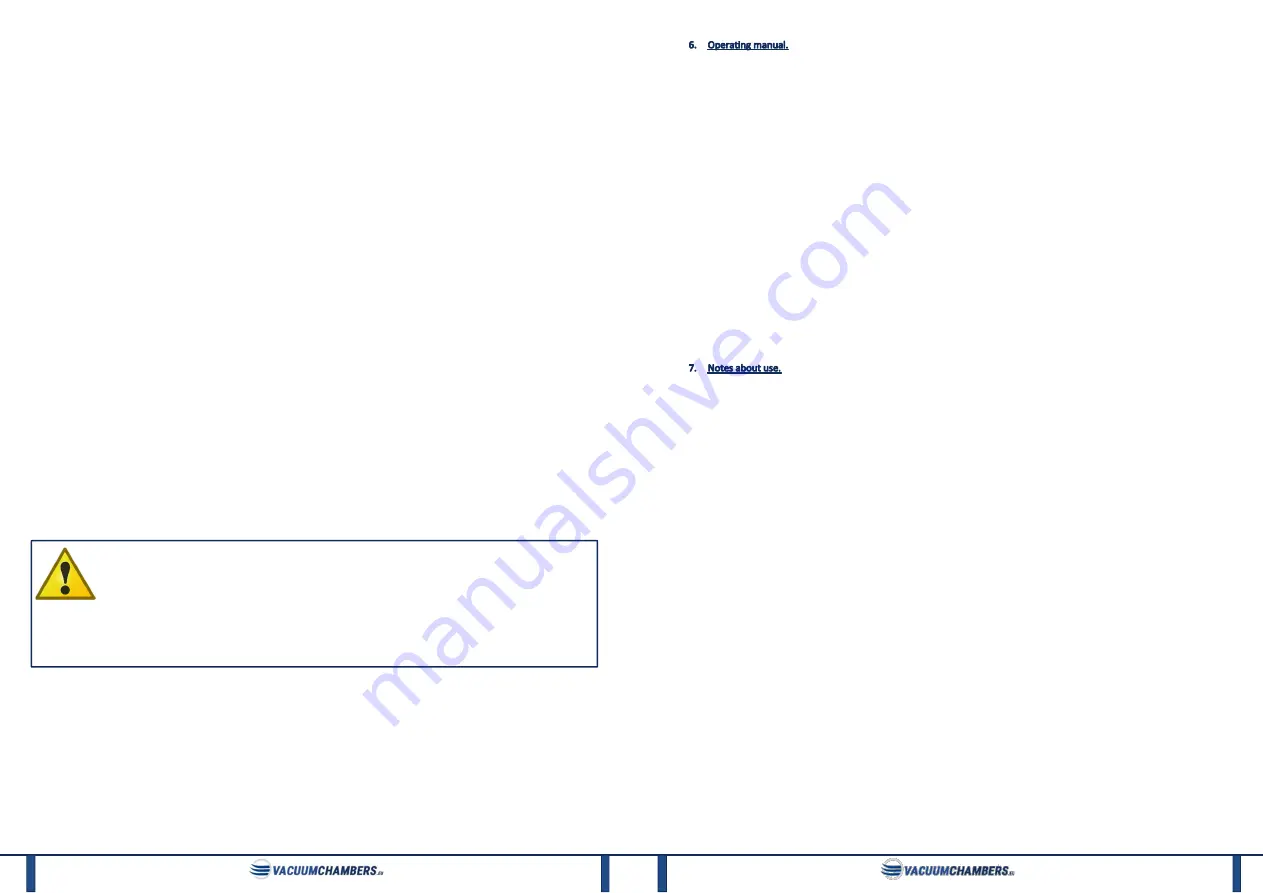
13
4)
Open the inner tank by removing the inner tank lid.
5)
Fill the inner chamber with cooling agent (e.g. dry ice):
a. Read cooling agent safety instructions and follow the information contained therein.
b. Put on cold resistant gloves.
c. Put the cooling agent into the cold trap inner tank.
d. Close the inner tank with the lid (without pressing lid down).
6)
Open the pump connecting valve and chamber connecting valve (place the valves handles parallel to the valves).
7)
Close the unsealing valve (place the valve handle perpendicular to the valve).
8)
Start degassing the chamber according to the point 6. “Operating manual.” of this manual.
9)
Control amount of material accumulating in the cold trap.
10)
If large amount of material has accumulated inside the cold trap:
a.
Close the cold trap valves: vacuum pump connecting valve and vacuum chamber connecting valve (place the valves
handles perpendicular to the valves).
b.
Turn off the vacuum pump.
c.
Open the unsealing valve (place the valve handle parallel to the valve). Allow the pressure inside the cold trap to
equilibrate with the ambient pressure.
d.
Take out the inner tank using cold resistant gloves.
e.
Remove any excess deposition material.
ATTENTION! The deposition material should be removed very carefully due to its very low temperature.
f.
Place cleaned inner tank back into the outer tank.
g.
Close the unsealing valve.
h.
Open the vacuum pump connecting valve (place the valve handle parallel to the valve).
i.
Start the vacuum pump. Lower the pressure inside the cold trap.
j.
Open the vacuum chamber connecting valve (place the valve handle parallel to the valve).
k.
Continue the degassing process.
l.
Clean the vacuum cold trap again if necessary (go back to point 10) a.).
11)
When the degassing process is complete, close the vacuum chamber connecting valve and the vacuum pump connecting
valve (place the valves handles perpendicular to the valves).
12)
Disconnect the vacuum pump and the vacuum chamber from the cold trap if needed.
13)
Open the unsealing valve (place the valve handle parallel to the valve). Allow the pressure in the cold trap to equilibrate
with the ambient pressure.
14)
Handle the remaining cooling agent in accordance with its safety instructions.
15)
Clean the cold trap.
Be very careful when operating the cold trap. This applies especially to the cleaning of the cold trap from
cold deposition material.
The vacuum cold trap is very cold when cooling agent is put inside. Risk of frostbite in case of direct
contact with cold trap elements.
Use cold resistant gloves.
Do not touch the device if not necessary.
Always follow all cooling agent instructions and warnings.
The inner tank lid must not be pressed down, loaded with other objects nor have limited free lift.
Large amount of accumulated deposition material can block the air flow from the vacuum chamber to the vacuum pump. If
that happens, clean the vacuum cold trap according to the point 10) of instruction above.
Accumulated material, when reaches the ambient temperature and pressure, most often turns into liquid (e.g. water,
ethanol). Then cleaning the cold trap is easier. Be very careful when cleaning cold trap before material turn into liquid. The
material is then very cold and there is a high risk of frostbite.
14
1)
Place degassing material in the additional container into the chamber.
2)
Place the lid on the chamber. Make sure it’s placed centrally on the tank.
In the case of a metal lid with clamps (chamber with a stirrer mechanism), place the lid on the tank in accordance with
paragraph "4C. Stirrer mechanism.” of this manual.
3)
Switch the intake air valve to the OFF position (valve handle perpendicular to the valve).
4)
Switch the exhaust air valve to the ON position (valve handle parallel to the valve).
5)
Turn on the vacuum pump.
6)
In the first phase of the suction it may be necessary to press the lid to the tank until the increasing vacuum in the chamber is
noticed.
7)
At the time of degassing casting products significantly increase their volume, note that opening the intake air valve prevents
leakage of these products when too small container is used. The operator should control the process and react
appropriately to increase in products volume, so that they do not get into the lid of the chamber and contaminate the
connections there.
8)
Degassing should continue until the degassing material stops increasing its volume and rapidly drops and reduces its
volume. The material will have a homogeneous, clear appearance.
9)
Before turning off the pump, close the exhaust air valve.
10)
Turn off the vacuum pump.
11)
Slowly open the intake air valve to balance pressure inside a chamber. After this step, lid can be removed.
12)
The process above can be repeated for the filled forms in order to obtain the best results.
Proper work of the vacuum chamber can only be guaranteed by using a vacuum pump which allows to achieve a vacuum of
at least 0.1mbar (10Pa). It is recommended to use vacuum pumps tested and recommended by VacuumChambers.eu.
Before starting work, make sure that the oil level in the pump is suitable. The pump can’t work without oil (possible seizing
of the pump) or with its excessive amount (possible oil splashing at the pump outlet).
In case of using the vacuum pumps without the protection against oil return (such as one-way solenoid valve or mechanical
valve), disconnect the pump from the chamber after reaching the required vacuum. Remember to close the exhaust air
valve first. All VacuumChambers.eu pumps are equipped with one-way valve.
When operating vacuum pumps that do not come from the VacuumChambers.eu offer, please refer to the operating
instructions supplied with the pump by the manufacturer.
Casting products placed in the chamber should be placed in an additional container that is large enough to avoid the spillage
inside of the chamber.
The vacuum gauge with removed green stopper plug shouldn’t be rotated downwards as it can cause glycerine leaking.
The chamber lid should only be taken off after the pressure in the chamber is balanced. In the case of a very strong lid
suction, waggle the lid from side to side, while the other hand gently hold the gasket. Raising the lid quickly can cause
ripping off the gasket. Especially in the case of new silicone gaskets there may be an occurrence of its strong adherence to
the lid. It is recommended to protect new gasket surface with, for example by technical talc.
Chambers with polycarbonate lid are not designed for wood stabilization or to work with alcohol, ethanol, acetone and
monomers or polymers based on acrylic. For these purposes, we recommend using chambers with tempered glass lid.
If you use a vacuum chamber for degassing the aggressive resins, additional filter should be placed between the chamber
and the pump, in case if degassing exceeds more than 10 minutes. Not using a filter can lead to the pump damage, which is
not subject to warranty later.
The vacuum pump must always be set below the vacuum tank.
The time of continuous operation of the vacuum pump shouldn’t exceed 15 minutes with the connected load in the form of
a tank or installation.
Time of continuous operation of the vacuum pump must not exceed 30 minutes in conditions of free air circulation, without
connected load.
Do not allow the vacuum pump to overheat. Exceeding the temperature of 75°C on the motor housing significantly shortens
the life of the pump, and in some cases can lead to its complete damage.
RS series of rotary, oil sealed vacuum pumps are not designed for continuous operation. The recommended mode of use is
intermittent work S3 25%.
Summary of Contents for VC0918SS
Page 9: ...17...