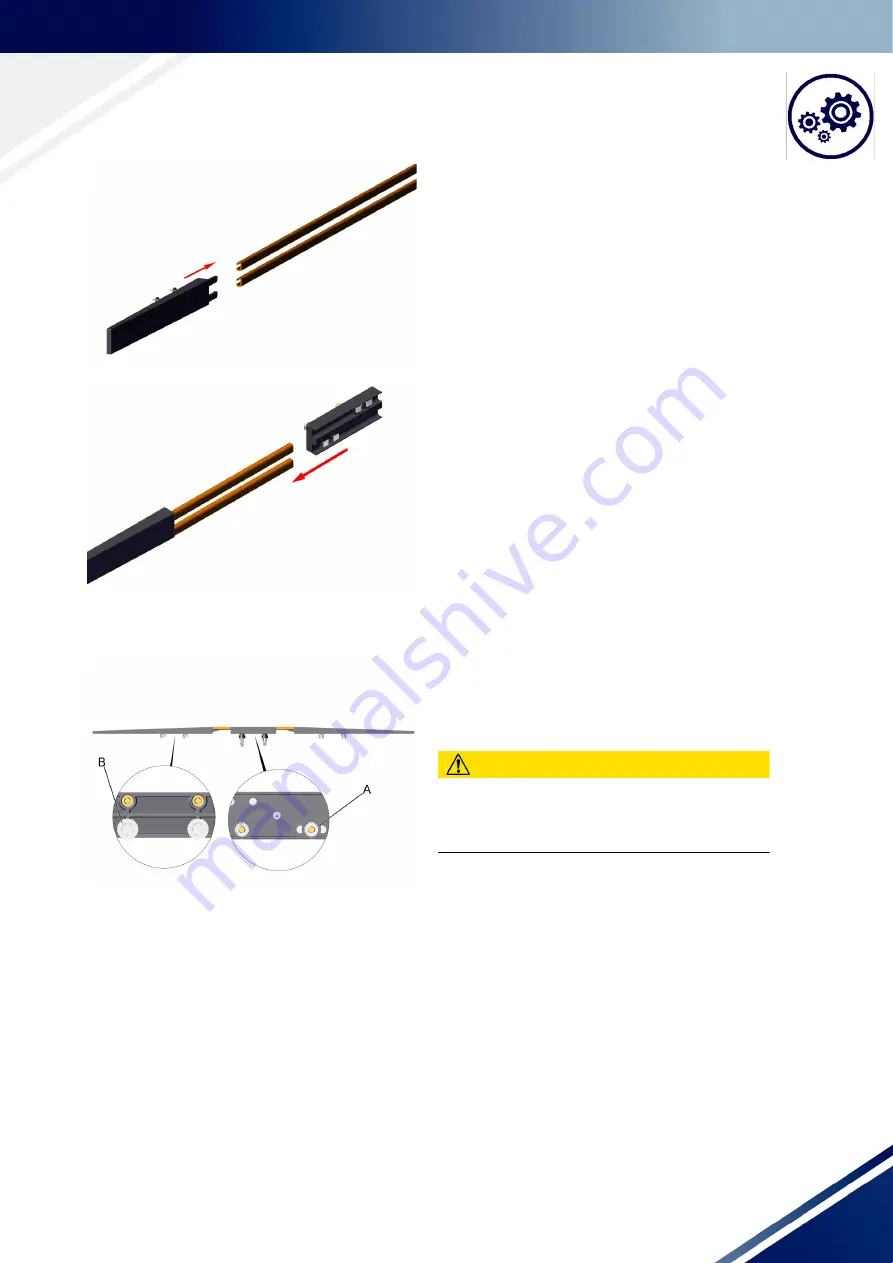
COMMISSIONING
21
5.2.2
Preassembling the system
Attaching access ramp
Assembly steps:
1. Put a ramp on the beginning of the charging con-
tact.
Push feed onto contact rails
Assembly steps:
1. Slide the rails to the desired position.
2. Tighten the screws on the back of the feeder. The
customer connection must be made to the MS
threaded bolt, see also 5.2.6 Connection Feed
terminal.
5.2.3
Assembling the system
Prerequisites:
The hole pattern is prepared according to side
19.
Installation steps:
CAUTION!
Inserting the centering bushings.
►
Only plastic sockets may be used in the area of
the feed. Metal bushings (B) must not be used.
1. Insert the centering bushing into the respective
drill hole.
a) Feed terminal: Plastic bushings
b) Access ramp: Metal bushings
2. For hole spacing
≥
500 mm,clip in the additional
suspensions.
3. Position the component according to the pre-
pared setup.
4. Fasten the component with the enclosed screws
with a tightening torque of 2 Nm.