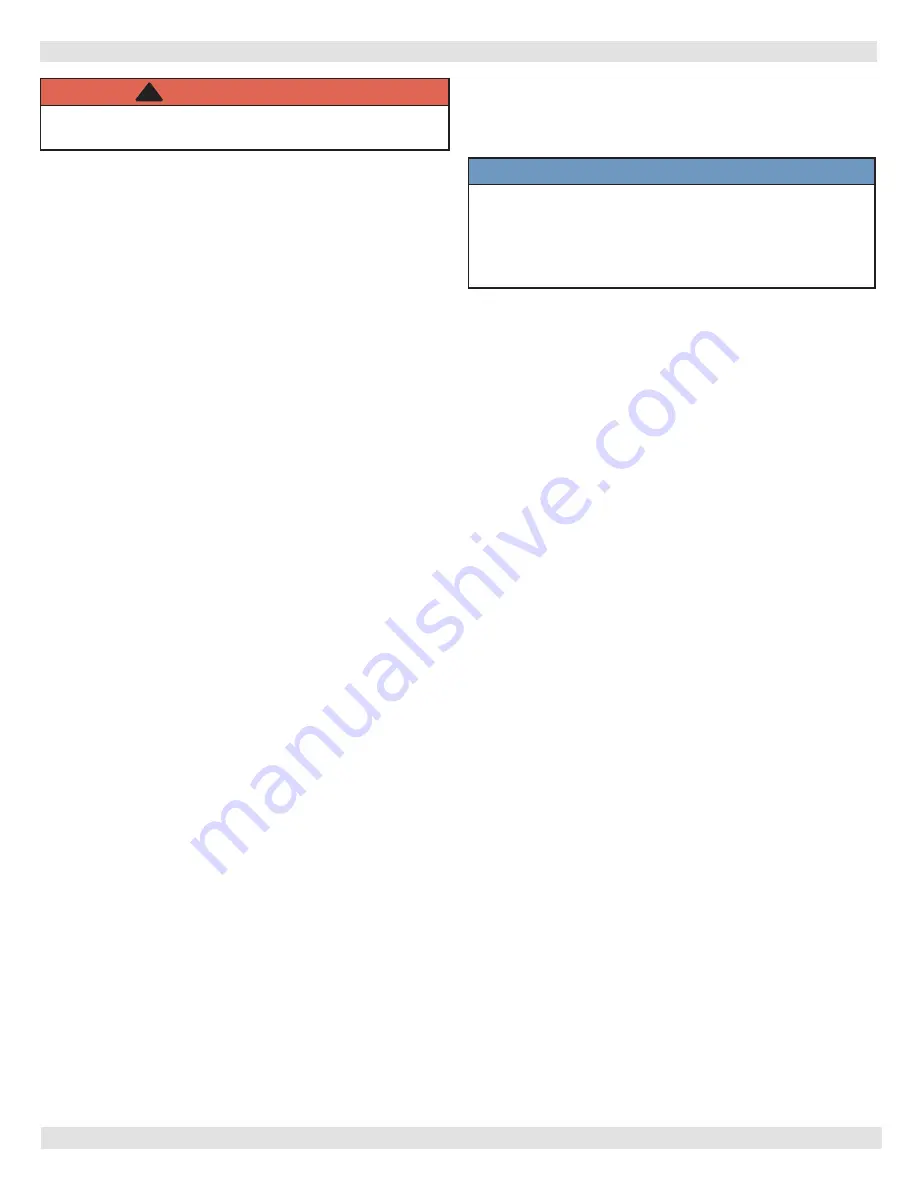
16
6 - CHIMNEY AND VENT PIPE CONNECTION
Connecting The Vent Damper And Vent Connector
Refer to Figure 1, page 4 for size and location of vent (flue
opening).
NOTICE
Damper blade on furnished vent damper has 1/2
square inch hole (approximately 3/4” diameter).
Boilers equipped with intermittent ignition, hole
should be plugged by using plug supplied with vent
damper.
1.
Position furnished vent damper on top of flue outlet
collar. Fasten damper securely to flue outlet collar with
sheet metal screws. Verify damper blade has clearance
to operate inside of diverter. Do not modify either draft
diverter or vent damper during installation.
As An Option
Damper may be installed in horizontal or vertical
position, closer to flue outlet collar preferred. See
Figures 8, 9 and 10 and enclosed vent damper
instructions.
2.
Install vent damper to service only single boiler for
which it is intended. Damper position indicator shall be
in visible location following installation. Locate damper
so it is accessible for servicing. See Figure 9.
3.
Damper must be in the open position when appliance
main burners are operating.
4.
Boiler is equipped with factory wired harness that plugs
into vent damper.
5.
Slope pipe up from boiler to chimney not less than 1/4”
per foot.
6.
Run pipe as directly as possible with as few elbows as
possible.
7.
Do not connect to fireplace flue.
8.
End of vent pipe must be flush with inside face of
chimney flue. Use a sealed-in thimble for chimney
connection.
Fasten sections of vent pipe with sheet metal screws to
make piping rigid. Support horizontal potions of vent
system to prevent sagging. Use stovepipe wires every 5’ to
support pipe from above. Use double wall vent pipe if vent
pipe must go through crawl space. Where vent pipe passes
through combustible wall or partition, use ventilated metal
thimble. Thimble should be 4 inches larger in diameter than
vent pipe.
Removing Existing Boiler From Common Venting
System
When an existing boiler is removed from common venting
system, common venting system is likely to be too large for
proper venting of appliances remaining connected to it.
At time of removal of existing boiler, following steps shall
be followed with each appliance remaining connected to the
common venting system placed in operation, while other
appliances remaining connected to common venting system
are not in operation.
1.
Seal any unused openings in the common venting
system.
2.
Visually inspect the venting system for proper size and
horizontal pitch and determine there is no blockage or
restriction, leakage, corrosion and other deficiencies
which could cause an unsafe condition.
3.
Insofar as is practical, close all building doors and
windows and all doors between the space in which the
appliances remaining connected to the common venting
system are located and other spaces of the building.
Turn on clothes dryers and any appliance not connected
to the common venting system. Turn on any exhaust
fans, such as range hoods and bathroom exhausts, so
they will operate at maximum speed. Do not operate a
summer exhaust fan. Close fireplace dampers.
4.
Place in operation the appliance being inspected. Follow
the lighting instructions. Adjust thermostat so appliance
will operate continuously.
5.
Test for spillage at the draft hood relief opening after
5 minutes of main burner operation. Use the flame of
a match or candle, or smoke from a cigarette, cigar or
pipe.
6.
After it has been determined that each appliance
remaining connected to the common venting system
properly vents when tested as outlined above, return
doors, windows, exhaust fans, fireplace dampers and
any other gas-burning appliance to their previous
conditions of use.
7.
Any improper operation of the common venting system
should be corrected so the installation conforms with
the National Fuel gas Code, ANSI Z223.1/NFPA 54,
and/or the Natural Gas and Propane Installation Code,
CAN/CSA B149.1. When re-sizing any portion of the
common venting system, the common venting system
should be re-sized to approach the minimum size
determined using the appropriate tables in Chapter 13
of the National Fuel Gas Code, ANSI Z223.1/NFPA 54,
and/or the Natural Gas and Propane Installation Code,
CAN/CSA B149.1.
WARNING
Do not connect boiler to any portion of mechanical
draft system operating under positive pressure.
!
PN 240013087 Rev. A [09/30/2020]