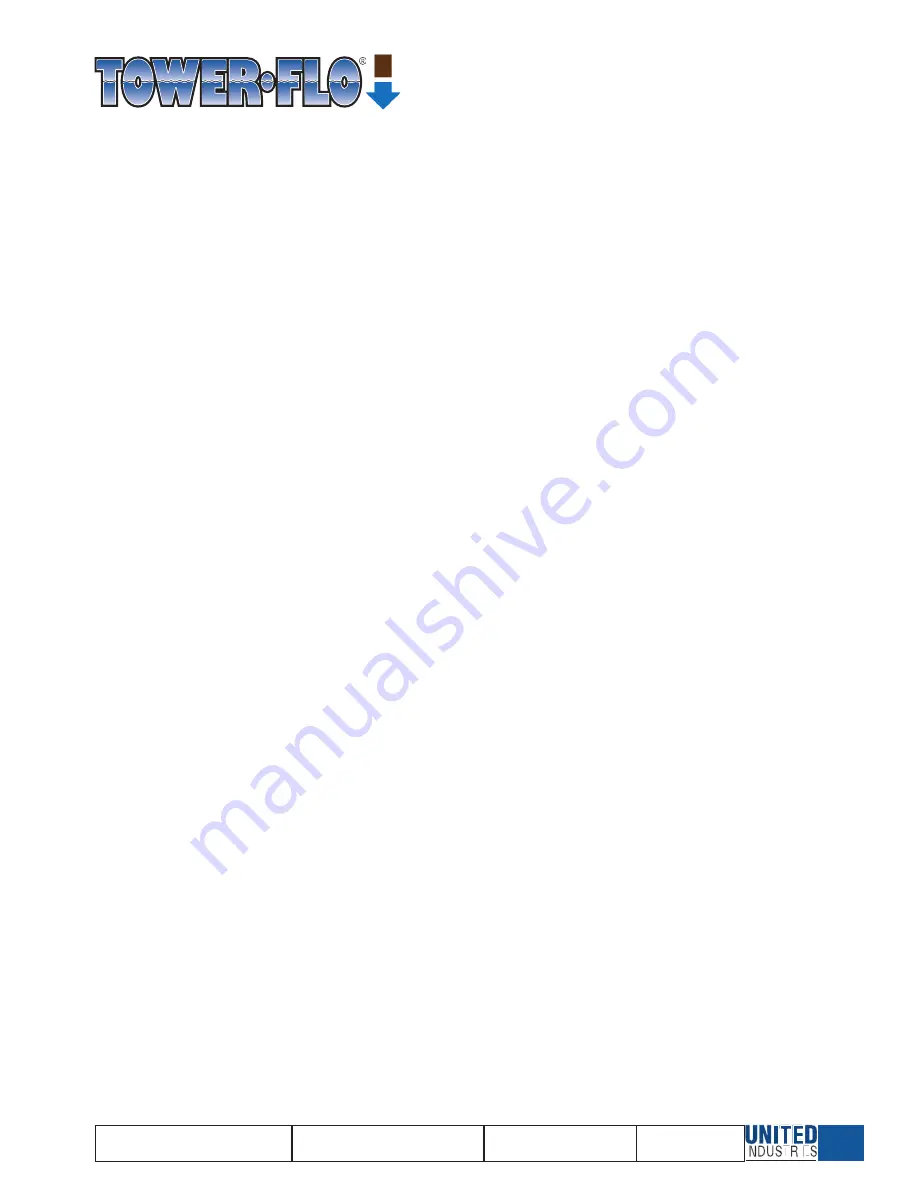
35
United Industries, Inc.
P.O. Box 58
Sterling, KS 67579
800-835-3272 • 620-278-3160
Fax 800-500-3115 • 620-278-3115
www.towerflo.com
Data presented here is the best available at the
time of publicaton. United Industries and/or its
representatives assume no liability for its use.
Form MEDINSP:3/11
Media Inspection
Series
TFW
The filter sand provided with your Tower-Flo
®
filter is permanent media and should never require replacement.
However, the media bed will function as a “concentrator” of both problem filtrates that resist removal by backwash
action, as well as water treatment deficiencies. Regular monthly media bed inspections will keep your filter operating
properly and can alert you to emerging water chemistry issues.
Media bed inspection requires accessing the media. Turn off the pump, close isolation valves in influent and effluent
piping to the filter, open the tank drain, open the air relief valve, remove the lid locking ring and the the clear tank
lid, close the tank drain when the water level is low enough to expose the surface of the media bed.
Inspection is a three step process; smell, look, feel:
• Smell to see if the media smells clean. A “septic” smell would indicate the presence of live biological contami
-
nants in the media bed and an issue with the biocide treatment. Sanitize the media bed with bleach.
• Look to see if the surface of the media bed is clean, smooth and flat. Remove any accumulation of fibrous materi
-
als (i.e., cottonwood tree seeds) or heavy materials that are not being removed by backwash action. The appear-
ance of “ridges and valleys” on the surface of the media bed would indicate the beginning of hard spots down in
the media bed (under the ridges) and an issue with water hardness control. Either remove the hardened media
and replace with an equal volume of new sand or recondition media bed with a muriatic acid wash to dissolve
calcium.
• Feel the sand at the surface to see if it is clean and loose. Probe the bed in several random places to a depth
of 8 to 12 inches to see if it is clean, loose and free of evidence of foreign matter, mudballs, oilballs, or hard
spots down in the media bed. If contamination is found, either remove the contaminated media and replace
with an equal volume of new sand or recondition media bed with a muriatic acid wash to dissolve calcium or
a low sudsing / low phosphate detergent to dissolve oilballs.
Resolution of problems revealed by your inspection requires the suggested remedies for the media bed (to treat the symp-
toms) as well as attention from those responsible for your water treatment / water chemistry program (to treat the problem).
After inspection, replace the vessel lid and the lid locking ring, open isolation valves and restart your filter system
according to the Start-Up Instructions.