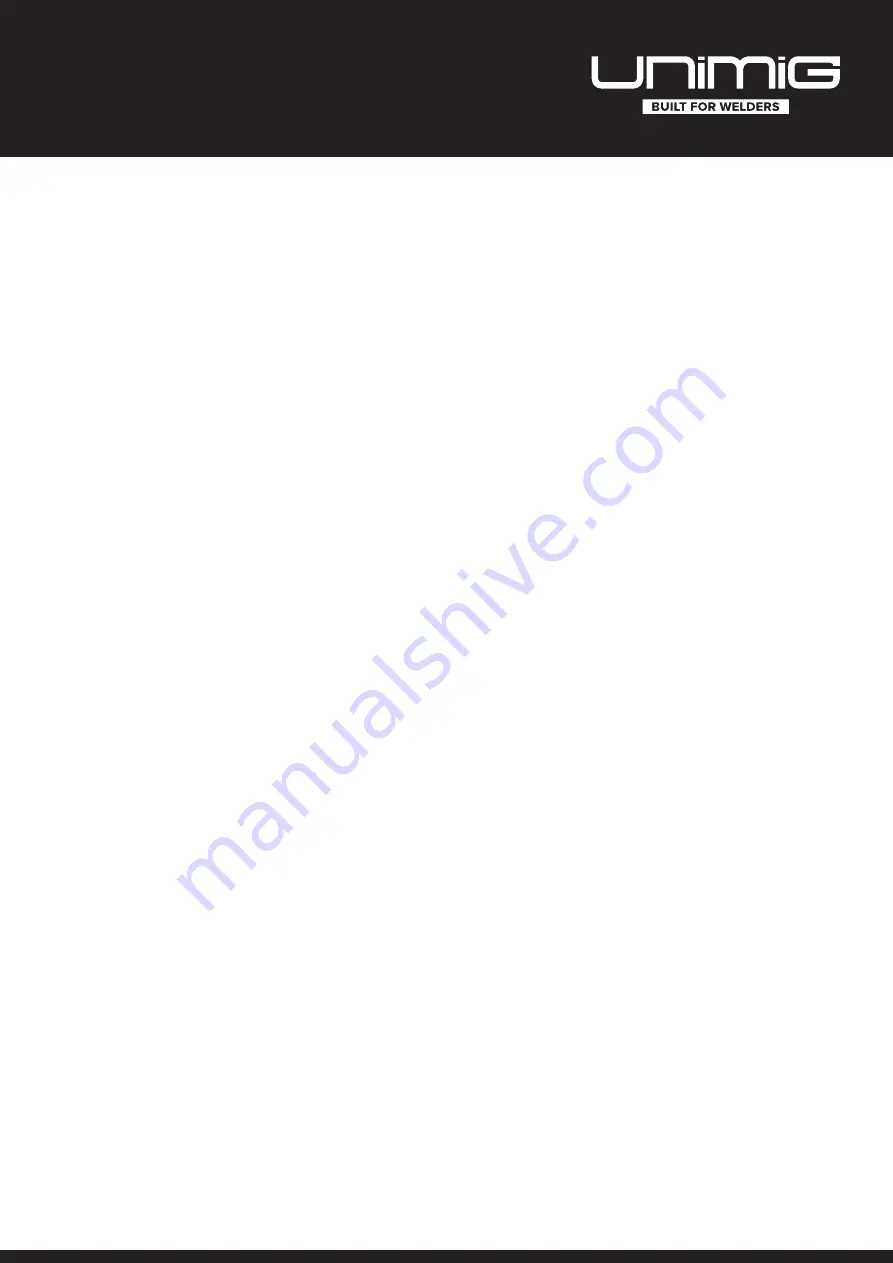
WARRANTY EXCLUSIONS
This Warranty covers Material and Faulty Workmanship defects only.
This Warranty does not cover damage caused by:
• Normal wear and tear due to usage
•
Misuse or abusive use of the UNIMIG, UNI-TIG, UNI-PLAS, UNI-FLAME, TECNA, T&R, HIT-8SS & ROTA, instructions supplied with the product.
• Failure to clean or improper cleaning of the product
• Failure to maintain the equipment such as regular services etc
• Incorrect voltage or non-authorised electrical connections
• Improper installation
• Use of non-authorised/non-standard parts
• Abnormal product performance caused by any ancillary equipment interference or other external factors
• Failure or any breakage caused by overload, dropping or abusive treatment or use by the customer
•
Repair, modifications or other work carried out on the product other than by an Authorised UNIMIG, UNI-TIG, UNI-PLAS, UNI-FLAME, TECNA, T&R, HIT-
8SS & ROTA Service Dealer
Unless it is a manufacturing fault, this Warranty does not cover the following parts:
MIG Welding Torches and Consumables to suit, such as:
Gas Nozzles, Gas Diffusers, Contact Tip holder, Contact tip, Swan Necks, Trigger, Handle, Liners,Wire Guide, Drive Roller, Gas Nozzle Spring. Neck Spring,
Connector Block, Insulator, Gas Nipple, Cap, Euro Block, Head Assembly, Gas Block, Trigger Spring, Spring Cable Support, Neck Insulator, Shroud Spring,Gun
Plug Cover, Lock Nut, Snap On Head, Spring Cap, Ball, Motor 42 Volt, Pot 10K standard, Knob, Drive Roll Seat, Washer, Bow, Ball Bearing, Wire Condue
Nipple, Central Plug, Printed Circuit Board, Gun Plug House, Cable Support, Gas Connector, Handle To Suit PP36 with Knobs, All Xcel-Arc/ Magmaweld MIG
Welding Wires & Electrodes, Arc Leads, Welding Cable, Electrode Holder, Earth Clamps
TIG Welding Torches and Consumables to suit, such as:
Tungsten Electrodes, Collet, Collet Body, Alumina Nozzle, Torch Head, Torch Head water Cooled, Torch Head Flexible,Back Caps, Gas Lens, Torch Handle,
Cup Gasket, Torch Body Gas Valve, O-ring, All UNIMIG TIG Welding Rods, All Xcel-Arc/ Magmaweld Electrodes, Arc Leads, Welding Cable, Electrode Holder,
Earth Clamps.
PLASMA Cutting Torches and Consumables to suit, such as:
All Cutting Tips, All Diffuser/Swirl Ring, All Electrode, Retaining Caps, Nozzle Springs, All Spacers, All Shield Caps, All Air and Power Cables, All Switches, All
O-rings, All Springs, All Circle Guides and Cutting Kits, Torch Bodies, Air Filter Regulator, Arc Leads, Welding Cable, Electrode Holder, Earth Clamps
STRAIGHT LINE CUTTING MACHINES and Consumables to suit, such as:
Hoses, Fittings, Track, Cutting Nozzles.
HIT-8SS Welding Carriage Consumables to suit, such as:
Input Cord, Inter-connecting Cord, Triggering Cable.
This Warranty does not cover products purchased:
•
From a non-authorised UNIMIG, UNI-TIG, UNI-PLAS, UNI-FLAME, TECNA,T&R, HIT-8SS & ROTA Dealer (such as purchases from unauthorised retailers
and purchases over the Internet from unauthorised local/international sellers or sites such as EBay)
•
At an auction;
• From a private seller
Unless it is a manufacturing fault, this Warranty does not apply to any products sold to Hire Companies.
These conditions may only be varied with the written approval of the Directors of Welding Guns Of Australia PTY LTD
REMEMBER TO RETAIN YOUR ORIGINAL INVOICE FOR PROOF OF PURCHASE.
36
| VIPER MIG 182 Manual
WARRANTY TERMS
Summary of Contents for VIPER MIG STICK 182
Page 37: ...VIPER MIG 182 Manual 37 NOTES...
Page 38: ...38 VIPER MIG 182 Manual NOTES...
Page 39: ...VIPER MIG 182 Manual 39 NOTES...