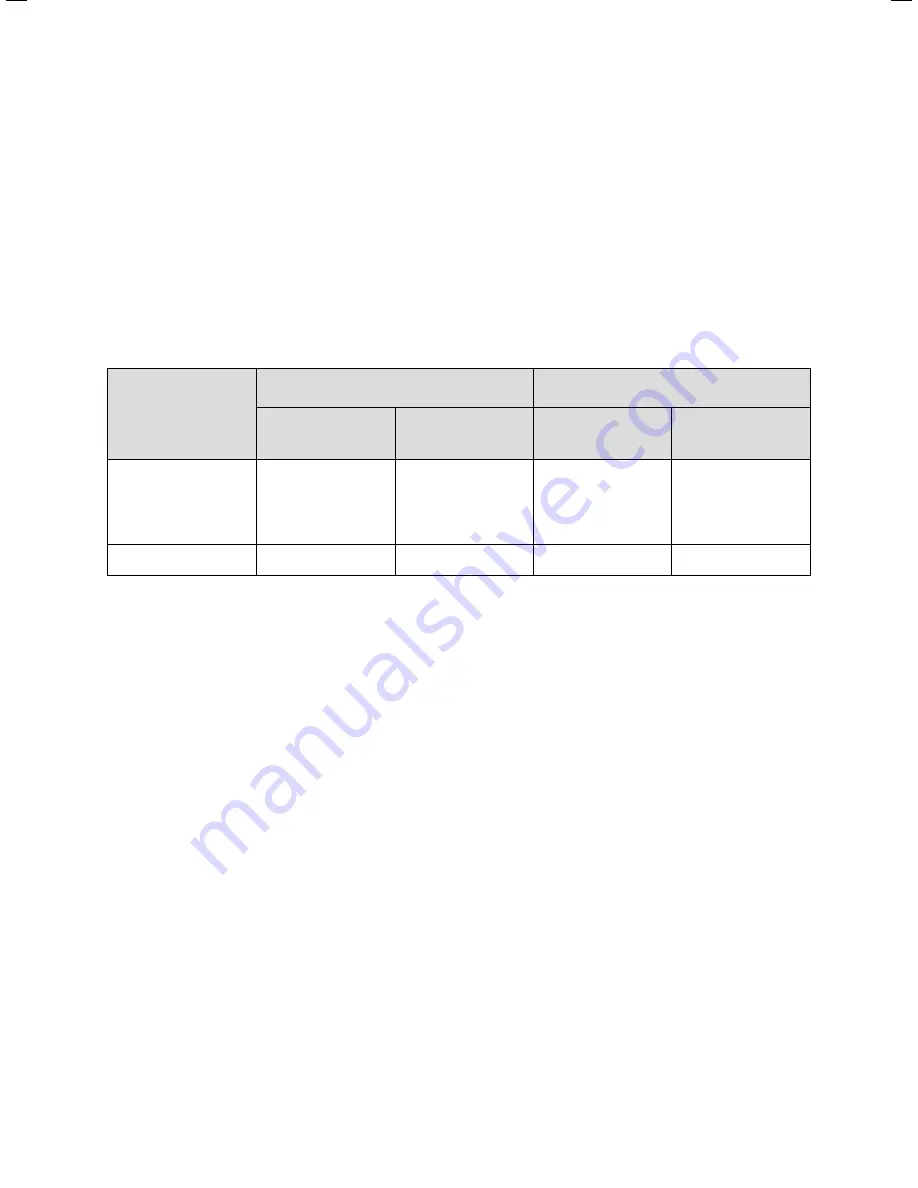
37
Instructions for installation and servicing ecoTEC 839592_12
• Connect a digital pressure gauge or U-tube
manometer (
2
).
• Open the gas isolation valve of the boiler.
• Start the boiler by activating the test program P.1 as
described in section 8.2.
• In addition, ensure that maximum heat can be
dissipated into the heating system by turning up the
room thermostat.
• Alternatively, for ecoTEC combination boilers fully
open the hot water taps to ensure full flow rate
through the boiler.
• With the boiler operating at full load check that the
gas inlet working pressure at the reference test
point (
1
) complies with the requirements of Table 5.2.
ecoTEC appliance
Natural gas (G20)
LPG (G31)
Minimum pressure at
reference test point in
mbar
Maximum pressure at
reference test point in
mbar
Minimum pressure at
reference test point in
mbar
Maximum pressure at
reference test point in
mbar
ecoTEC plus
612/615/618/624/630
824/831
ecoTEC pro
24/28
16
23
23
43
ecoTEC plus
637/837
15
23
23
43
Table 5.2 Gas inlet working pressures at the reference test
point
• Should the pressure recorded at the reference test
point in the boiler be lower than indicated (Table 5.2)
check if there is any blockage in the pipework or if the
pipework is undersized.
• If the supply pressure is out of tolerance contact your
Emergency Service Provider.
If the gas inlet working pressure at the reference test
point (
1
) is
not
within the permissible range and you
cannot correct the failure, notify the gas supply
company or the Vaillant Service Solutions team and
proceed as follows:
• Take the boiler out of operation by
- Pressing the + and i buttons simultaneously and
turn down both thermostat control knobs.
- Only for combination boilers: Allow the boiler to cool
down by turning off water taps and allow pump
overrun to operate for a minimum of two minutes.
• Close the gas isolation valve of the boiler.
• Remove the pressure gauge and re-tighten the sealing
screw (
1
).
• Turn on gas at the gas isolation valve.
• Make sure that there is no leakage at the sealing
screw.
• Turn off gas at the gas isolation valve.
• Put the front casing back on.
• Turn off electrical supply to the boiler.
• You must not start up the boiler.
If the gas inlet working pressure is within the
permissible range, proceed as follows:
• Take the boiler out of operation by
- Pressing the + and i buttons simultaneously and
turn down both thermostat control knobs.
- Only for combination boilers: Allow the boiler to cool
down by turning off water taps and allow pump
overrun to operate for a minimum of two minutes.
• Close gas isolation valve of the boiler.
• Remove the pressure gauge and re-tighten the sealing
screw (
1
).
• Open the gas isolation valve of the boiler.
• Make sure that there is no leakage at the sealing
screw.
• Put the front casing back on.
• Reset boiler controls for normal operation.
• Record the appliance gas inlet working pressure
(mbar) in the Benchmark gas boiler commissioning
checklist.
Commissioning Part I 5