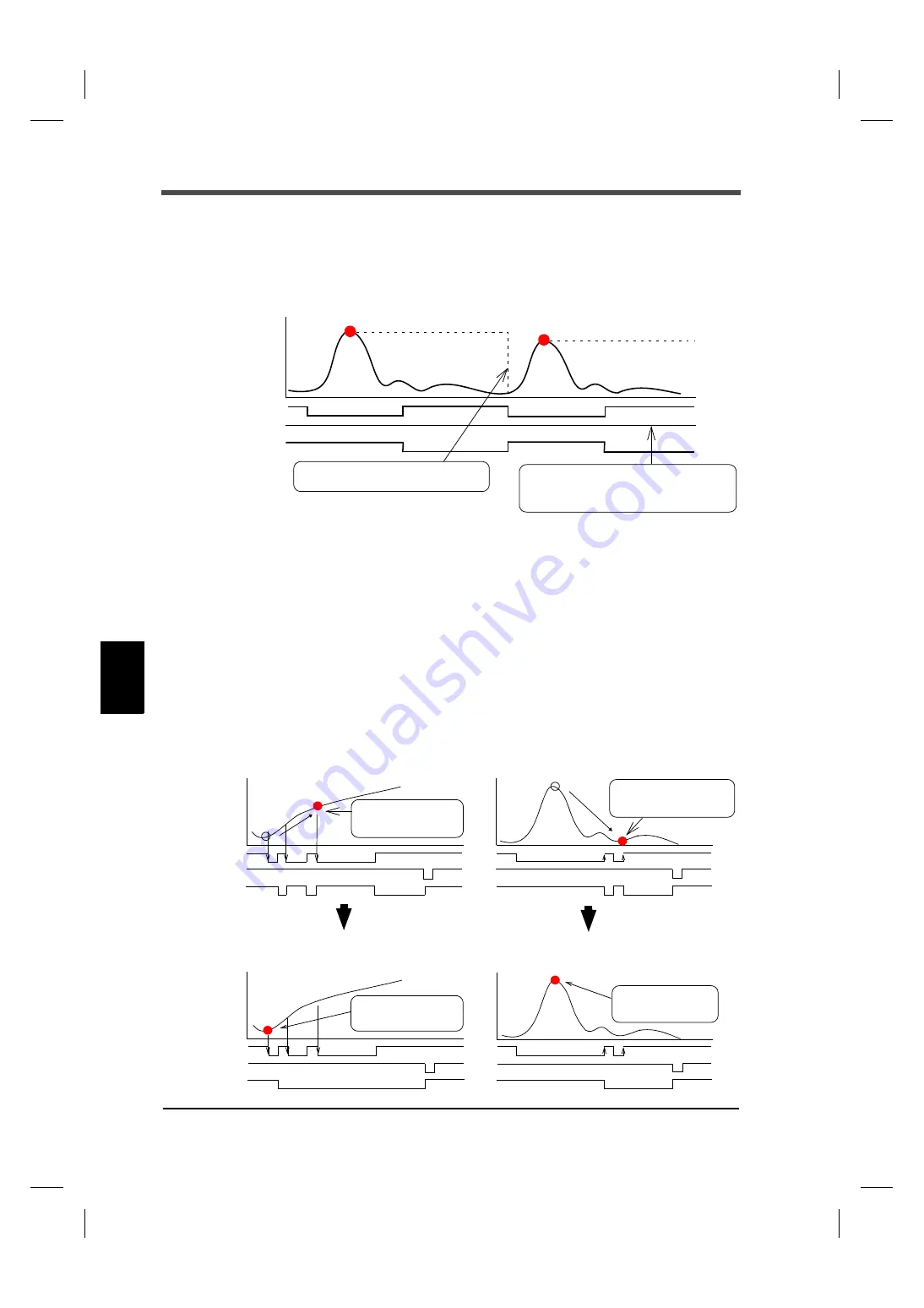
58
7
EXPLANATION OF HOLD FUNCTIONS
58
EXPLANATION OF HOLD FUNCTIONS
Chapter
7
7-4.
Auto reset function
It is factory-set that each hold is automatically reset at the start of the detection section, and
therefore, simple control can be performed by one signal without releasing the hold.
However, when the auto reset functions, if the signal causes chattering, the point that should be
taken originally may deviate. Switching is provided so as to prevent the next detection from being
performed until the T/H signal is turned on even if the SECTION signal is turned on again.
《
Setting value
》
0
:
OFF
After a hold is fixed, the next detection is not started until the T/H
signal is turned on even if the SECTION signal is turned on.
1
:
ON
After a hold is fixed, the next detection is started when the SECTION
signal is turned on again even if the T/H signal is not turned on. This is
the initial setting (factory default setting).
SECTION
T/H
H/E
Example) Auto reset in externally specified section peak hold
Upon turning-ON of the SECTION signal,
hold reset is performed and detection starts.
Control can be performed without inputting the T/H
signal.
However, a hold value is maintained until the
SECTION signal turns ON.
When auto reset is on in externally
SECTION
H/E
T/H
When auto reset is off in externally
SECTION
H/E
T/H
SECTION
H/E
T/H
SECTION
H/E
T/H
When auto reset is on in externally
When auto reset is off in externally
If the SECTION signal
chatters, the point shifts
from the proper one.
The first hold value is
maintained until T/H is
inputted.
If the SECTION signal
chatters, the point shifts from
the proper one.
The first hold value is
maintained until T/H is
inputted.
specified section sample hold
specified section peak hold
specified section peak hold
specified section sample hold
Summary of Contents for F350
Page 1: ...01MAR2015REV 1 04 F350 OPERATION MANUAL ...
Page 115: ......