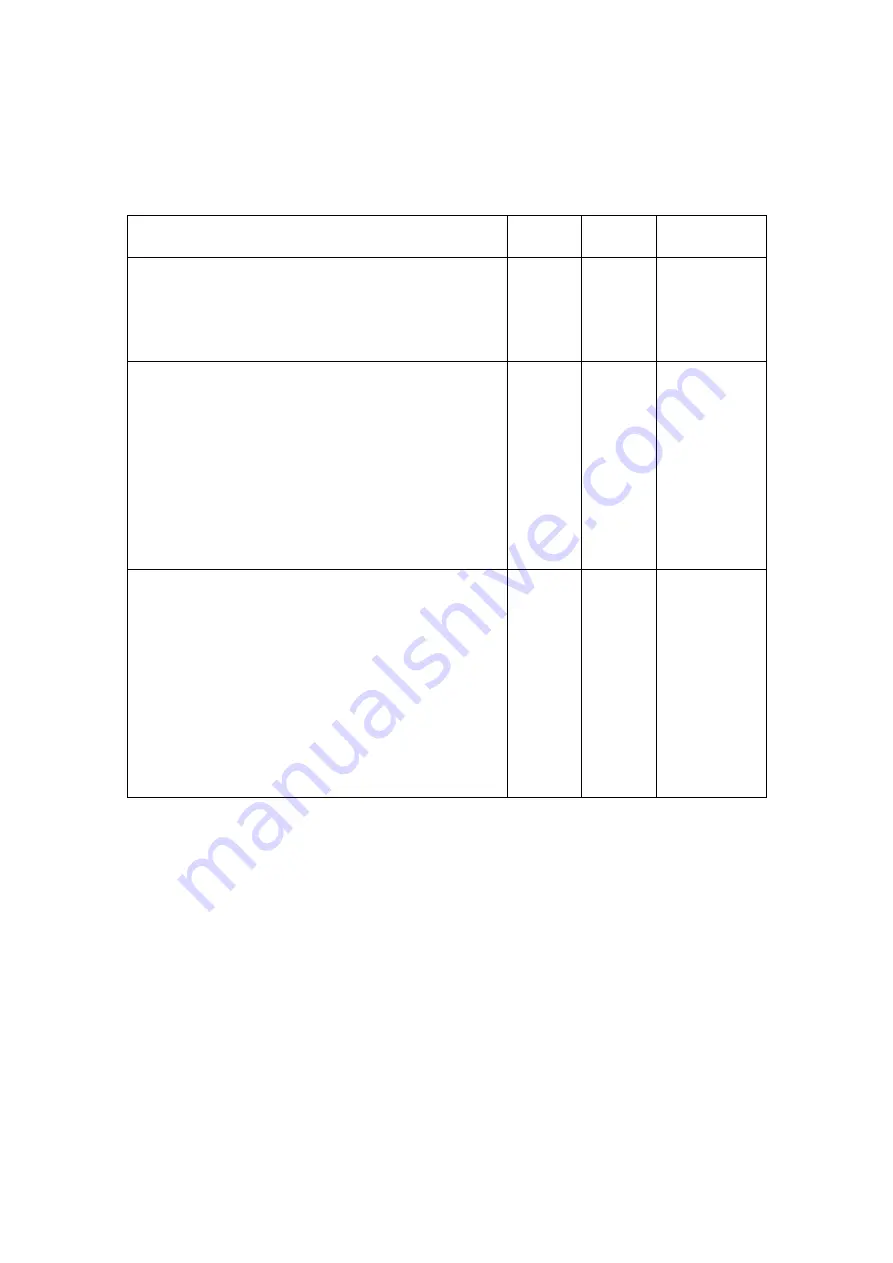
3.1.3
Motor Parameters
Configuration items in this menu relate to the motor and turntable.
Parameter / Description
Units
Range
Default
value
Winding 1 phase is always starts at 0 degrees.
This is a statement. Subsequent windings
probably require 90, 180, 270 degree phase angles
respectively depending if you are using 2,3,4
phase motors.
-
-
-
Enter winding %d, phase angle in deg
Windings probably require 90, 180, 270-degree
phase angles respectively depending if you are
using 2,3,4 phase motors.
Slight adjustment of phase angles can reduce
motor vibration. Start with the defaults and adjust
on test. If you can hold the motor in your hand
this is the best way to determine vibration.
Listening to the motor noise is also a good
indication.
degrees 45 –
300
90, 180, 270
for each
phase 2, 3, 4
respectively
Enter winding n, drive voltage (rms)
The voltage that should be applied to each
winding. For 110v synchronous motors 85v rms is
a good starting point. Slight adjustment of phase
voltages can reduce motor vibration. Start with
the defaults and adjust on test. If you can hold the
motor in your hand this is the best way to
determine vibration. Listening to the motor noise
is also a good indication. However, if you set to
low a voltage then the platter will fail to turn or
not make it up to 45 rpm.
Volts
(rms)
5-100
85
3.1.4
PID Control parameters
Proportional, Integral, Derivative control is an adaptive speed control algorithm. It
uses the IR platter rotation sensor to adjust the frequency fed to the motor to help
maintain an accurate 33.3 or 45 rpm rotation speed. Further details on setting the
values are provided in a separate section. We recommend initial testing is done only
with motor drive and IR sensor to get the system initially working. Once you get an
rpm indication in the region of 33 or 45 rpm from the IR sensor, only then proceed to
configure PID. To get to the parameters in this setup section you must answer Y to
“Are you using PID and platter sensor?” in the system parameters section.