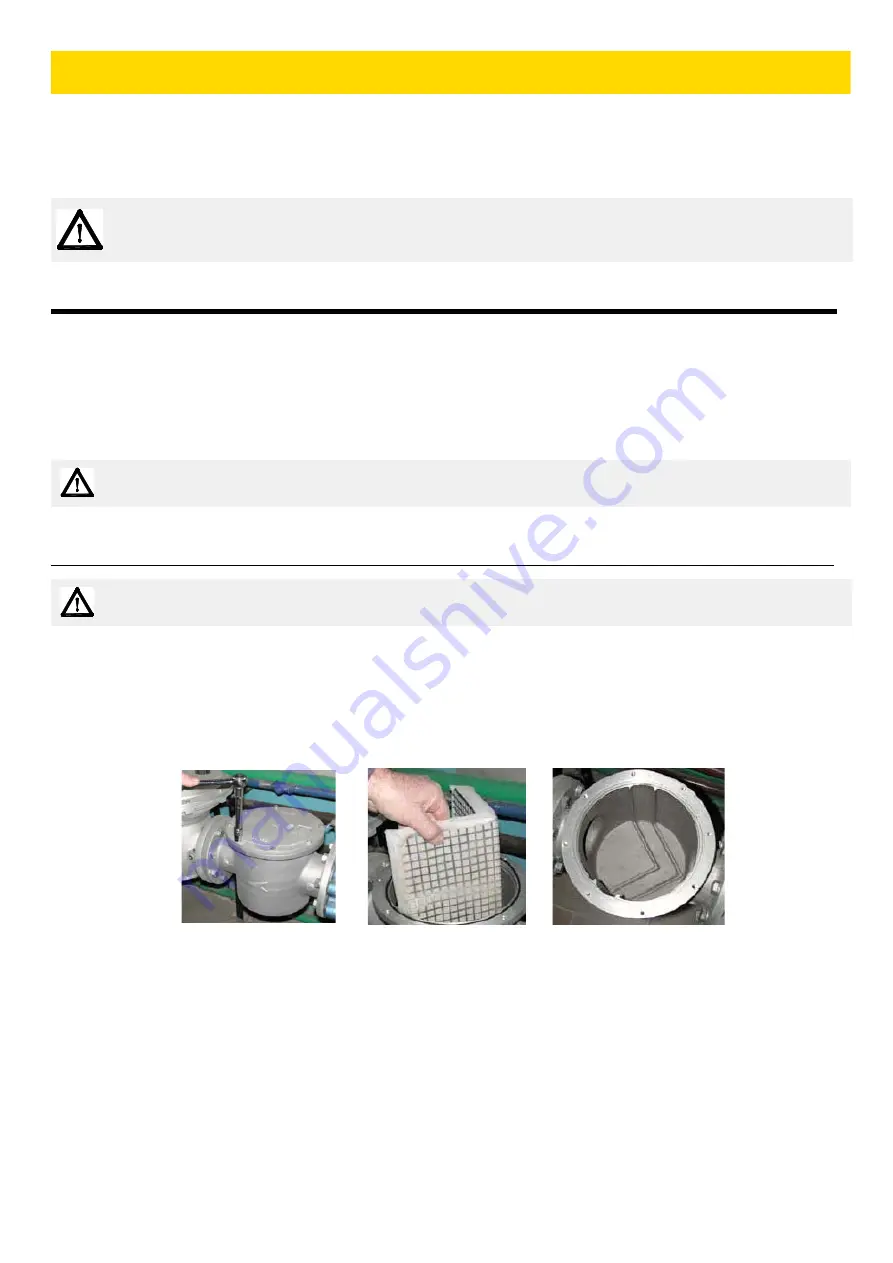
PART IV: MAINTENANCE
29
At least once a year carry out the maintenance operations listed below. In the case of seasonal servicing, it is recommended to carry
out the maintenance at the end of each heating season; in the case of continuous operation the maintenance is carried out every 6
months.
6.0 ROUTINE MAINTENANCE
z
Clean and examine the gas filter cartridge and replace it if necesssary;
z
Remove and clean the combustion head;
z
Examine and clean the ignition electrodes, adjust and replace them if necessary;
z
Examine and clean the detection electrode/photoelement (according to the burner models), replace it if necessary, in case of
doubt, check the detection circuit, after the burner start-up;
z
Clean and grease leverages and rotating parts.
6.1 Gas filter maintenance
To clean or remove the filter, proceed as follows:
1
remove the cap unscrewing the fixing screws (A);
2
remove the filtering cartridge (B), clean it using water and soap, blow it with compressed air(or replace it, if necessary)
3
replace the cartridge in its proper position taking care to place it inbetween the guides as not to hamper the cap replacement;
4
be sure to replace the “O” ring into its place (C) and replace the cover fastening by the proper screws (A).
WARNING: ALL OPERATIONS ON THE BURNER MUST BE CARRIED OUT WITH THE MAINS DISCONNECTED
AND THE FUEL MANAUL CUTOFF VALVES CLOSED!
ATTENTION: READ CAREFULLY THE “WARNINGS” CHAPTER AT THE BEGINNIG OF THIS MANUAL..
ATTENTION: when servicing, if it was necessary to disassemble the gas train parts, remember to execute the gas
proving test, once the gas train is reassembled, according to the procedure imposed by the law in force.
ATTENTION: Before opening the filter, close the manual cutoff valve downstream the filter and bleed the gas;
check that inside the filter there is no pressurised gas.
A
B
C
PART IV: MAINTENANCE