconnect and de-energize the actuator before
installation and maintenance work.
High pressure injection hazard.
Do not use higher pressure than rated for the valve.
Higher pressures can cause serious damage to the
valve or harm to operating personnel.
CAUTION!
Harmful substance hazard.
If the process medium has to be fully contained, is
corrosive or harmful, make sure the flushing ports
are piped to a safe location.
Never use the valve with all flushing ports
plugged. Accumulated solids can cause the valve
to jam.
4.1 General
Flowrox gate valves are normally delivered fully assembled
and ready for use. Only personnel with appropriate training
are allowed to install the valves. If the valve is delivered
without an actuator or accessories, they must be installed in
accordance with the manufacturer’s instructions.
Flowrox gate valves have connections with DIN or ANSI
bolt drillings as standard design, but other drillings are also
available, such as BS, AS, JIS.
Reserve enough space for safe installation and maintenance.
See
Appendix A
for valve dimensions. Notice that during
opening and closing cycles, a small amount of medium is
discharged in the valve body cavity; therefore do not install
gate valves above walkways or critical components. Flushing
and drainage connection must be installed if medium is
harmful or corrosive.
If the valve has been stored in the warehouse, lubricate the
valve as instructed in the
Lubrication
chapter.
4.2 Flow direction, support, and valve
position
Do not install DN250 or larger valves in other
than vertical position without support.
Do not step on a valve installed in horizontal or
angled position.
The valve does not have an intended flow direction; therefore
it can be installed either way in the pipeline.
Proper pipe support must be placed on either side of the valve
to support the weight of the pipe. The valve must never be
used to support the pipes.
The valve can be installed in any position other than below
horizontal. Flushing will not work in installations below
horizontal level and it will lead to leaking and nonfunctional
valve. See the following Figure 7.
Recommended installation
positions
Forbidden installation positions
Figure 7. Installation alternatives for SKW and SKF
valves.
Horizontal installation.
Support is required as shown or
otherwise.
Angled installation.
Support is required as shown or
otherwise.
Figure 8. Support for automatically actuated valves.
Summary of Contents for Flowrox SKW DN50-600
Page 1: ...Valmet 4SK70ZHS 6 2022...
Page 2: ...4SK70ZHS 6 2022 2...
Page 3: ...3 4SK70ZHS 6 2022...
Page 4: ...4SK70ZHS 6 2022 4...
Page 5: ...5 4SK70ZHS 6 2022...
Page 6: ...4SK70ZHS 6 2022 6 2 0 to 75 7 2 3 4...
Page 7: ...7 4SK70ZHS 6 2022 H...
Page 8: ...4SK70ZHS 6 2022 8 2 3 4 2 2 5 6 7 8 4 2 2...
Page 9: ...4SK70ZHS 6 2022 2 3 4 2 2 5 6 7 8 4 2 2...
Page 10: ...4SK70ZHS 6 2022...
Page 11: ...4SK70ZHS 6 2022 3...
Page 12: ...4SK70ZHS 6 2022 4...
Page 13: ...4SK70ZHS 6 2022...
Page 14: ...4SK70ZHS 6 2022...
Page 15: ...4SK70ZHS 6 2022 5 6...
Page 16: ...4SK70ZHS 6 2022 4 2 7 cm3 cm3...
Page 17: ...4SK70ZHS 6 2022...
Page 18: ...4SK70ZHS 6 2022...
Page 19: ...4SK70ZHS 6 2022 Nm...
Page 20: ...4SK70ZHS 6 2022 20...
Page 21: ...4SK70ZHS 6 2022...
Page 22: ...4SK70ZHS 6 2022 22 DN D F U K N S V W H H H D F U K N S V W H H H...
Page 23: ...23 4SK70ZHS 6 2022 DN D F U K N S V W H H H D F U K N S V W H H H...
Page 25: ...25 4SK70ZHS 6 2022 2 3 4 5 6 7 8 0 2 4 S2 S3 S4 S5 S6 S7 S8...
Page 26: ...4SK70ZHS 6 2022 26 F F5 H S S5 Z2 Z3 Z5 Z6...
Page 27: ...27 4SK70ZHS 6 2022 Z7...
Page 28: ...Valmet 4SK70ZHS 6 2022...