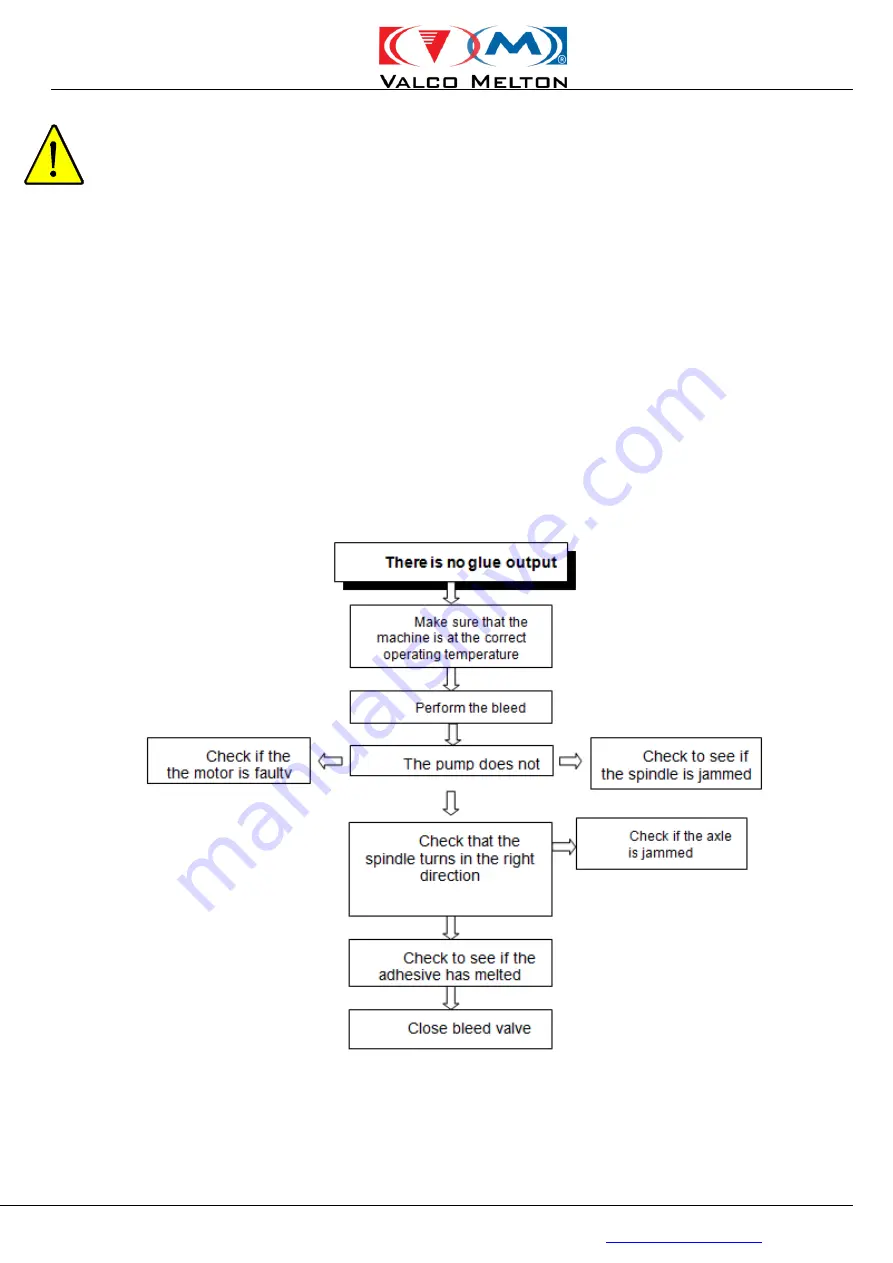
MUS0920201
07/10/2014 66
MELTON, S.L.U. - POLIGONO INDUSTRIAL AGUSTINOS CALLE G-34,31160 ORCOYEN, NAVARRA
TEL: 00 34 948 321580 Fax: 00 34 948 326584 e-mail: [email protected]
WARNING:
The maintenance operations described in this chapter should only be
performed by qualified personnel understanding the processes and familiar with the
safety measures involved.
7.1. INTRODUCTION:
This chapter refers to the most common faults in your equipment.
Breakdowns occur when the flow of glue is reduced or stops, or the alert system
informs of a fault. Try to solve the problem with the help of this manual.
If the problem cannot be solved with the information provided here, contact your
Melton representative.
7.2. MECHANICAL FAULTS: