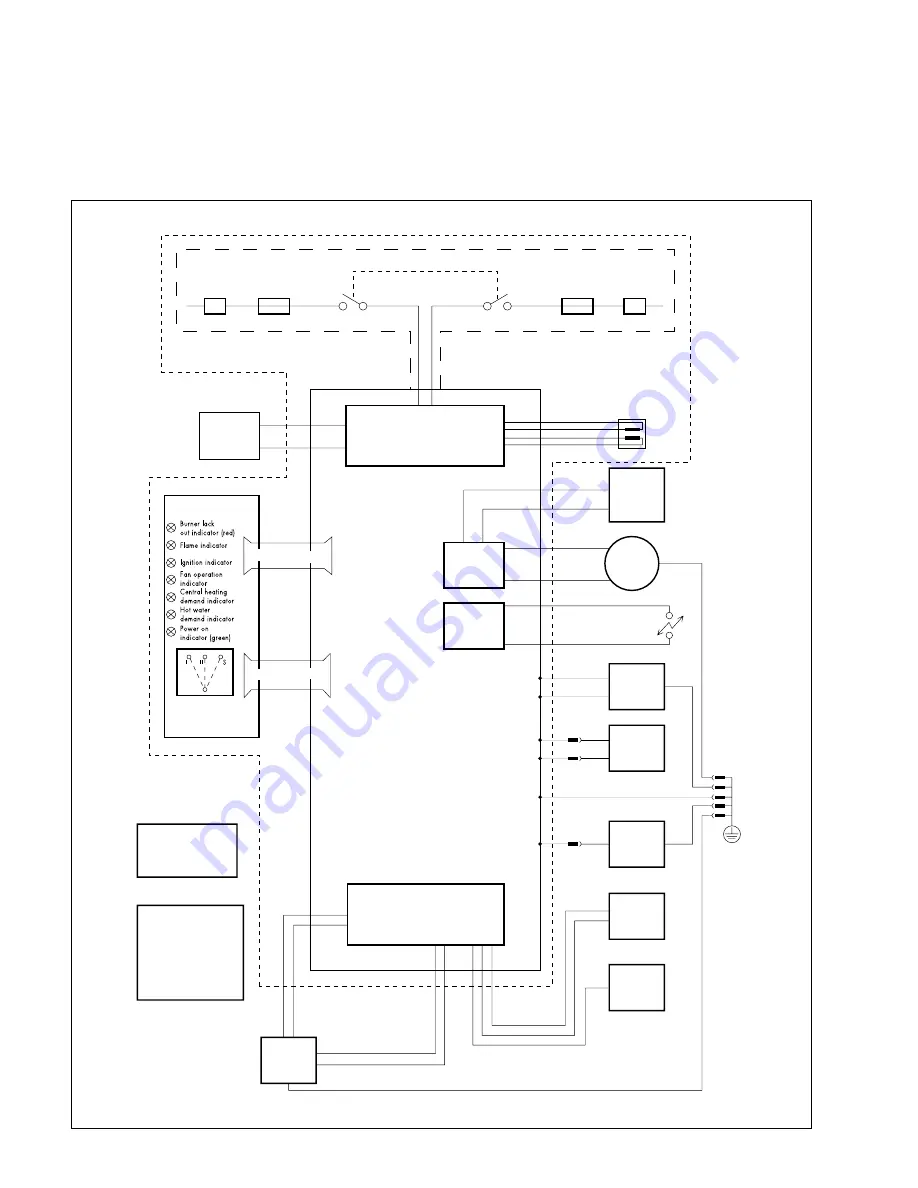
54
9 Electrical diagrams
9.1 Functional Flow diagram: VUW 242/1 E, 282/1 E
GW 651/1
MAIN SWITCH
CONTROL BOX
MAIN SWITCHBOARD
MAIN
TRANSFORMER
230V
20V
POWER SUPPLY
CONTROL BOARD
WATER-PUMP
SELECTOR
OVERHEAT
THERMOSTAT
FAN-
CONTROL
AIR
PRESSURE
SWITCH
FAN
PUMP
DHW
MICRO
SWITCH
FLAME
SENSOR
GAS
VALVE
GAS BURNER CONTROL
LEGEND
NOTE
ALL UNCODED
WIRES ARE BLACK
b
blue
br
brown
r
red
t
transparent
t
r
r
NTC
TEMPERATURE
SENSOR
PRESSSURE
DIFFERENTIAL
SWITCH
IGNITION ELECTRODES
b
br
IGNITION
TRANSFORMER
L
2
1
F2A
F2A
N
plug in connector
plug in connector
fig. 78