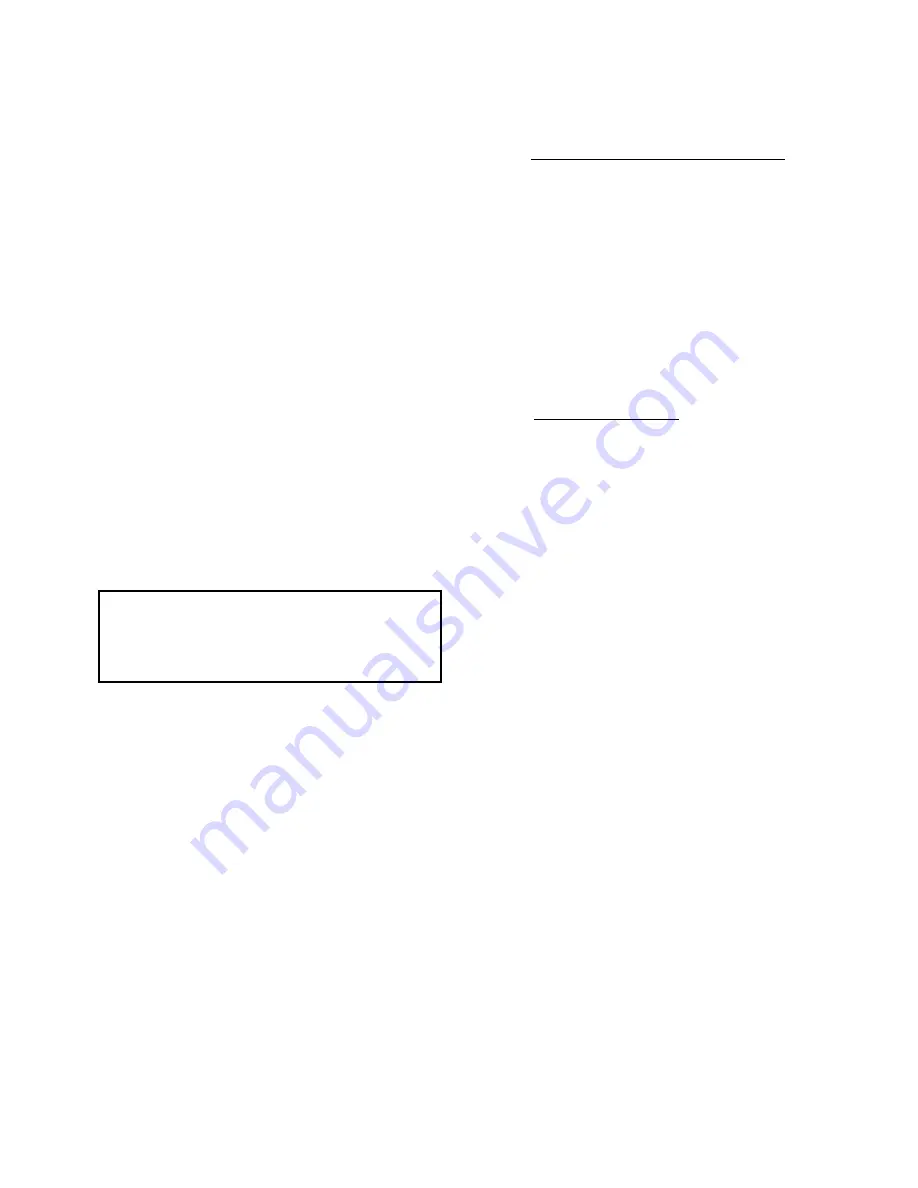
Lower heavy valves over the mating flange
using slings or chains around the valve body.
Lubricate the bolts or studs and insert around
flange. Lightly tighten bolts until gaps are
eliminated. Torque bolts in an alternating
pattern in graduated steps. If leakage occurs
wait 24 hours and re-torque the bolts but do not
compress the gasket more than 50% or exceed
bolt maximum torque rating.
VALVE CONSTRUCTION
The standard Figure 920 Air Release Valve has
a cast iron body, stainless steel float and linkage
mechanism and a rubber seat. Optional
materials such as ductile iron body can be
provided for higher working pressures. Refer to
the List of Materials submitted for the order if
non-standard materials were provided.
Refer to Page 4 for details of construction and
parts location.
The body (1) has an inlet connection at the
bottom where the valve attaches to the system
and a smaller outlet connection at the top
through which air leaves the valve.
WARNING
Removing the valve from the line or
disassembling the valve while there is pressure
in the valve body may result in injury or damage
to the valve
PREVENTIVE MAINTENANCE
Figure 920 Air Release Valves require no
scheduled lubrication, adjustment or preventive
maintenance.
A periodic visual inspection should be performed
to ensure the outlet piping is not obstructed and
to verify there is no fluid leakage.
TESTING
Valve operation can be easily tested. Close the
inlet isolation valve and remove or loosen the
pipe plug nearest the inlet to drain the water
from the valve. The float should drop as the
water leaves the valve. NOTE: A ball or gate
valve can be installed in place of the pipe plug to
facilitate testing.
Replace or tighten the pipe plug and slowly open
the inlet isolating valve. The valve should float
closed and seat tightly.
TROUBLESHOOTING
•
Valve Does Not Close / Fluid Leakage
Verify debris has not collected on the seat
preventing tight closure
Verify rubber orifice button and/or orifice
seating surfaces are not damaged
Verify float has buoyancy
Verify linkage mechanism operates freely
without binding or sticking
Verify the pressure at the valve inlet is at
least 10 PSI
•
Valve Does Not Open
Verify debris in the valve is not
preventing the float from freely falling
when fluid is drained from valve
Verify linkage mechanism operates freely
without binding or sticking
Verify the pressure at the valve inlet does
not exceed the maximum
working
pressure
DISASSEMBLY
While small valves may be more easily serviced
by removing it from the line, all valves can be
serviced while the body remains connected to
the pipeline. A skilled technician with proper
tools should perform all work. No special tools
are required.
First ensure there is no pressure within the
valve. Remove the cover bolts and nuts (16 &
17) and lift off cover (2) with float and linkage
attached. It may be necessary to pry the cover
off. Be careful no to damage or lose O-ring (21).
Remove the two spring pins connecting the lever
arm (5) and float arm (6) to the bracket (3). The
float and linkage will be free from the cover.
Remove the spring pin connecting the pivot link
(12) to the float arm (6) and remove the float
screw (13) and lockwasher (9). Remove the hex
nut (8) and lockwasher (9) and unscrew the
orifice button (7) from the lever arm (5).
Remove the bracket screw (4) to remove the
leverage bracket (3). Using a hex socket
remove the orifice (20) from the cover.