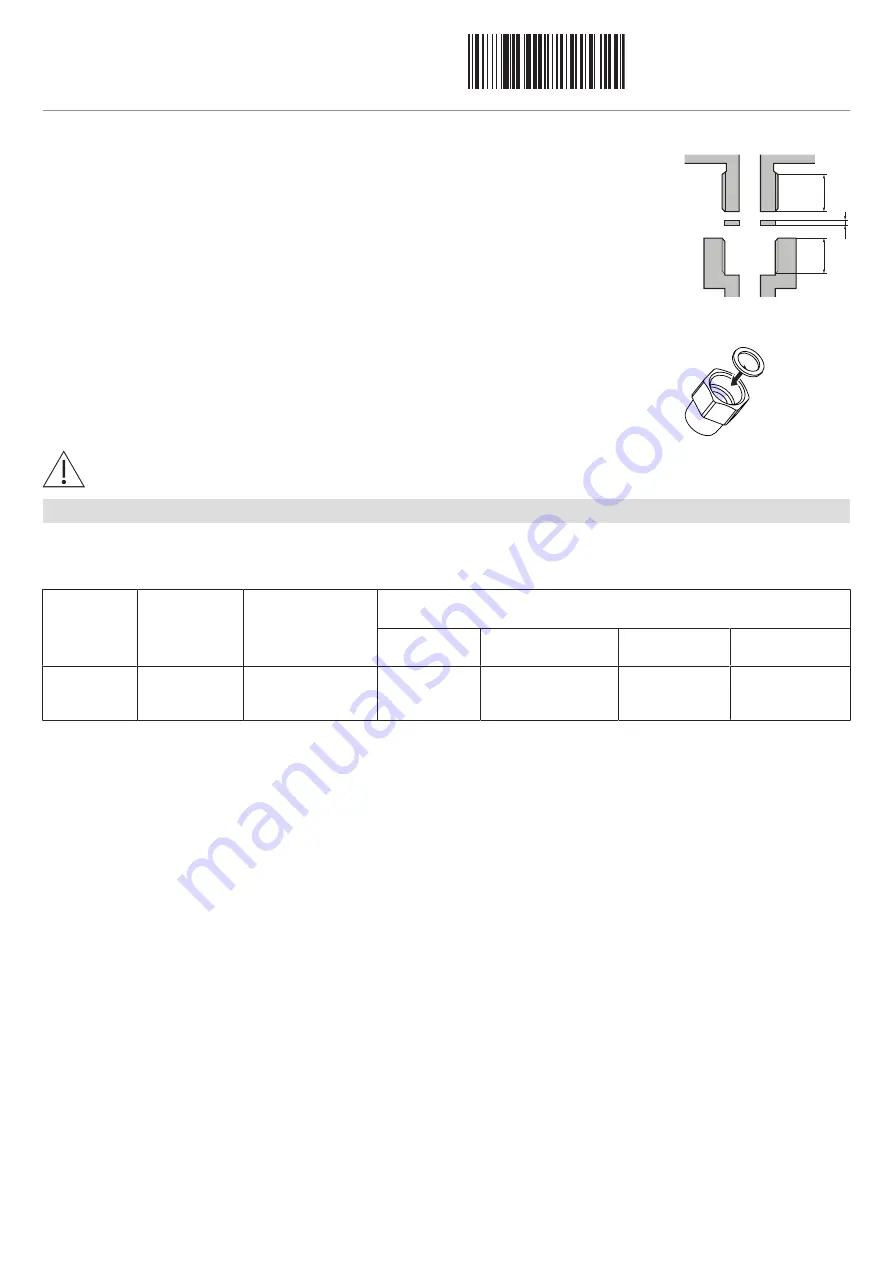
Installation instructions
Built-in variants of gas hob
GAS731
1094429-04
26/07/2023
1094429-04
7
Thread length
Thread length of gas connection on the appliance (external thread)
So
is 16 mm. If the thread
length of the on-site counterpart (internal thread)
Si
is longer than 17 mm, the front-end seal is no
longer guaranteed through the supplied green sealing ring H64006 with a height of 1.5 mm.
In this case, the yellow sealing ring 1030096 with a height
h
of 5 mm is to be used as it provides a
leak tight connection for on-site thread lengths of up to 20.5 mm.
Si
So
h
½-inch conical thread
If the gas connection has a conical thread, the transition piece and sealing ring must first be
screwed onto the appliance. The transition piece has a conical external thread R ½-inch in accord-
ance with ISO 7/11. In the case of a conical screw connection, the thread makes the seal, which is
why the thread must be sealed with hemp or Teflon tape.
After the gas has been connected, leak and function testing must be carried out by a registered gas fitter.
Conversion to another gas type
The appliance is set up for a certain gas type, which is also recorded on the identification plate. The appliance can be converted to an-
other type of gas using the nozzle sets supplied (others available as accessories). This requires the burner injector nozzles and the gas
tap bypass nozzles be changed.
Type
Default gas
setting
Nozzle set
(supplied)
Additional nozzle sets available for country-specific combinations of gas type
and connection pressure
Liquid gas G30,
50 mbar
Natural gas L/K (G25/
G25.3), 25 mbar
Natural gas G20,
13 mbar
Natural gas G20,
25 mbar
GAS731GKBZ Natural gas H, E
(G20), 20 mbar
Liquid gas butane/
propane (G30/31),
28–30/37 mbar
Nozzle set
1015475
Nozzle set 1015476
Nozzle set
1015478
Nozzle set
1015477
All the nozzles are numbered to avoid any mix-up.
Always disconnect the appliance from the electricity and gas mains before changing the nozzles.
Changing the injector nozzles
▸
Remove the pan supports and burners.
▸
Remove injector nozzles (using 7 mm socket wrench).
▸
Screw in the new injector nozzles (according to the table) as far as they will go.
Changing the bypass nozzles
▸
Pull all control knobs up and off.
▸
Loosen all the screws in the burner plates (torx no. 10) and then remove the burner plates.
▸
Remove the drawers or cabinet front to gain access from below.
Flush mounted
Surface mounted
A
Remove all the nuts from around the circumference of
the appliance (using 8 mm socket wrench).
A
Loosen any adjusting braces and lift gas hob up and out
of the cut-out.
B
Supporting the appliance tray with one hand, unscrew
the two knurled nuts in opposite corners.
B
Remove lateral screws from around the circumference
of the appliance (torx no. 20).
C
Let the appliance tray slide down and remove from the
kitchen cabinet.
C
Lift the base plate upwards and carefully remove from
the base.
▸
Remove the springs and microswitch from the gas taps.
▸
Remove the bypass nozzle from each gas tap and screw in the new nozzle as far as it will go.
▸
Put back the microswitch and springs.