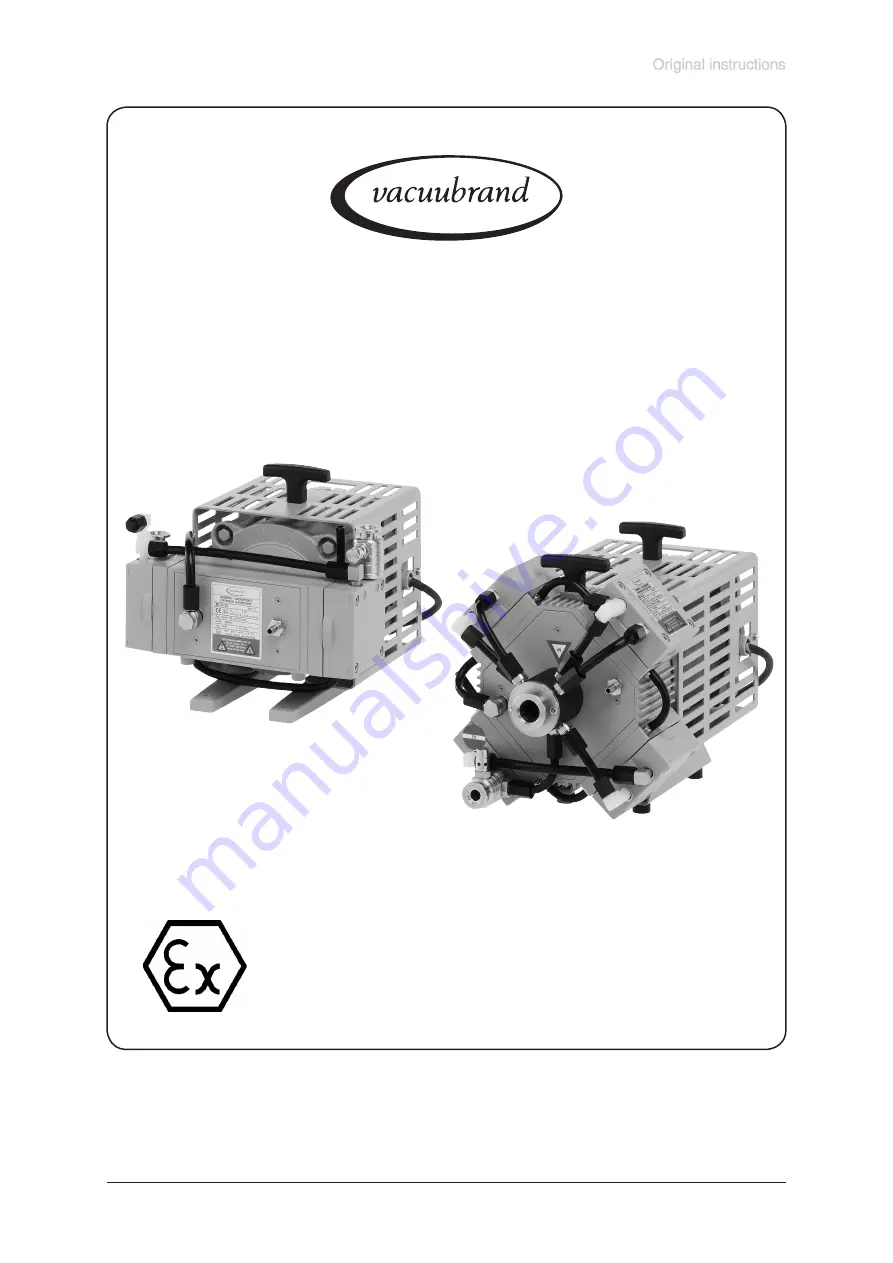
page 1 of 75
Documents are only to be used and distributed completely and unchanged. It is strictly the users´ responsibility to check carefully
the validity of this document with respect to his product. manual-no.: 999128 / 29/04/2014
Chemistry diaphragm pumps
with
ATEX conformity
MZ 2C EX
MD 4C EX
MV 10C EX
MZ 2C EX + AK + EK
MZ 2C EX + IK + EK
MD 4C EX + AK + EK
MV 10C EX + AK + EK
Technology for Vacuum Systems
Instructions for use