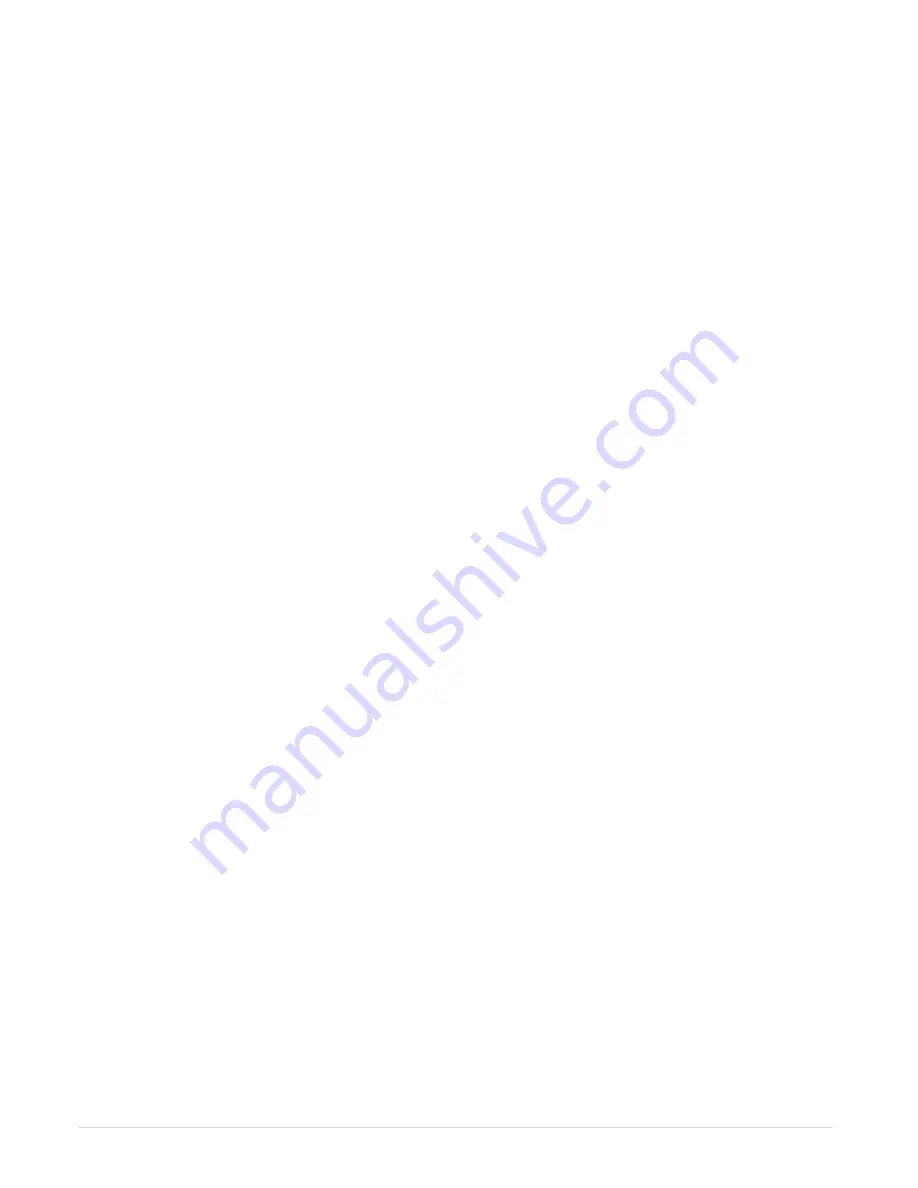
United Process Controls, Inc.
Oxyfire-LT Installation/Operation Manual
9 |
P a g e
2 INSTALLATION
2.1
APPLICATION CONFIRMATION
Call your local MMI Representative or MMI directly when planning your sensor installation. The
sensor location and depth of insertion are critical factors to consider and vary with different
applications. MMI Application Engineers are equipped to help with such information in many
applications.
2.2
ITEMS REQUIRED
To perform a sensor installation, you will need the following items:
Supplied with standard Oxyfire models:
1.
K T/C models: 2-conductor solid extension wires
2.
Polyvinyl coated copper wire, two conductor, stranded, 18 gauge, twisted pair,
shielded – Belden #6341PC
Ceramic fiber blanket insulation and/or refractory cement.
Sensor Reference Air: Clean, dry continuous air source – approximately 2 psi at 50 to
150cc/minute
Cooling Air: If the temperature of the sensor terminal head will exceed 300ºF (148ºC), air
should be blown across it to reduce the temp. The cooling air should be directed to flow
perpendicular across the sensor head.
2.3
SENSOR HOLE SIZE
The installation hole, through the refractory of the crown or wall, should be a minimum of 2 inches
(50mm) in diameter. The hole should always be straight, clean, and perpendicular to the wall or crown.
It is advised to always verify the hole size required for your application and sensor. MMI
Application Engineers can help with this matter.
2.4
INSTALLATION PORTS
The ports can be of different designs – open hole, threaded, and flanged. Applications with exterior
metal shells should use threaded or flanged type ports. Thread is 1.25” NPT size for standard Oxyfire
models. Applications with ceramic exterior shells may use the open hole, threaded, or flanged
connection ports. The flange or pipe will be cemented in to the refractory.