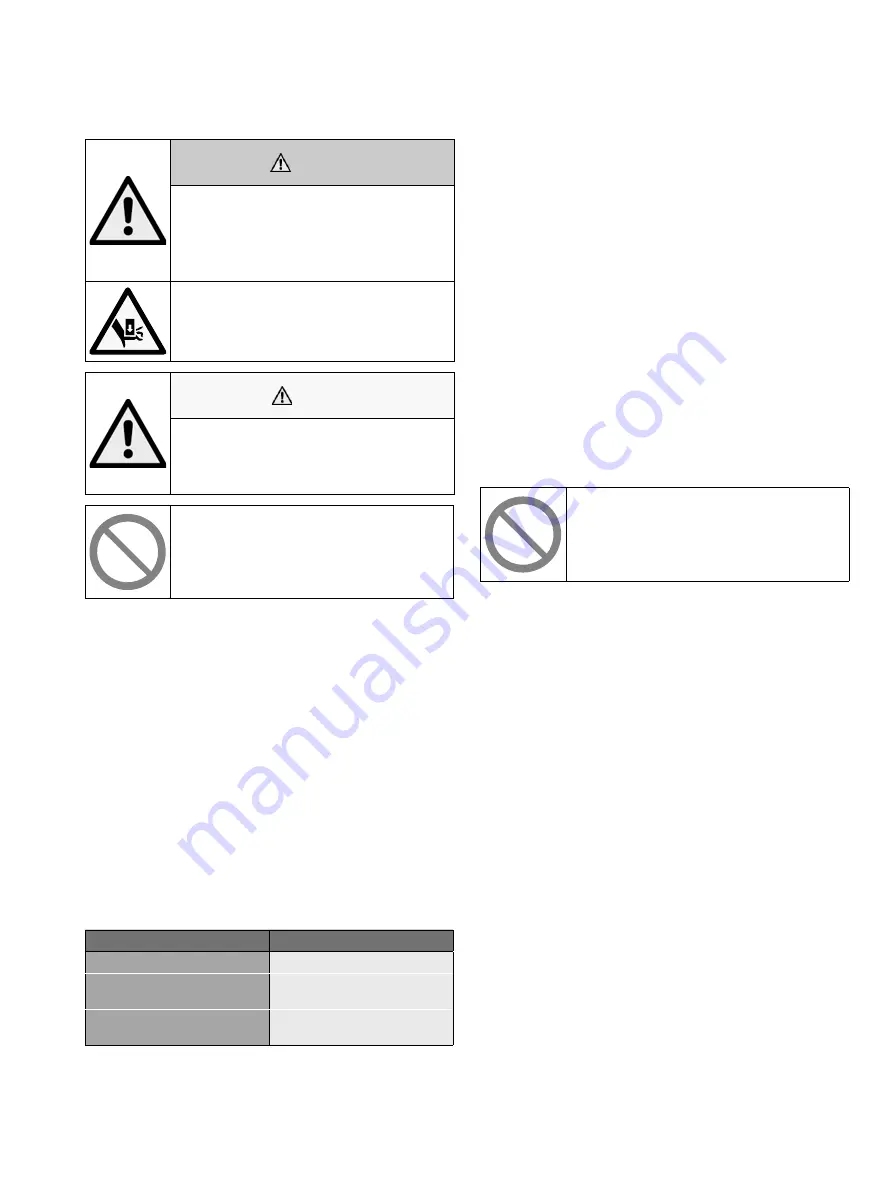
11
4PV72EN - 4/2022
6 MAINTENANCE
6.1 General maintenance and checks
WARNING!
Unexpected start-up hazard.
De-energize actuators before maintenance. Especially
pneumatic actuators equipped with a mechanical spring
can cause injury to people and equipment if cylinder
actuates unintentionally.
Crushing hazard.
Keep your hands and feet clear of moving parts.
De-energize actuators before maintenance.
CAUTION!
Depressurize, empty and cool down the valve before any
maintenance work. Valve surface can be hot. Isolate the
valve completely from the process and follow the factory
safety regulations.
Do not step on a valve installed in horizontal or angled
position.
Only personnel with appropriate training are allowed to
service the valves. For actuator service instructions consult
the manufacturer’s documentation supplied with the valve.
Check the condition of the valve regularly. When the valve is
tight and it actuates flawlessly, periodic inspection is the only
mandatory maintenance task. Do not neglect it as sleeves
wear over time depending on conditions and process
6.2 Scheduled maintenance
Include the valves in your factory maintenance program.
Maintenance tasks and service intervals are offered as a
guideline in Table 6 Schedules will vary with applications.
Table 6.
Maintenance schedule.
Maintenance task
Frequency & advice
Do a leakage inspection
Regularly. Refer to Troubleshooting.
Run an open/close cycle
Suggested once a month for smooth
and reliable operation.
Examine the valve for erosion and
wear
Every six months.
6.3 Spare parts
To ensure correct and quick delivery of spare parts, the order
must contain at least the following information:
• Valve type
• Serial number
• Spare part name and quantity (example: Sleeve, 1 piece)
You can order the spare parts from Neles offices, distributors
or agents. Contact information is available at http://www.
flowrox.com
It is recommended to keep one sleeve as a spare part at your
factory warehouse. For part numbers refer to Mechanical
structure.
6.4 PVEG disassembly and sleeve
replacement
Do not disconnect a pressurized valve from the pipeline
in any case!
1. Open the valve and detach it from the pipeline.
The body bolts of the PVEG valve are stainless steel and
can be removed by a 10 mm hexagon key and 19mm socket
wrench for 2” and 3” valves, and a 14 mm hexagon key and
24mm socket wrench for 4” and 6” valves.
2. If other body half cannot be removed from PVEG A
valve, remove lower nuts (part 8.) and close the valve
carefully by pneumatic cylinder so that cylinder (part 3.)
raises up from the attachment frame (part 5.). Do not
change the position of upper nuts (part 8.).
3. Remove the body bolts (part 11/12 or 9/10) and other
body half.
4. Remove the broken sleeve (part 7.) and put in the new
sleeve.
5. Install body half and body bolts.
6. If lower nuts (part 8.) had to be removed from PVEG
A valve, open the valve by pneumatic cylinder so that
cylinder (part 3.) lands down and it is possible to install
removed lower nuts (part 8.). Check that the valve will
close totally.
7. Install the valve into the pipeline.