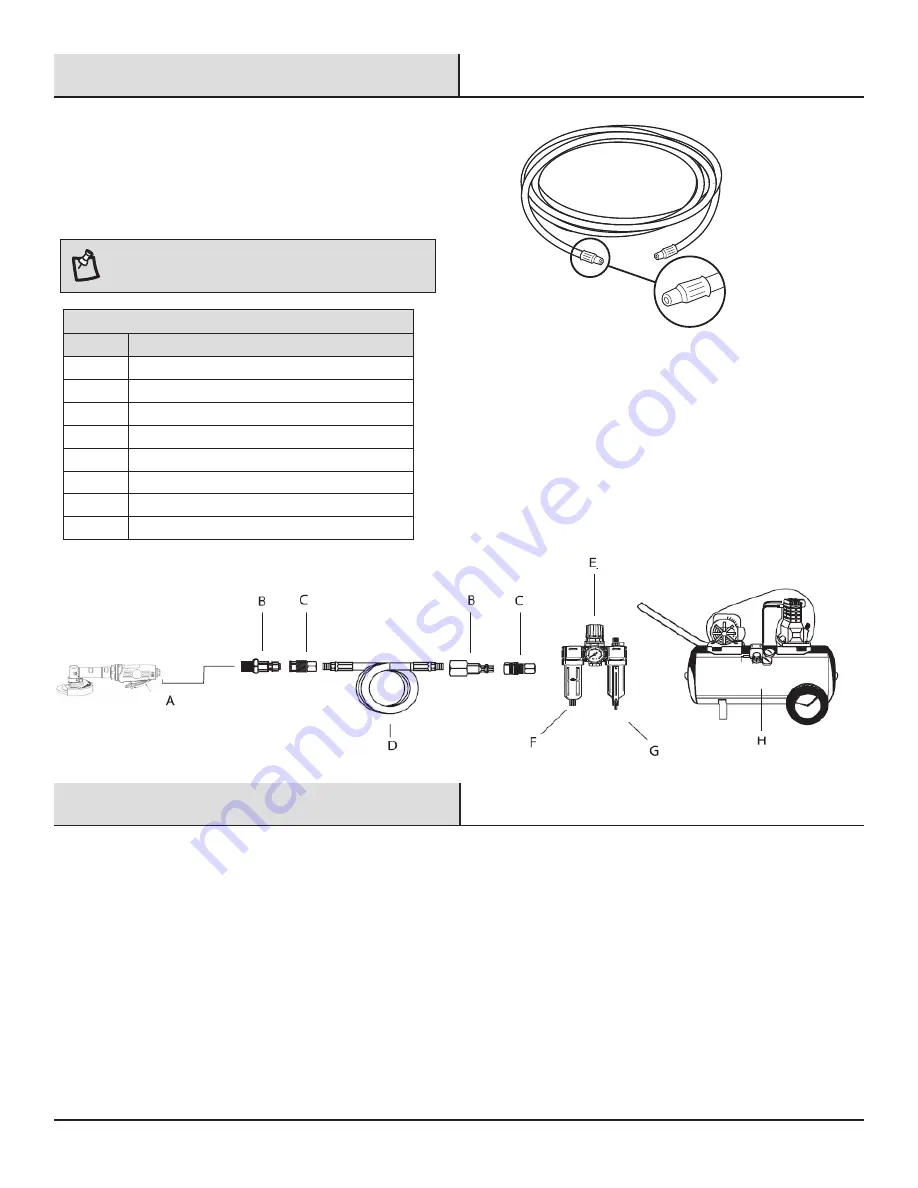
Universal Tool a Division of Florida Pneumatic Mfg. Corp.
851 Jupiter Park Lane, Jupiter FL 33458
Universal Air Tools Company Ltd.
Unit 8 Lane End Industrial Park, High Wycombe, HP14 3BY, UK
Installation
1
Cleaning the air hose
□
A 3/8" air hose is required, with a maximum length of 25 ft.
□
Clean the air hose of accumulated dust and moisture
before connecting it to the air supply.
NOTE:
If a longer air hose is required, connect a 1/2"
air hose to the 3/8" air hose to ensure the drill has the
necessary air supply.
Recommended Air Line Set-Up
Part
Description
A
Air Tool
B
Quick Plug
C
Quick Coupler
D
Air Hose
E
In-line Regulator
F
In-line Lubricator
G
In-line Filter
H
Air Compressor
Ensure the air line is shut-off and drained of air before removing this tool for service or changing sockets. This will prevent the tool from
operating if the throttle is accidentally engaged.
LUBRICATION
□
An in-line filter-regulator-lubricator is recommended as it increases tool life and keeps the tool in sustained operation.
□
Regularly check and fill the in-line lubricator with air tool oil. Avoid using excessive amounts of oil.
□
Adjust the in-line lubricator by placing a sheet of paper next to the tool’s exhaust ports and holding the throttle open approximately 30
seconds. The lubricator is properly set when a light stain of oil collects on the paper.
□
If it is necessary to store the tool for an extended period of time (overnight, weekend, etc.), generously lubricate the tool through the air
inlet. Run the tool for approximately 30 seconds to ensure the oil is evenly distributed throughout the tool. Store the tool in a clean and
dry environment.
□
Recommended lubricants: Air tool oil or any other high grade turbine oil containing moisture absorbent, rust inhibitors, metal wetting
agents, and an EP (extreme pressure) additive.
Maintenance