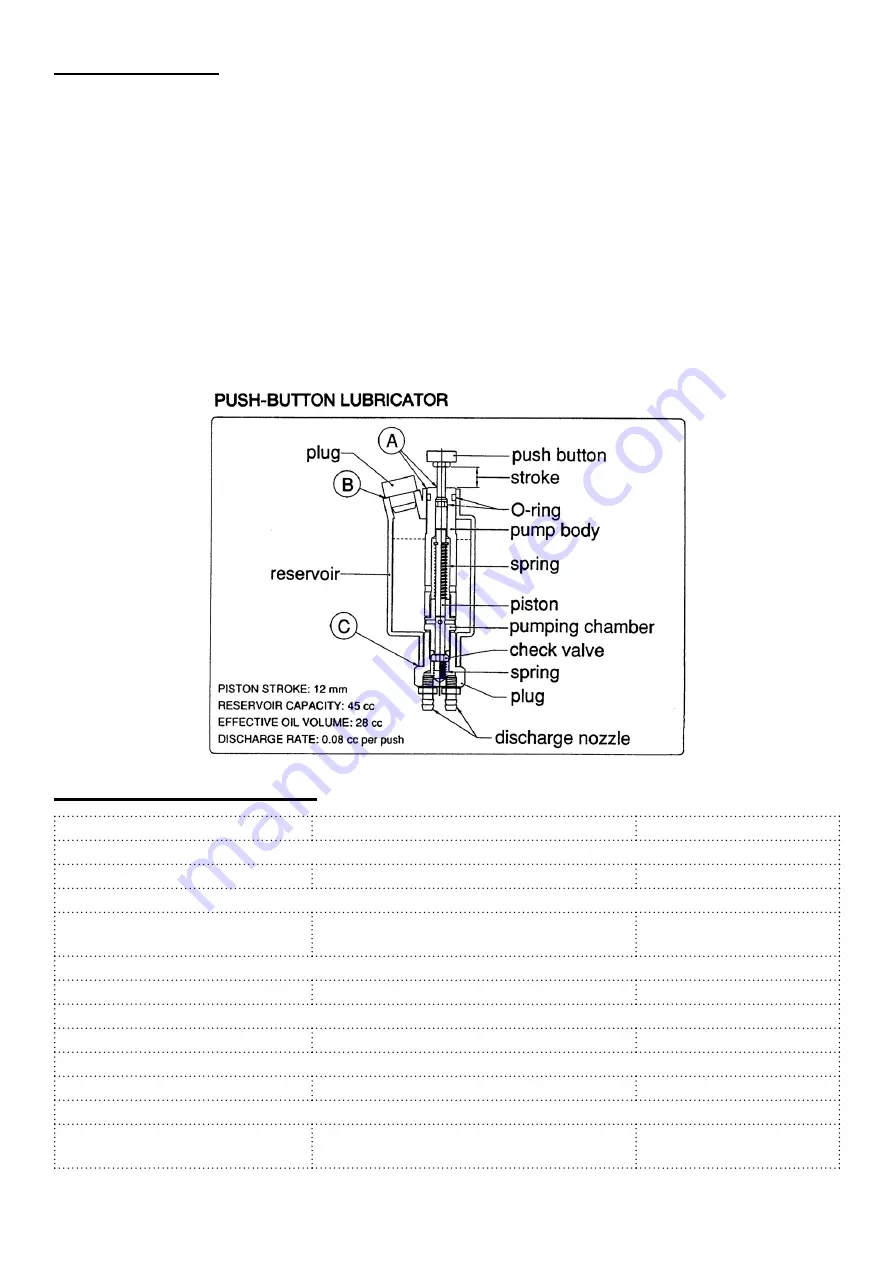
13
LUBRICATOR
OPERATION
The lubricator comprises a pump and a reservoir.
The reservoir holds max 45 cc of oil (effective oil
volume is 28 cc).
Use mineral oil 22-32 cSt at 40°C (Eg. Tellus oil
No.32). To operate the lubricator:
1. First unscrew the reservoir cap by half a turn. Do
not remove the cap completely.*
2. Push the button to its lowest position (stroke: 12
mm).
3. When released, the button will automatically re-
turn to its original position.
4. Lastly, tighten the cap to prevent oil leakage dur-
ing operation.
MAINTENANCE
1. Keep off dust or foreign matter when filling reser
-
voir (may cause jamming of piston and check the
valve).
2. Rate of discharge is fixed and not adjustable
(0.08cc per push).
3. At high temperatures, grease may run along
points (A). This is normal grease used during
assembly of lubricator in our plant.
4. Keep oil reservoir (high density polyehylene)
away from fire and do not use organic, benzene
or xylene chemicals for cleaning.
Regularly check the correct function of the oil
pump (Repeat oil feed and check oil through the
discharge pipe).
TROUBLE SHOOTING
PROBLEM
CAUSE
REMEDY
================================================================================
Oil not fed
Low oil level
Fill oil
================================================================================
Full stroke movement not obtain-
able
Dust attached on the interior of the pump
chamber
Replace lubricator
================================================================================
Button will not return
Dust accumulated or break of spring
Replace lubricator
================================================================================
Oil leak from (A)
Wornout or displaced seal of O-Ring
Replace lubricator
================================================================================
Oil leak from (B)
Wornout or displaced seal of Plug
Replace lubricator
================================================================================
Oil leak from (C)
Loose plug
Tighten Plug or replace
lubricator
Summary of Contents for 4500A
Page 2: ......
Page 6: ...6...
Page 17: ...17 VIEWS AND DESCRIPTION OF PARTS...
Page 18: ...18 THREAD TENSION AND COVERS 1 THREAD TENSION AND COVER PARTS...
Page 20: ...20 BUSHINGS OIL PUMP AND HANDLE...
Page 22: ...22 for Net Bag NEEDLE BAR PRESSER BAR AND DRIVING PARTS...
Page 24: ...24 LOOPER DRIVE...
Page 26: ...26 FEED DRIVE AND THREAD CUTTER...
Page 28: ...28 MOTOR PARTS for completely enclosed type motor 15 8 18...
Page 30: ...30 ACCESSORIES 7 ACCESSORY BAG...
Page 32: ...32 DRIVE PARTS 8 MOTOR PARTS...