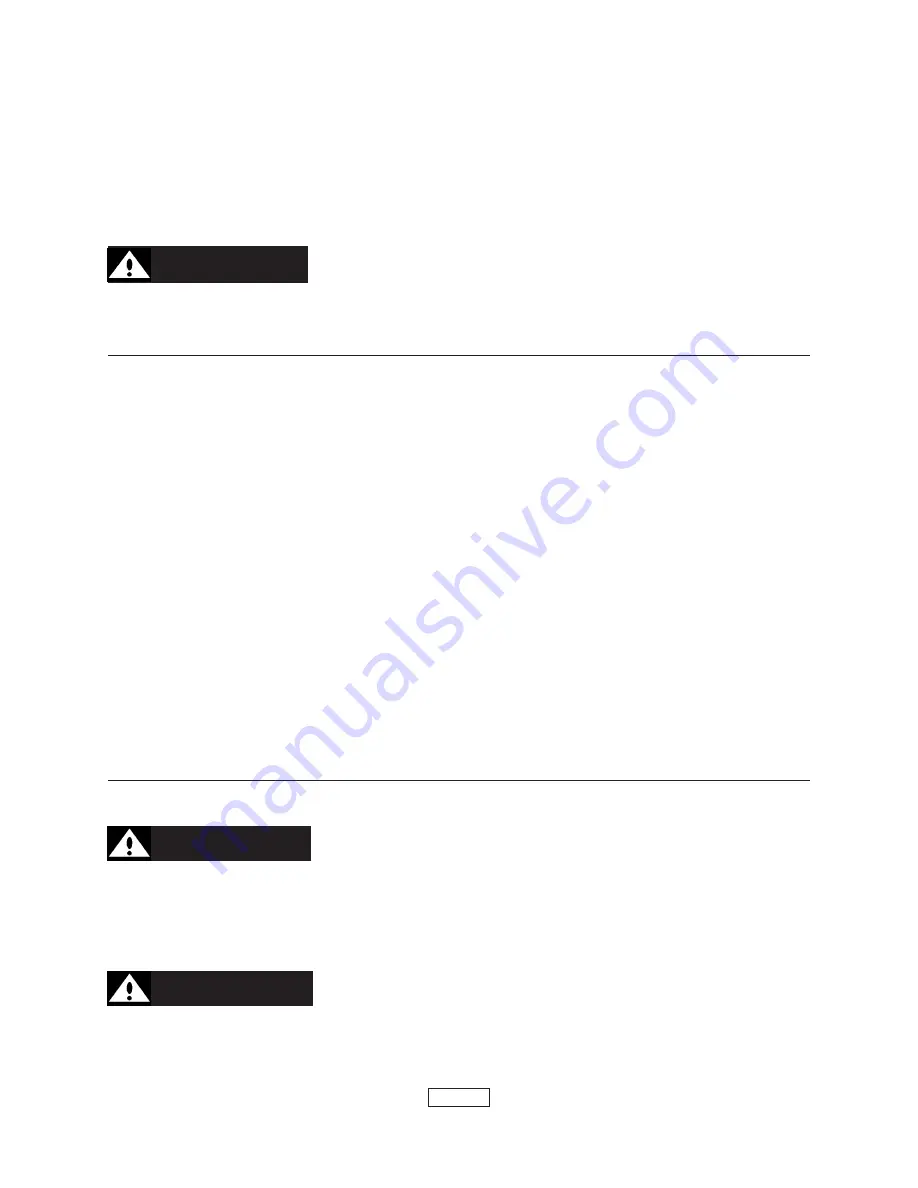
LIGHTING INSTRUCTIONS
LIGHTING INSTRUCTIONS
LIGHTING INSTRUCTIONS
LIGHTING INSTRUCTIONS
LIGHTING INSTRUCTIONS
WARNING:
WARNING:
WARNING:
WARNING:
WARNING:
IF YOU DO NOT FOLLOW THESE INSTRUCTIONS EXACTLY,
A FIRE OR EXPLOSION MAY RESULT CAUSING PROPERTY DAMAGE, PERSONAL
INJURY OR LOSS OF LIFE.
Before any procedures are attempted on this appliance, it is necessary to
determine if the ignition system is electric or standing pilot. If you are un-certain,
contact the manufacturer before proceeding.
CA
CA
CA
CA
CAUTION:
UTION:
UTION:
UTION:
UTION:
Before lighting any type of pilot burner (standing or
intermittent), make certain the hot water boiler and system are full of water to
minimum pressure of 12 lbs. per square inch in the system, and also make certain that
the system is vented of air. Set the operating control of thermostat to a “below”
normal setting. Refer to the following appropriate lighting instruction.
ELECTRICAL WIRING
ELECTRICAL WIRING
ELECTRICAL WIRING
ELECTRICAL WIRING
ELECTRICAL WIRING
SEE ADDENDUM " A" FOR WIRING DIAGRAMS
AND COMPONENT CODING.
Electrical wiring must conform with the National Electrical Code, ANSI/NFPA No. 70-1990
when installed in the United states, the CSA C22.1 Canadian Electrical Code, Part 1, when
installed in Canada, and/or the local authority having jurisdiction.
WARNING:
WARNING:
WARNING:
WARNING:
WARNING:
1.When an external electrical source is utilized, the boiler, when
installed
MUST BE
MUST BE
MUST BE
MUST BE
MUST BE
electrically grounded in accordance with these requirements.
2. Install a fused disconnect switch between boiler and meter at a convenient location.
THERMOST
THERMOST
THERMOST
THERMOST
THERMOSTA
A
A
A
AT INST
T INST
T INST
T INST
T INSTALLA
ALLA
ALLA
ALLA
ALLATION
TION
TION
TION
TION
1. Thermostat should be installed on an inside wall about four feet above the floor.
2.
NEVER
install a thermostat on an outside wall.
3. Do not install a thermostat where it will be affected by:
A. Drafts
B. Hot or Cold Pipes
C. Sun Light
D. Lighting Fixture
E. Television
F. A Fireplace or Chimney
4. Check thermostat operation by raising and lowering thermostat setting as required to
start and stop the burners.
5. Instructions for the final adjustment of the thermostat are packaged with the thermostat
(adjusting heating anticipator, calibration, etc.)
PAGE 13