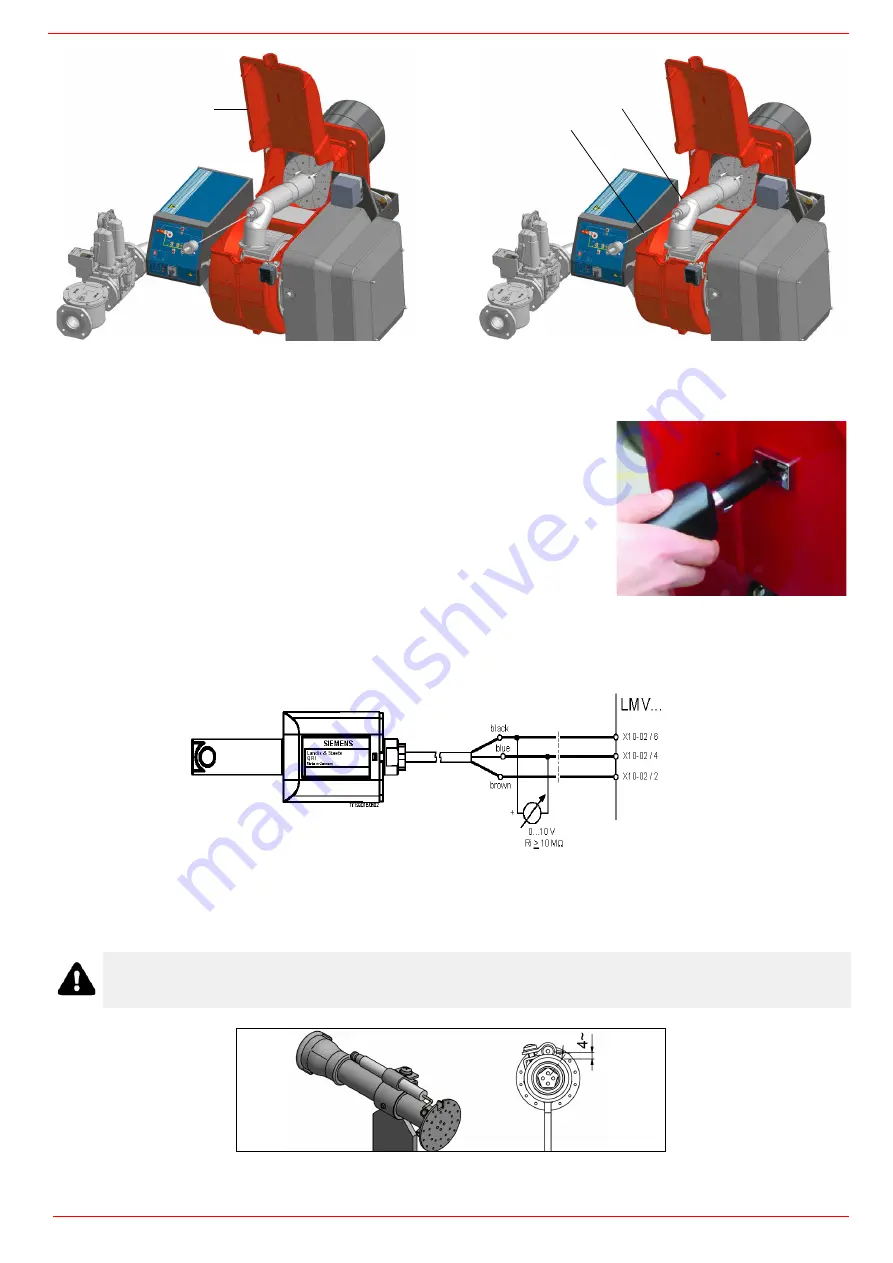
PART IV: MAINTENANCE
37
Ignition pilot electrode positions (if provided)
ATTENTION:
avoid
the ignition and detection electrodes to contact metallic parts (blast tube, head, etc.), otherwise the boi-
ler’s operation would be compromised. Check the electrodes position after any intervention on the combustion head.
C
AR
G
Flame detection probe
To clean/replace the detection photocell, proceed as follows:
1 Disconnect the system from the electrical power supply.
2 Shut off the fuel supply;
3 remove the photocell from its slot (see next figure);
4 clean the bulbe if dirty, taking care not to touch it with bare hands;
5 if necessary, replace the bulb;
replace the photocell into its slot.
Checking the detection current
To check the detection signal follow the scheme in the picture below. If the signal is less than the value indicated, check the position of
the detection electrode or detector, the electrical contacts and, if necessary, replace the electrode or the detector.
Minimum detection signal: 3.5Vdc
Fig. 12 - Detection with detector QRI...
Summary of Contents for TLX2020
Page 42: ...Annex1 Example for motor cable...
Page 43: ......
Page 44: ...Annex 2 Example for sensor cable...
Page 45: ......
Page 46: ......
Page 50: ......