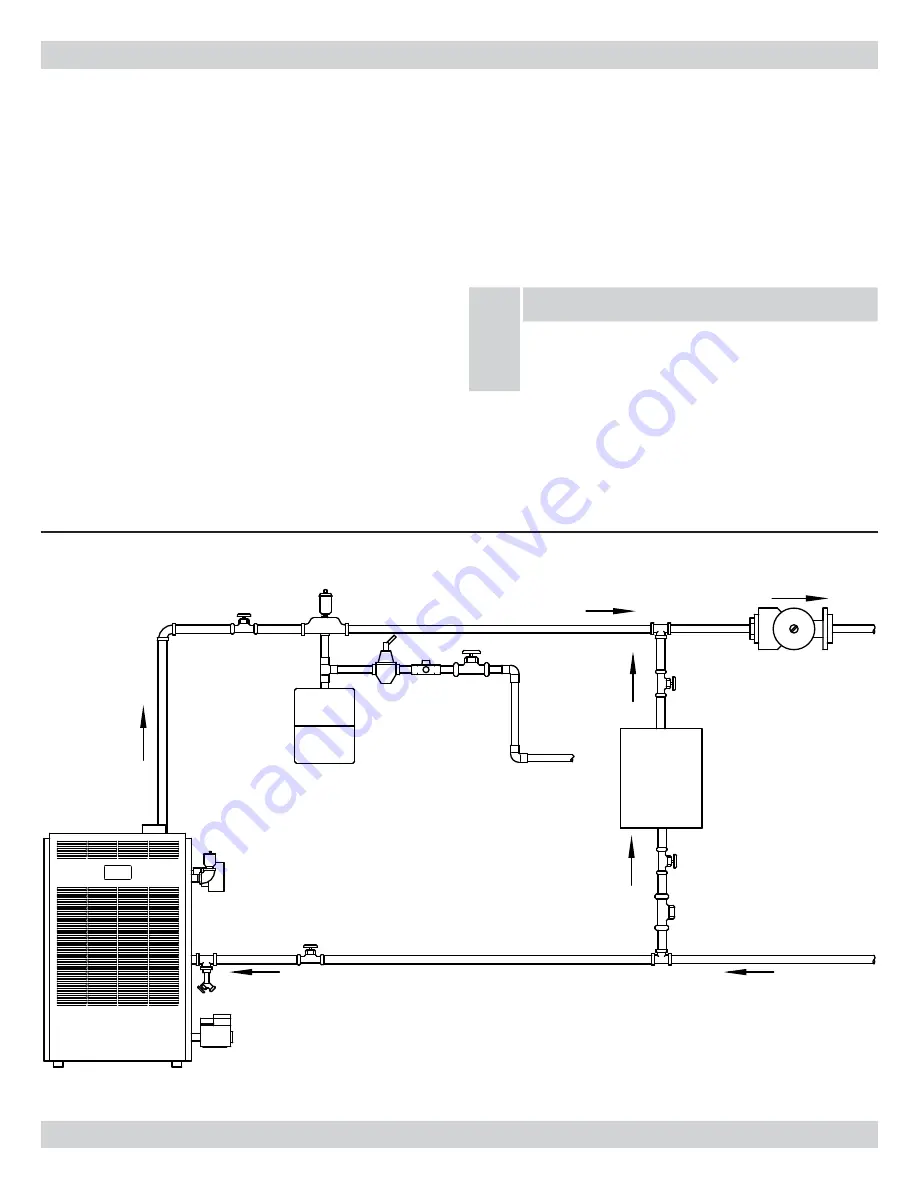
5
Connect supply and return piping as suggested in
1.
Fig-
ure #2
below when the boiler is used in connection with
refrigerated systems:
The chilled medium MUST BE IN PARALLEL with
A.
the boiler.
Use appropriate valves to prevent the chilled medium
B.
from entering the heating boiler.
During heating cycle open valves A and B. Close
t
valves C and D.
During cooling cycle open valves C and D, close valves
t
A and B.
Maintain a minimum clearance of 1 inch (2.54 cm) to
C.
hot water pipes. In air handling units where they may
be exposed to refrigerated air circulation, the boiler
piping system MUST be supplied with flow control
valves or other automatic means to prevent grav-
ity circulation of the boiler water during the cooling
cycle.
CONNECTING SUPPLY AND RETURN PIPING
EXPANSION
TANK
B
A
D
CHECK
VALVE
CIRCULATOR
FROM HEATING
AND COOLING
ELEMENT
SUPPLY PIPING
TO HEATING
AND COOLING
ELEMENT
WATER
CHILLER
C
RETURN PIPING
FEED
WATER
NOTICE
* Reduced pressure back flow preventer must be used
under provisions required by the Environmental Pro-
tection Agency, (EPA).
Hot water boilers installed above radiation level must be
2.
provided with a low water cut-off device at the time of
boiler installation.
When a boiler is connected to a heating system that
3.
utilizes multiple zoned circulators, each circulator must
be supplied with a flow control valve to prevent gravity
circulation.
Figure 1 - Near Boiler Supply & Return Piping
National Excelsior Company
www.excelsiorhvac.com
Subject to change without notice.