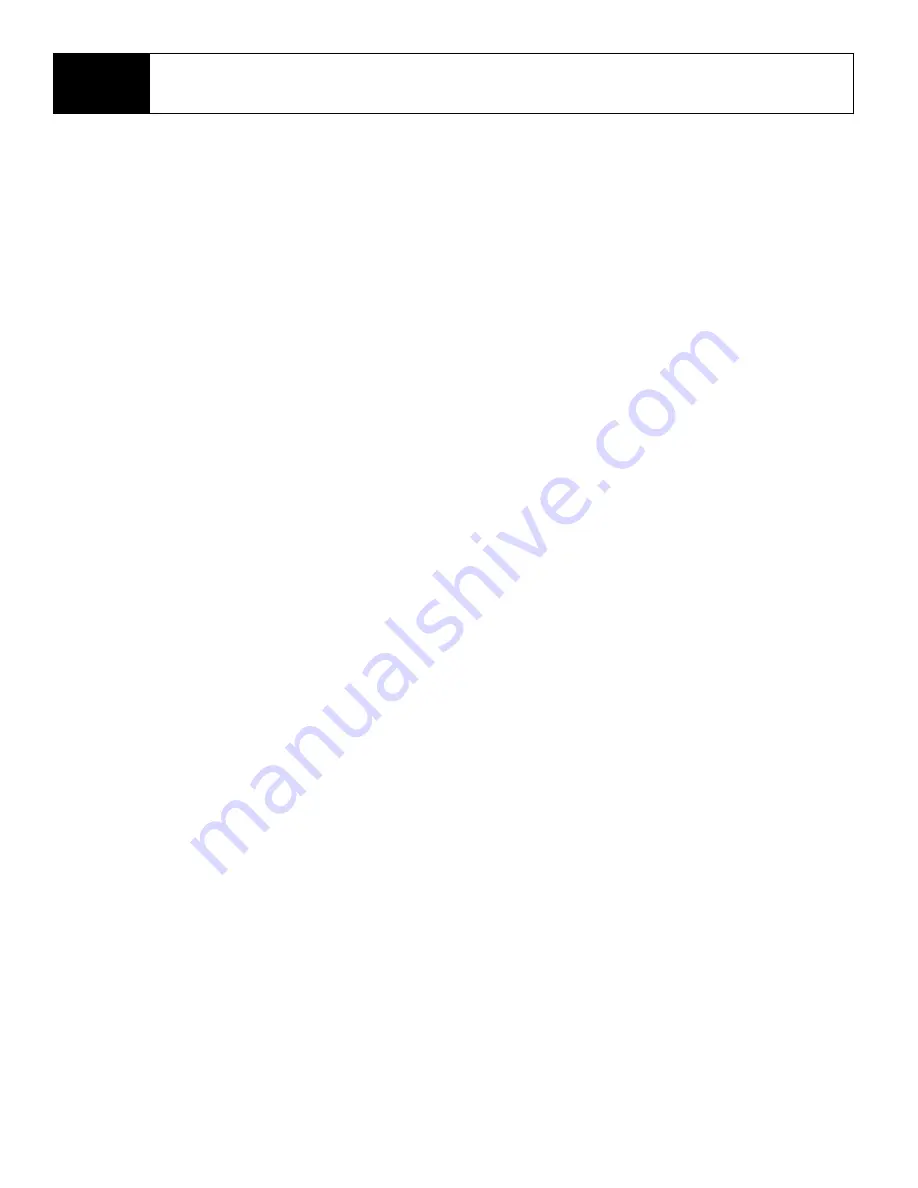
2-6
SL26/30SL Work Platform
M
ACHINE
P
REPARATION
& O
PERATION
Section
2.8
2.8 I
NTRODUCTION
General Functioning
The engine directly drives a hydraulic pump. The
pump supplies oil under pressure to operate all the
work platform functions. The oil flow is directed to the
different functions by electrically activated solenoid
valves.
Driving
With the Controller Key Switch
ON
, and the engine
running, both chassis and controller Emergency Stop
Switches
ON
, the Interlock Lever depressed, and the
Drive/Lift Switch on
DRIVE
, the machine will drive
forward or reverse at a speed proportional to the
angle the control lever is pushed or pulled.
Driving with the Platform Lowered
Selecting
HIGH SPEED
with the Drive Speed Switch
and moving the Control Lever forward or reverse with
the platform fully lowered will energize the cutout
relay thru the Platform Down Relay contacts, the
Series/Parallel Coils, the Proportional Coil and the
Forward or Reverse Coil to allow oil to flow into the
Parking Brake (releasing the Brake) and serially
through the Hydraulic Motors. The Proportional Valve
closes or opens in proportion to the movement of the
Control Lever (from center). As the Proportional
Valve closes, more oil is allowed to flow to the For-
ward or Reverse Valve increasing drive speed.
Selecting
HIGH TORQUE
(low speed) with the Drive
Speed Switch the Series/Parallel Valves are not
energized, allowing the oil to divide through the
Hydraulic Motors producing the high torque/low drive
speed.
Driving with the Platform Elevated
Raising the platform (see
RAISING AND LOWERING
THE PLATFORM
, below) opens the Platform Down
Switch which cuts power to the Platform Down Relay.
This energizes the cutout relay thru the tilt sensor
and prevents the axle float valve solenoid from ener-
gizing, locking the axle in place. Also de-energized
are the Series/Parallel coils and the controller high
speed circuit. When raised, the platform will only
drive at low speed (motors in parallel) and then
only
if the front axle parallel with the rear axle and the
platform is level.
Steering
On the top of the Control Lever is a momentary
rocker switch for steering the machine left and right.
Pressing the right or left side of the rocker switch will
energize the Steering Coils and allow oil to flow
through the Steering Valve to the Steering Cylinder.
Releasing the rocker switch de-energizes the Steer-
ing Coils and holds the Steering Cylinder in position.
The Steering Cylinder will not automatically
return to center. The Steering Switch must be
activated to change the wheels direction
.
Leveling
With the controller key switch
ON
(and the engine
running), both chassis and controller emergency stop
switches
ON
, and the Level/Drive/Lift switch on
LEVEL, the machine can be tilted right or left with the
side/side switch forward and backward with the fore/
aft switch to allow centering of the platform bubble
indicator. The side/side switch and the fore/aft switch
energize the steering bypass coil, to direct oil to the
tilt valves, and the tilt valves directing oil to the right/
left tilt cylinder and fore/aft tilt cylinder, respectively.
Raising And Lowering The Platform
With the Controller Key Switch
ON
(and the engine
running), both chassis and controller Emergency
Stop Switches
ON
, the Interlock Lever depressed,
and the Drive/Lift Switch on
LIFT
, the machine will
elevate at a speed proportional to the angle the Con-
trol Lever is pushed forward.
Pushing forward on the Control Lever energizes the
Cutout Relay thru the tilt sensor, Proportional Coil,
Up Coil and accelerator or throttle relay to increase
the engine speed. The greater the angle (from cen-
ter) of the Control Lever the more the Proportional
Valve closes. As the Proportional Valve closes more
oil is allowed to flow through the Lift Valve to the Lift
Cylinder increasing lift speed.
Lowering the platform electrically energizes the
Down Alarm and the Down Coil. This allows the oil to
flow out of the Lift Cylinder through an orifice, which
controls the rate of descent, then back to tank. Dur-
ing the last 304 mm (12 in.) of lowering the Cushion
Down Valve is energized forcing the oil thru another
orifice slowing the platform rate of descent. Lowering
the platform manually with the Emergency Down
Valve allows the oil to flow out of the Lift Cylinder in
the same manner but there is no Down Alarm.
Summary of Contents for SL26SL
Page 1: ...European Specification ...
Page 4: ...ii SL26 30SL Work Platform FORWARD NOTES ...
Page 12: ...1 4 SL26 30SL Work Platform INTRODUCTION SPECIFICATIONS Section 1 3 NOTES ...
Page 24: ...2 12 SL26 30SL Work Platform MACHINE PREPARATION OPERATION Section 2 13 NOTES ...
Page 48: ...4 6 SL26 30SL Work Platform TROUBLESHOOTING Section 4 2 NOTES ...
Page 54: ...5 6 SL26 30SL Work Platform SCHEMATICS Section 5 2 NOTES ...
Page 59: ...SL26 30SL Work Platform 6 5 ILLUSTRATED PARTS BREAKDOWN 6 1 NOTES ...
Page 63: ...SL26 30SL Work Platform 6 9 ILLUSTRATED PARTS BREAKDOWN 6 1 NOTES ...
Page 65: ...SL26 30SL Work Platform 6 11 ILLUSTRATED PARTS BREAKDOWN 6 1 ...
Page 67: ...SL26 30SL Work Platform 6 13 ILLUSTRATED PARTS BREAKDOWN 6 1 ...
Page 69: ...SL26 30SL Work Platform 6 15 ILLUSTRATED PARTS BREAKDOWN 6 1 ...
Page 71: ...SL26 30SL Work Platform 6 17 ILLUSTRATED PARTS BREAKDOWN 6 1 ...
Page 83: ...SL26 30SL Work Platform 6 29 ILLUSTRATED PARTS BREAKDOWN 6 1 ...
Page 85: ...SL26 30SL Work Platform 6 31 ILLUSTRATED PARTS BREAKDOWN 6 1 ...
Page 95: ...SL26 30SL Work Platform 6 41 ILLUSTRATED PARTS BREAKDOWN 6 1 ...
Page 97: ...SL26 30SL Work Platform 6 43 ILLUSTRATED PARTS BREAKDOWN 6 1 ...
Page 99: ...SL26 30SL Work Platform 6 45 ILLUSTRATED PARTS BREAKDOWN 6 1 ...
Page 101: ...SL26 30SL Work Platform 6 47 ILLUSTRATED PARTS BREAKDOWN 6 1 ...
Page 103: ......