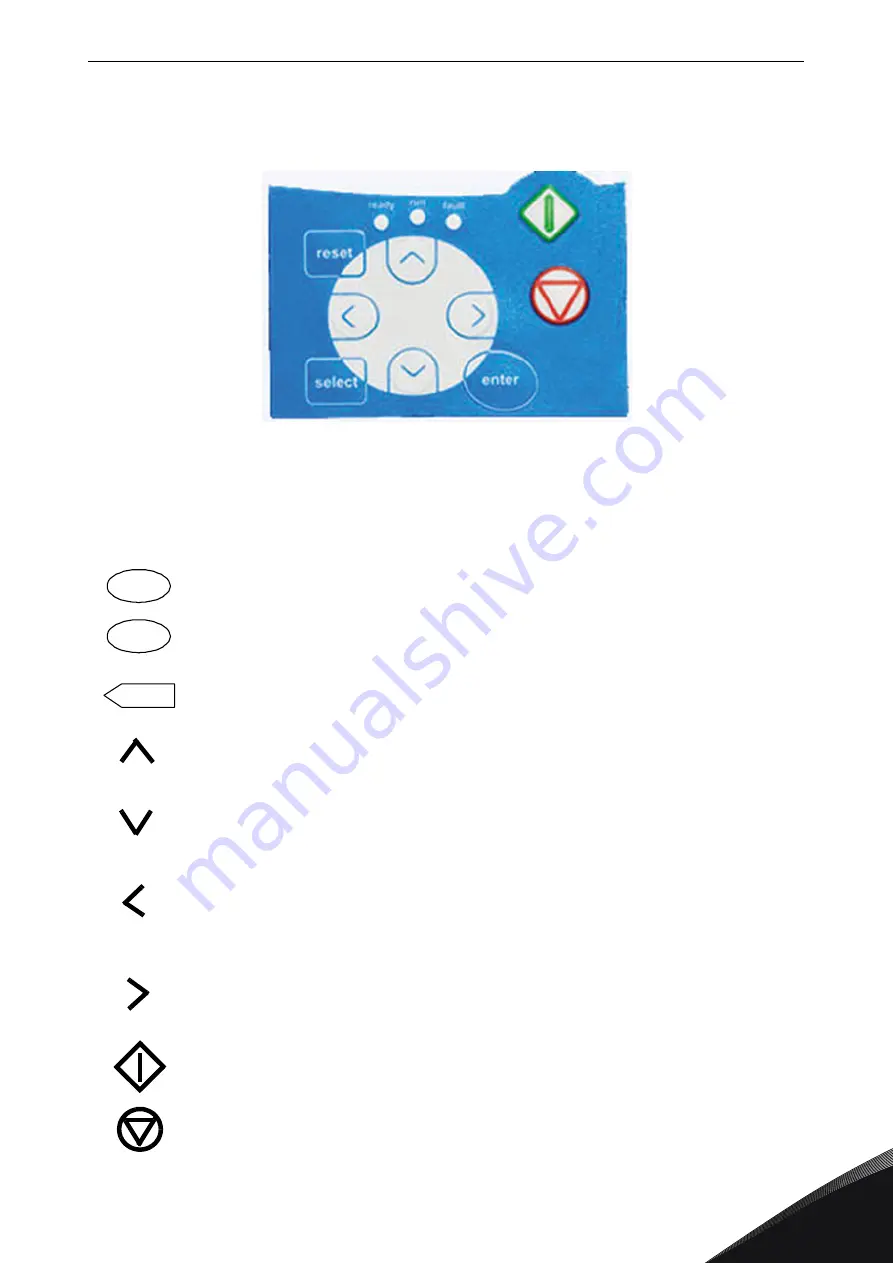
CONTROL KEYPAD
vacon • 71
24-hour s358 (0)201 212 575 • Email: [email protected]
9
9.2
Keypad push-buttons
The Vacon alphanumeric control keypad features 9 push-buttons that are used for the control of the
frequency converter (and motor), parameter setting and value monitoring.
Figure 43. Keypad push-buttons
9.2.1
Button descriptions
= This button is used to reset active faults (see Chapter 9.3.4).
= This button is used to switch between two latest displays. May be useful when
you want to see how the changed new value influences some other value.
= The Enter button serves for:
1) confirmation of selections
2) fault history reset (2…3 seconds)
= Browser button up
Browse the main menu and the pages of different submenus.
Edit values.
= Browser button down
Browse the main menu and the pages of different submenus.
Edit values.
= Menu button left
Move backward in menu.
Move cursor left (in parameter menu).
Exit edit mode.
Hold down for 3 seconds to return to main menu.
= Menu button right
Move forward in menu.
Move cursor right (in parameter menu).
Enter edit mode.
= Start button
Pressing this button starts the motor if the keypad is the active control place. See
Chapter 9.3.3.
= Stop button
Pressing this button stops the motor (unless disabled by parameter R3.4/R3.6).
See Chapter 9.3.3.
11525_00
reset
select
enter