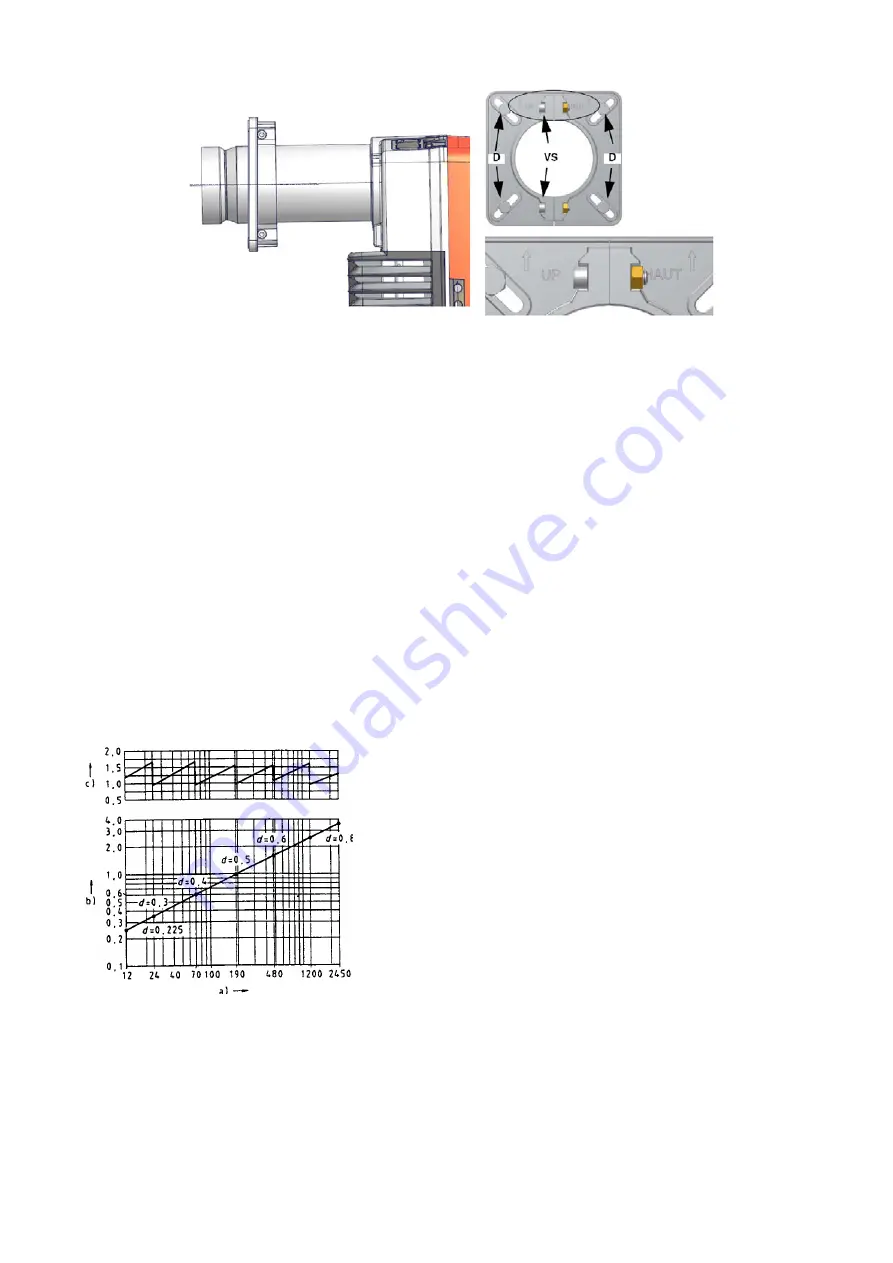
10
Fig. 2
Once the burner is installed into the boiler, go on with the electrical and hydraulic connections, according to the diagrams
shown on the following paragraphs.
Matching the burner to the boiler
The burners described in this manual have been tested with combustion chambers that comply with EN267 regulation and
whose dimensions are described in the diagram . In case the burner must be coupled with boilers with a combustion
chamber smaller in diameter or shorter than those described in the diagram, please contact the supplier, to verify that a
correct matching is possible, with respect of the application involved. To correctly match the burner to the boiler verify the
necessary input and the pressure in combustion chamber are included in the burner performance curve; otherwise the
choice of the burner must be revised consulting the burner manufacturer. To choose the blast tube lenght follow the
instructions of the boiler manufacturer. In absence of these consider the following:
Cast-iron boilers, three pass flue boilers (with the first pass in the rear part): the blast tube must protrude no more than
100 mm (values between 0 and 100mm) into the combustion chamber.
Pressurised boilers with flame reversal: in this case the blast tube must penetrate at least 50 - 100 mm into combustion
chamber in respect to the tube bundle plate.
The length of the blast tubes does not always allow this requirement to be met, and thus it may be necessary to use a
suitably-sized spacer to move the burner backwards or to design a blast tube tha suites the utilisation (please, contact the
manifacturer).
Fig. 3
Keys
a) Heat output in kW
b) Length of the flame tube in meters
c) Flame tube firing intensity in MW/m3
d) Combustion chamber diameter (m)
Fig.3:Firing intensity, diameter and lenght of the test flame tube as a function of the heat
input in kW.