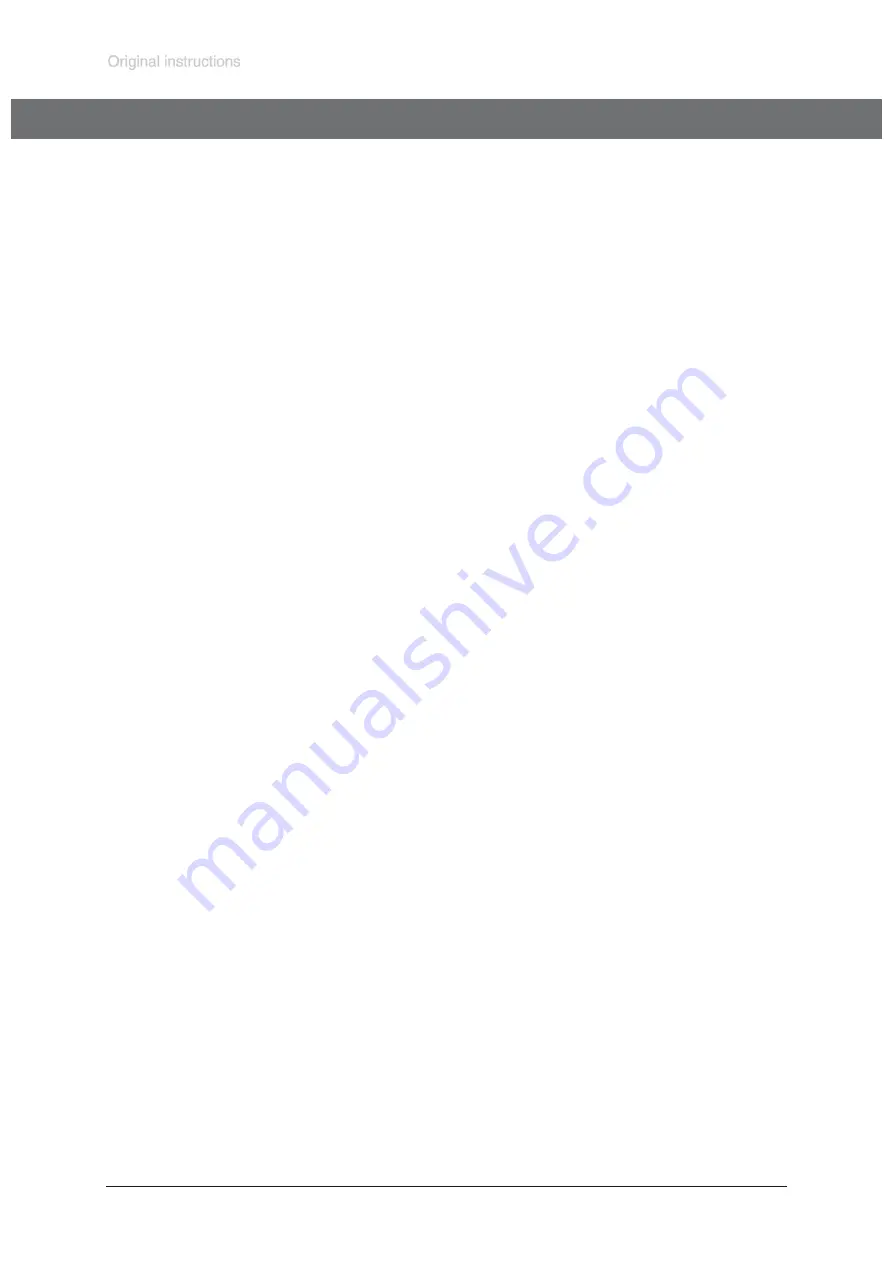
page 16 of 27
Documents are only to be used and distributed completely and unchanged. It is strictly the users´ responsibility to check carefully
the validity of this document with respect to his product. Manual-no.: 999198 / 29/09/2009
Kits
Kit AK + CVC 3000
.......................................................................................................................
699921
Kit EK 500
.....................................................................................................................................
699922
Accessories for vacuum controller CVC 3000
External pressure transducer VSK 3000
,
capacitive, ceramic diaphragm sensor 1080-0.1 mbar ..................................................................
636657
Coolant valve VKW-B, 24 V=
...................................................................................................
674220
Air admittance valve VBM-B / KF 16 / hose nozzle 6/10 mm, 24 V=
.......................................
674217
Y-type adapter VACUU•BUS
......................................................................................................
636656
Extension cable VACUU•BUS, 2m
.............................................................................................
612552
Cable RS 232C, 9-pole, Sub-D
...................................................................................................
637837
Accessories