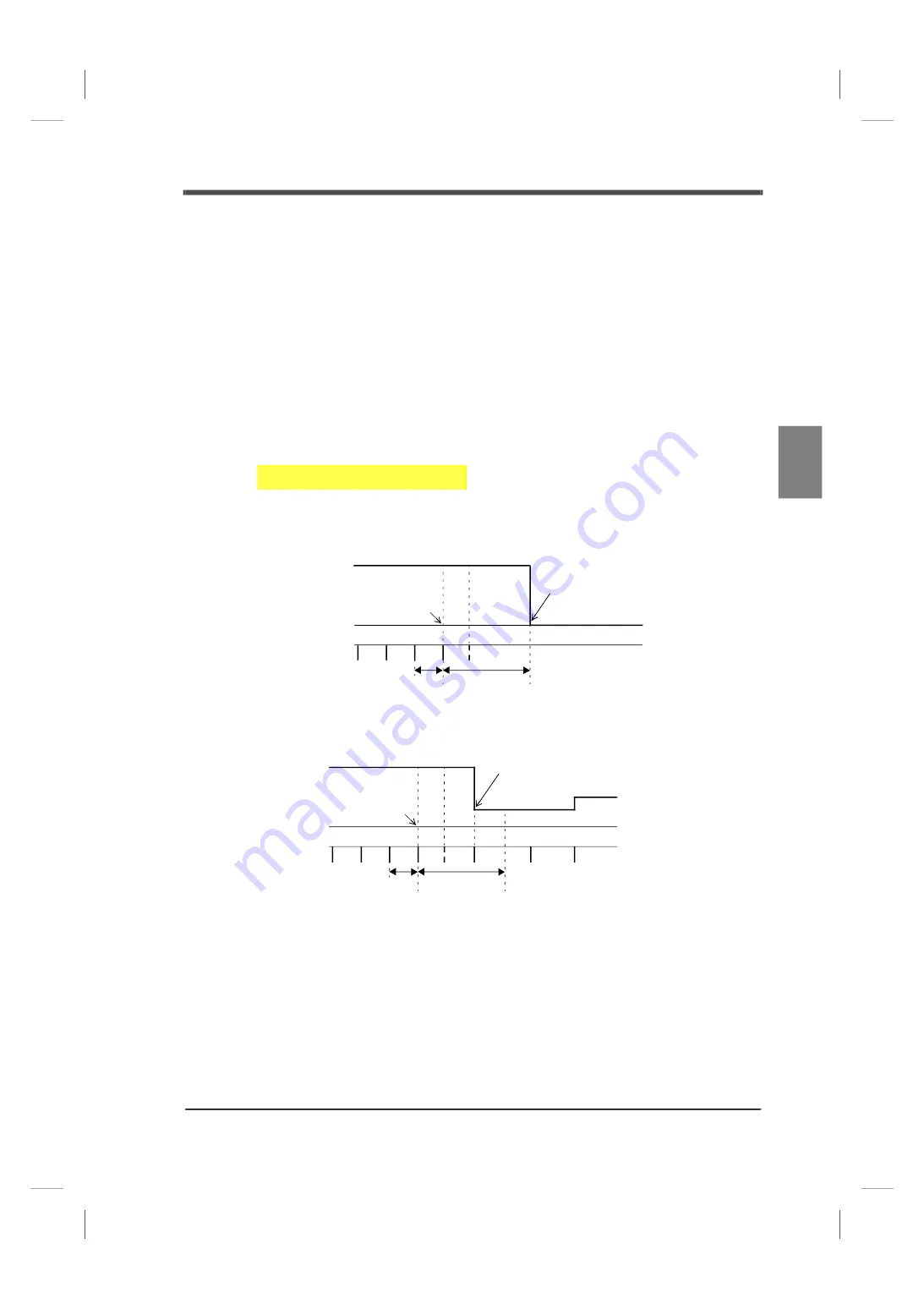
25
4
CALIBRATION
25
C
A
LI
B
R
A
TI
O
N
Chapter
4
■
Rotation stop mode
Cut-off looks unclear when the rotation stops suddenly due to the constraint of maximum detection
time corresponding to the minimum input rotation speed. For this reason, 0 rpm display can be
forcibly set with "the cycle of the rotation speed last detected × a certain multiple".
≪
Setting value
≫
OFF (invalid)
After detection is waited for the duration of the maximum detection time
corresponding to the minimum input rotation speed, the display becomes 0 rpm.
2, 4, 8 [times] (valid)
If pulse is not detected from the cycle of the rotation speed last detected to the cycle
of the set multiple, the display becomes 0 rpm forcibly.
How to set
Example) When stopped suddenly with the setting of "4 times"
Example) When decelerated suddenly with the setting of "4 times"
SET.
Calibration
Page 4
→
→
Pulse
Display
3000rpm
0rpm
Final cycle T
T×4
Since pulse is not detected,
Sudden stop
(Display held)
0 rpm is displayed
Pulse
Display
3000rpm
Final cycle T
T×4
1500rpm
New pulse is detected before T×4 time
Sudden deceleration
1000rpm
(Display held)
Summary of Contents for TM700
Page 1: ...20MAY2021REV 1 08 TORQUE MONITOR TM700 OPERATION MANUAL ...
Page 91: ......