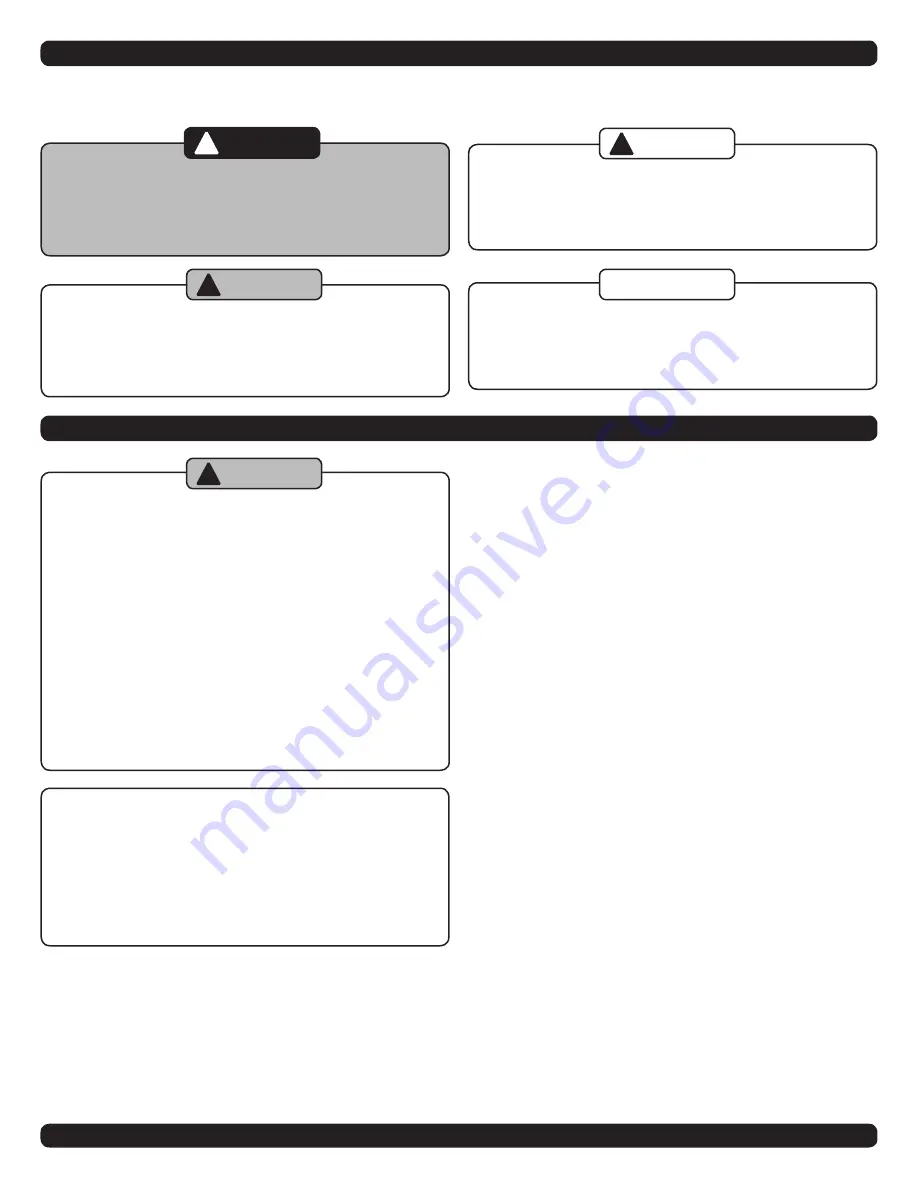
3
III - RULES fOR SAfE InSTALLATIOn And OPERATIOn
ImPORTAnT:
Failure to follow these instruc
-
tions could cause a malfunction of the boiler
and result in death, serious bodily injury, and/or
property damage. For assistance or additional
information, consult a qualified installer, service
agency, or the gas supplier.
II - SAfETy SymBOLS And wARnInGS
This appliance has been equipped for resi-
dential installations. If used for commercial
applications, any and all additional code re-
quirements must be adhered to for installa-
tion. This may require additional controls,
including but not limited to an external wa-
ter cut off, a manual reset high temperature
limit, and wiring and/or piping modifications.
The manufacturer is not responsible for any
field installation changes made to a boiler
installation which are not described or ac-
knowledged in this manual.
WARNING
!
I
ndicates an imminently hazardous situation
which, if not avoided, will result in death,
serious injury or substantial property dam-
age.
DANGER
!
Indicates a potentially hazardous situation
which, if not avoided, could result in death,
serious injury or substantial property dam-
age
.
WARNING
!
Indicates a potentially hazardous situation
which, if not avoided, could result in minor or
moderate injury or property damage
.
CAUTION
!
Indicates special instructions on installation,
operation or maintenance which are important
but not related to personal injury hazards.
NOTICE
The following defined symbols are used throughout this manual to notify the reader of potential
hazards of varying risk levels.
Check all applicable state and local building
1.
codes and utility company requirements before
installation. This installation must conform with
these requirements in their entirety. In the ab
-
sence of these codes, use NFPA installation
codes and good industry practice.
Before servicing the boiler, allow it to cool. Al
-
2.
ways shut off any electricity and gas supply con
-
nected to the boiler prior to servicing.
Inspect gas line for leaks.
3.
Be certain gas input rate is correct. Overfiring
4.
may result in early failure of the boiler compo
-
nents. This may cause dangerous operation.
Underfiring may result in too much air for the pre-
mix burner causing poor or loss of combustion.
Never vent the products of combustion from this
5.
boiler to an enclosed space. Always vent to the
outdoors. Never vent to another room or to in
-
side a building.
Be sure there is adequate outdoor air supply to
6.
boiler for complete combustion.
Follow a regular service and maintenance sched
-
7.
ule for efficient and safe operation.
Keep boiler area clean of debris and free of com
-
8.
bustible and flammable materials.
Proper through-the-wall or through-the-roof com
-
9.
bustion venting shall be in accordance with the
materials and methods described in this manual.
Installation must comply with local codes.