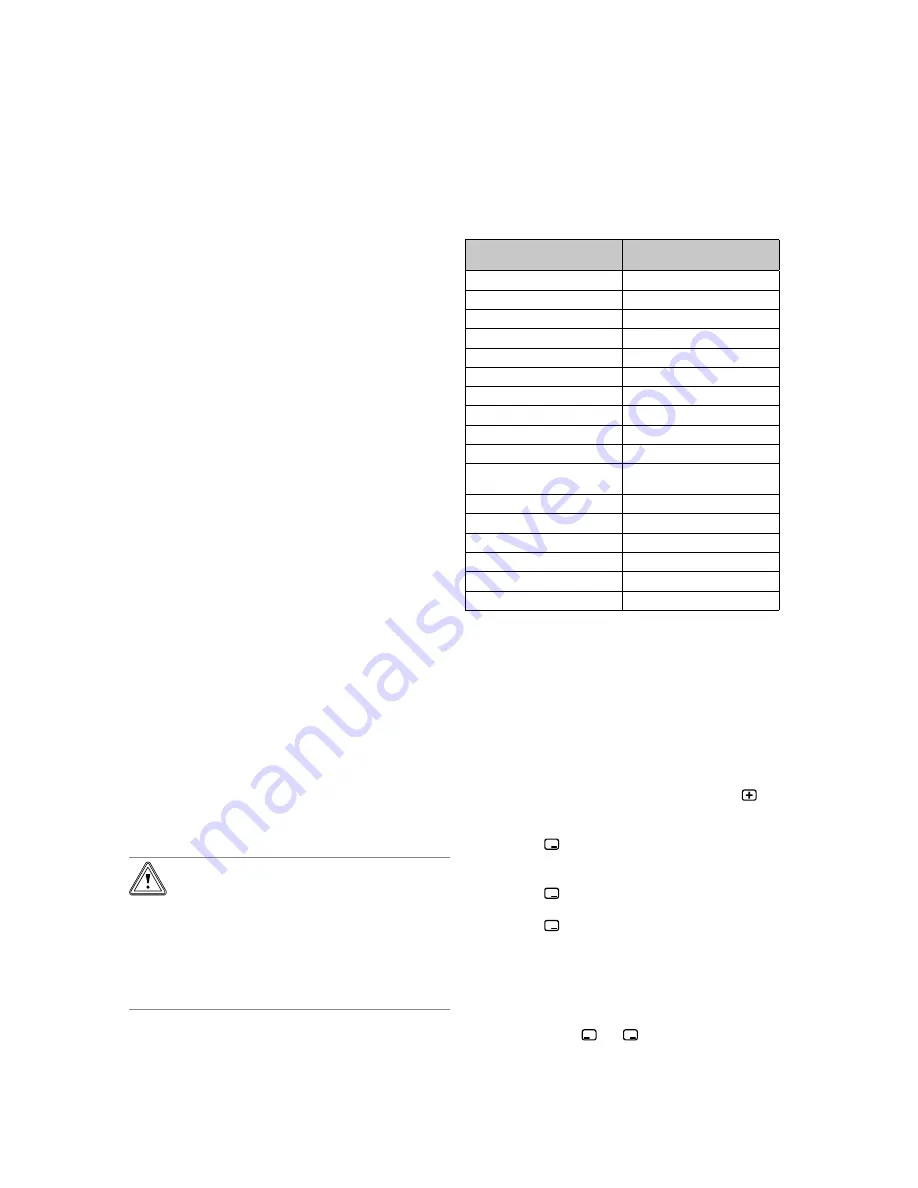
Start-up 7
0020257319_02 Hydraulic station Installation and maintenance instructions
33
6.14
Connecting the domestic hot water cylinder
1.
Connect the temperature sensor (VR10) for the do-
mestic hot water cylinder to the corresponding connec-
tion for cable harness X22 on the control PCB.
2.
If an external current anode is installed in the domestic
hot water cylinder, connect it to X313 or X314 on the
power supply PCB.
◁
The connection plug is included in the bag of small
parts.
6.15
Connecting the external prioritising diverter
valve (optional)
▶
Connect the external prioritising diverter valve to X14 on
the control PCB.
–
The connection to a permanently live phase "L" with
230 V and to a switched phase "S" is available.
Phase "S" is actuated by an internal relay and
releases 230 V.
6.16
Using the additional relays
▶
If required, consult the installation diagram handbook
that is contained in the scope of delivery for the system
control and the handbook for the optional module.
6.17
Connecting cascades
▶
If you want to use cascades (max. seven units), you must
connect the eBUS line to contact X100 via the
VR32b
bus coupler (accessory).
6.18
Sealing the power supply PCB
1.
Tighten all of the screws on the strain relief clamps.
2.
Close the cover for the electronics box on the power
supply PCB.
3.
Hinge the electronics box back up.
6.19
Checking the electrical installation
▶
After the installation is complete, check the electrical in-
stallation to ensure that the connections that have been
established are secured properly and are sufficiently in-
sulated.
7
Start-up
7.1
Activating screed drying without the outdoor
unit and system control
Caution.
Risk of damage to the product caused by
impermissible purging
Without purging the heating circuit, the sys-
tem may become damaged.
▶
If the screed drying is activated without a
system control, purge the system manu-
ally. No automatic purging takes place.
Screed drying
.
–
You can use this function to "dry heat" freshly laid screed
in accordance with the construction regulations, accord-
ing to a defined time and temperature schedule, without
having a system control or the outdoor unit connected.
When screed drying is activated, all the selected operating
modes are interrupted. The function controls the flow tem-
perature of the controlled heating circuit according to a pre-
set programme, regardless of the outdoor temperature.
The display shows the target flow temperature. You can
manually set the current day.
Days after starting the func-
tion
Target flow temperature for
this day [°C]
1
25
2
30
3
35
4
40
5
45
6
–
12
45
13
40
14
35
15
30
16
25
17
–
23
10 (frost protection function,
pump in operation)
24
30
25
35
26
40
27
45
28
35
29
25
The day is always changed at 00:00, irrespective of when
the function starts.
After a mains Off/On, screed drying starts with the last active
day.
The function ends automatically when the last day of the
temperature profile has elapsed (day = 29) or if you set the
start day to 0 (day = 0).
7.1.1
Activating the screed drying
1.
Press the reset button.
2.
When restarting the display, press and hold the
but-
ton until the language selection opens.
3.
Set the required language. (
→
Page 36)
4.
Press the
button in order to select the power supply
for the back-up boiler.
–
230 V
5.
Press the
button in order to select the output of the
back-up boiler.
6.
Press the
button in order to select the start day for
the screed drying.
◁
The screed drying is started and the display shows
the current flow temperature and the right-hand
status bar shows the system pressure.
▽
In the current programme, the current status mes-
sages for the system can be called up in the display.
▶
Press the
and
buttons in order to display
the status messages.