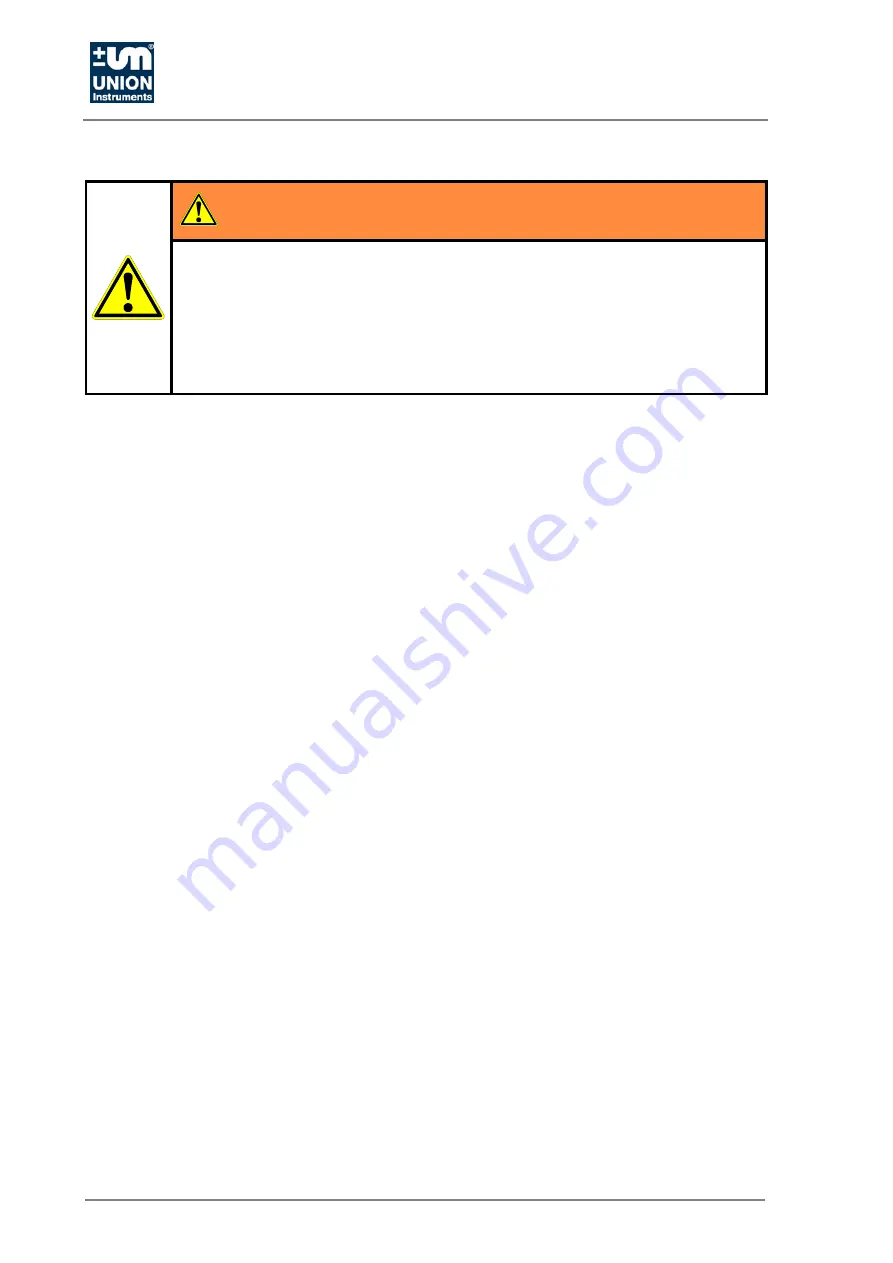
Description and connections
26
5.3 Accessories
WARNING
Risk of injury/damage!
The use of non-approved accessories may cause damage and endanger per-
sons. Any warranty is voided in this case! The owner is then liable for damage
that occurs!
Only use genuine accessories or accessories approved by UNION Instruments
GmbH.
Summary of Contents for CWD2005 SPC
Page 1: ...Apr 2016 V1 06 Original Operating Instructions Combustion Calorimeter CWD2005 CWD2005 Plus ...
Page 10: ...Technical data 10 ...
Page 12: ...EU Declaration of Conformity 12 ...
Page 18: ...Safety information 18 ...
Page 22: ...Protective equipment 22 ...
Page 48: ...Description of the work stations operator control elements 48 ...
Page 63: ...Operation 63 Main menu Options Calibration Calibration values are configured in this menu ...
Page 87: ...Operation 87 ...
Page 88: ...Operation 88 ...
Page 90: ...Decommissioning Switching off 90 ...
Page 94: ...Maintenance 94 ...
Page 100: ...Troubleshooting 100 ...
Page 102: ...Service 102 ...
Page 104: ...Disposal 104 ...
Page 106: ...Spare parts 106 ...