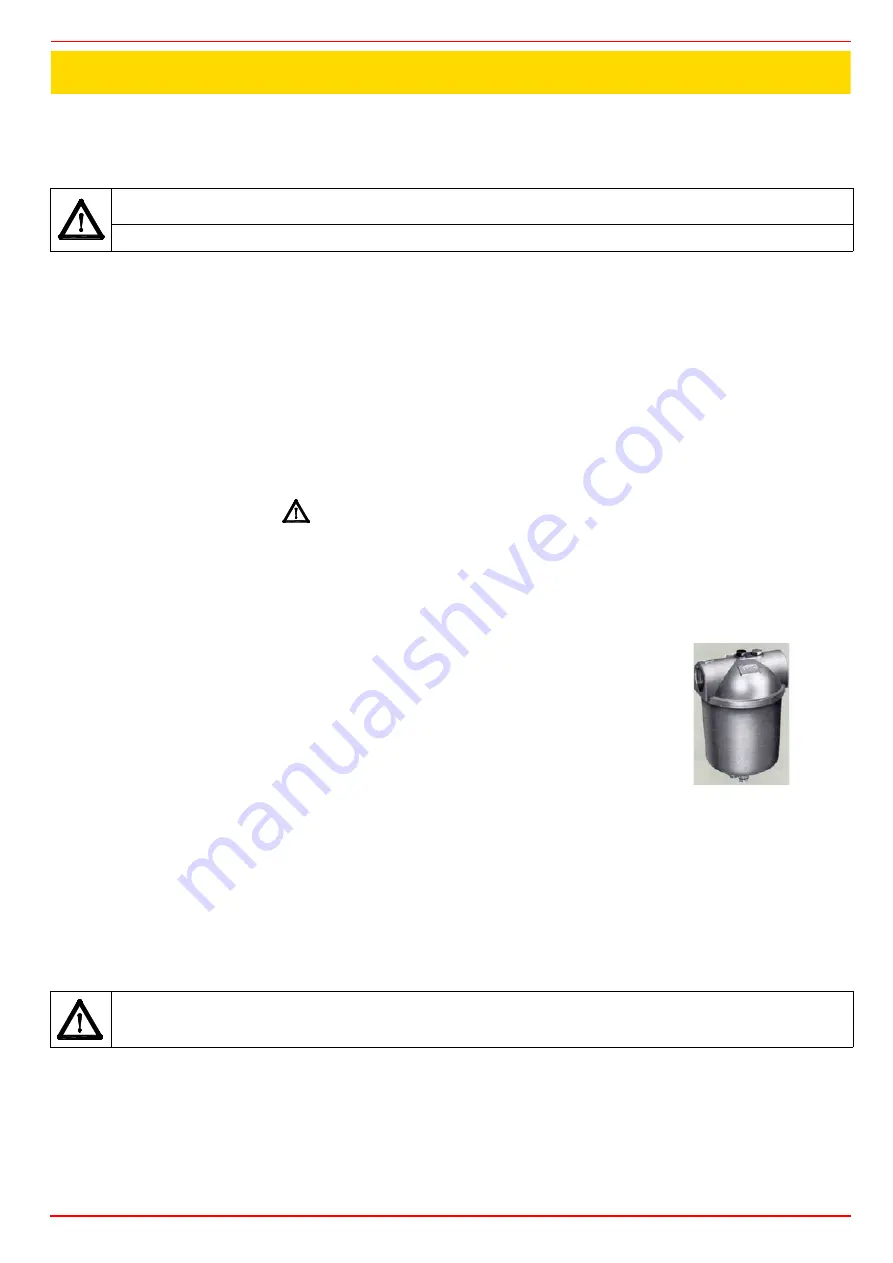
19
At least once a year carry out the maintenance operations listed below. In the case of seasonal servicing, it is recommended to carry
out the maintenance at the end of each heating season; in the case of continuous operation the maintenance is carried out every 6
months.
ROUTINE MAINTENANCE
Check and clean the fuel filter cartdrige, replace if necessary.
Check and clean the filter inside the light oil pump: filter must be thoroughly cleaned at least once in a season to ensure correct
working of the fuel unit. To remove the filter, unscrew the four screws on the cover. When reassemble, make sure that the filter is
mounted with the feet toward the pump body. If the gasket between cover and pump housing should be damaged, it must be repla-
ced. An external filter should always be installed in the suction line upstream of the fuel unit.
Check the fuel hoses for possible leaks.
Remove, check and clean the combustion head (see page 19);
Check ignition electrodes, clean, adjust and, if necessary, replace them (see page 20);
Check and carefully clean the flame detector, replace it if necessary; if in doubt, check the detection current, once the burner starts
up (see page 21).
Remove and clean the fuel nozzle
(Important:
cleaning must be performed using solvent, not metal tools!
).
At the end of
maintenance operations after the burner reassembly, light the flame and check its shape, replacing the nozzle whenever a questio-
nable flame shape appears. Whenever the burner is used intensely, we recommend preventively replacing the nozzle at the start of
each heating season.
Clean and grease sliding and rotating parts.
Removing the combustion head
1
Remove the burner cover by unscrewing the fixing screws
2
Remove the
FR
detection probe from its slot; disconnect the electrodes cables and remove the light oil pipe.
3
Unscrew the four screws that fasten the head ass.y
Unscrew the screws that fasten the gas manifold (
C
).
4
The operator must pull the burner towards him/her self to take the combustion head out.
5
Clean the combustion head by means of a vacuum cleaner; scrape the scale off using a metallic brush.
Note:
to reassemble the burner, follow the procedure above in the reversed oredr.
Adjusting the electrodes and nozzle position
Fix a stable surface to lean on the burner during maintenance.
To gain access to the combustion head and to the nozzles, slacken the screw on the blast tube and remove it from the part that
remains fixed to the boiler.
To guarantee a good ignition, observe the measures shown in the table below.
Be sure to tight the screw that fix the electrodes group, before reassembling the burner.
WARNING: ALL OPERATIONS ON THE BURNER MUST BE CARRIED OUT WITH THE MAINS DISCONNECTED AND
THE FUEL MANAUL CUTOFF VALVES CLOSED!
ATTENTION: READ CAREFULLY THE “WARNINGS” CHAPTER AT THE BEGINNIG OF THIS MANUAL..
Light oil filter maintenance
For correct and proper servicing, proceed as follows:
1
cutoff the required pipe section;
2
unscrew the filter cup;
3
remove the filtering cartridge, wash it with gasoline; if necessary, replace it; check the tightening
O-rings and replace them if necessary;
4
replace the cup and restore the pipe line.
5
ATTENTION:
avoid
the electrodes to get in touch with metallic parts (blast tube, head, etc.), otherwise the boiler operation
would be compromised. Check the electrodes position after any intervention on the combustion head.
PART III: MAINTENANCE