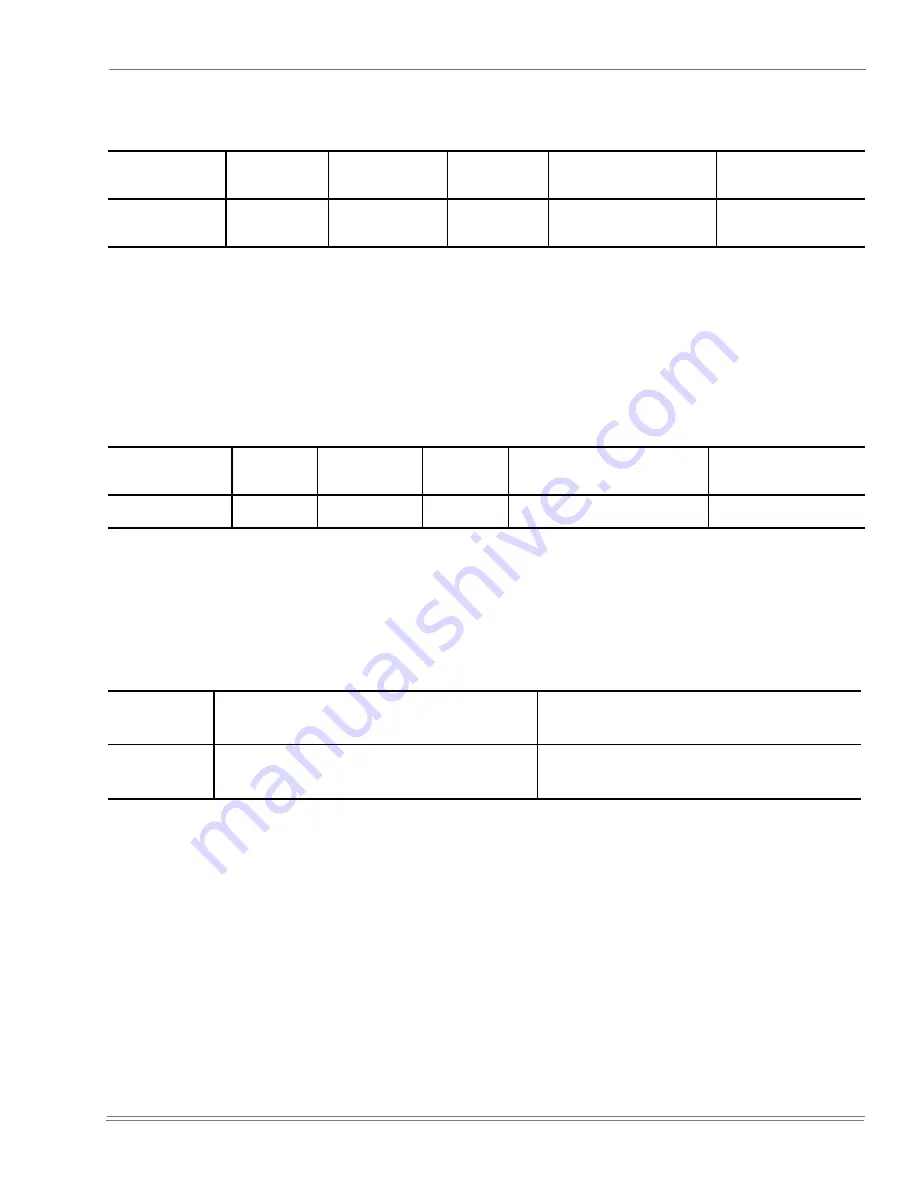
035-18518-001-B-0703
Unitary Products Group
11
TABLE 4: SUCTION LINES
*
†
Model Designation
Nominal Capac-
ity (Tons)
Refrigerant Flow
Rate
‡
(Lbs./Min.)
Type L Copper
Tubing (Inches
O.D.)
Refrigerant Gas Velocity
(FT./Min.)
Friction Loss
**
††
(PSI/100 Ft.)
HF-07
7-1/2
22
1-1/8
1-3/8
1-5/8
2050
1680
1140
4.3
1.6
0.7
*.
All horizontal suction lines should be pitched at least 1 inch every 20 feet in the direction of the refrigerant flow to aid the return of oil to the compre-
sor.
†.
Every vertical suction riser greater than 3 feet should have a “P” trap at the bottom to facilitate the return of oil to the compressor. Use short radius fit-
tings of these traps.
‡.
Based on Refrigerant-22 at the nominal capacity of the condensing unit, a suction temperature of 40°F and a liquid temperature of 105°F.
**.
Although suction lines should be sized for a friction loss equivalent to a 2°F change in saturation temperature (or approximately 3 psi), sizing the lines
for the proper return of oil is more important.
††.
These friction losses do not include any allowances for valves or fittings.
TABLE 5: LIQUID LINES
Model Designation
Nominal
Capacity
(Tons)
Refrigerant Flow
Rate
*
(Lbs./Min.)
Type L Cop-
per Tubing
(Inches O.D.)
Pressure Drop
†
Friction
‡
(PSI/100 Ft.)
Vertical Rise (PSI/Ft.)
HF-0
7-1/2
22
1/2
5/8
11.0
3.5
0.5
*.
Based on Refrigerant-22 at the nominal capacity of the condensing unit, a suction temperature of 40°F and a liquid temperature of 105°F.
†.
The total pressure drop of the liquid line for both friction and vertical rise must not exceed 40 PSI. If the pressure drop exceeds 40 PSI, the liquid
refrigerant could flash before it reaches the expansion valve. This flashing will not only cause erratic valve operation and poor system performance,
but it could also damage the expansion valve.
‡.
These friction losses do not include any allowances for a strainer, filter-drier, solenoid valve, isolation valve or fittings.
TABLE 6: REFRIGERANT-22 LINE CHARGE
*
Liquid
†
Line
Inches, O.D.
1/2
5/8
3/4
0.070 lb./ft.
0.113 lb./ft.
0.167 lb./ft.
Suction Line
Inches, O.D.
1-1/8
1-3/8
1-5/8
0.009 lb./ft.
0.013 lb./ft.
0.019 lb./ft.
*.
Charges are based on 40°F suction temperature and 105°F liquid temperature.
†.
Type “L” copper tubing.
NOTE:
Add the operating charge of the condensing unit, the evaporator coil and the refrigerant lines to determine the total refrigerant charge for the
system.