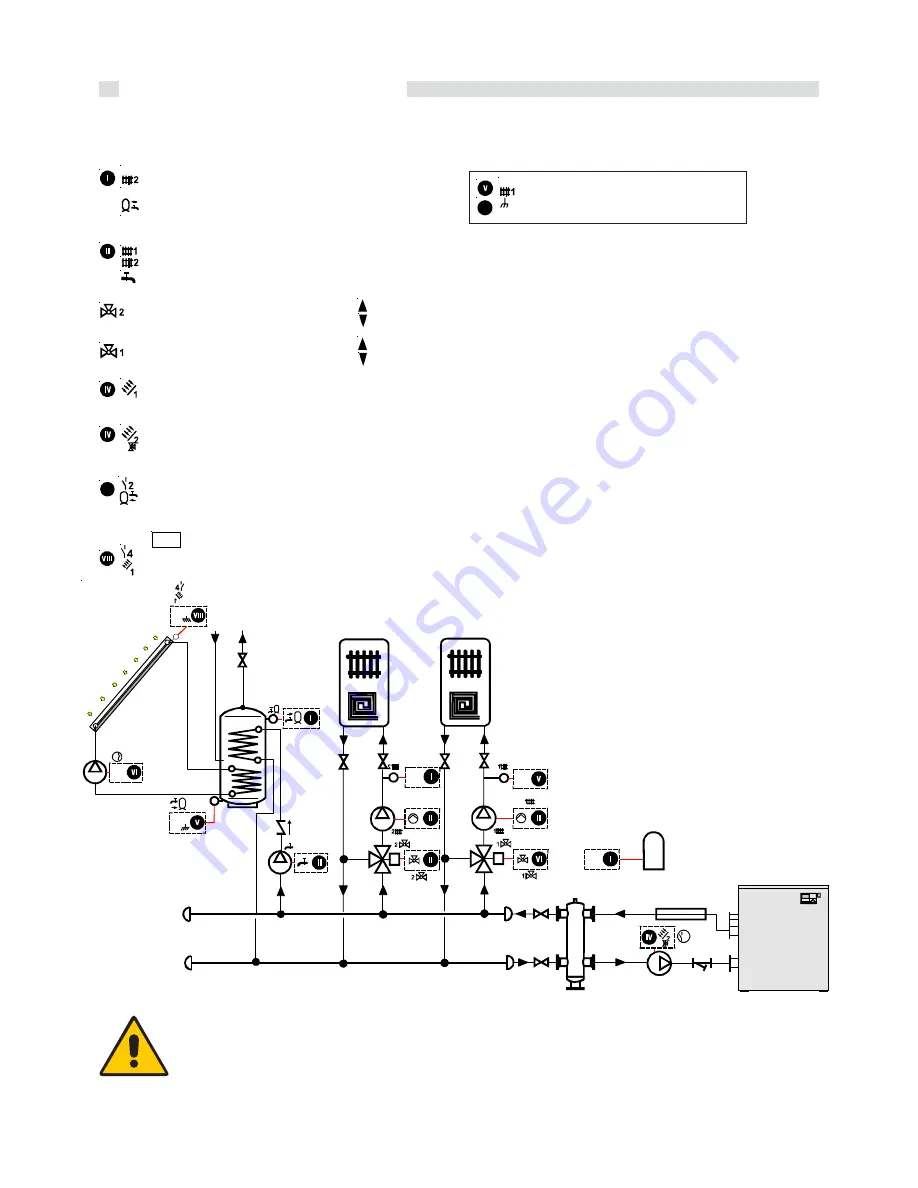
40
Instructions for the installer
VF
VF
1
2
VF
VF
VF
AF
M
R
SPF
C
F
A11
5
4
PT1000
2+
F14
F12
2+
3
Mixing Header
Filter
Heating Circuit 1
Outside
Sensor
Heating Circuit 2
Safety devices kit
Primary
system pump
INSTALLATION OF A BOILER WITH CONNECTION TO TWO MIXED ZONES + D.H.W. PRODUCTION BY SOLAR PANELS
(9-10) outdoor sensor
(4-5) Flow sensor heating circuit 2
(6-7) Storage tank sensor
(4) Pump heating circuit 1
(5) Pump heating circuit 2
(6) Cylinder charging pump
SPF
AF
n
(5) Re-circulation pump storage tank
VF
V
(2) Hot water tank low / Multifunction relay sensor 2
(2) PT1000 sensor solar 1 / Multifunction relay sensor 4
PT1000
For the connection to a solar installation it is
necessary to change some parameters. See
Table:
Expert AREA
⇒
Level SOLAR / MF
⇒
MF 4
FUNCTION = ‘’23’’
(4) Collector pump
(7) Mixer motor heating circuit 2 OPEN
(8) Mixer motor heating circuit 2 CLOSE
(1) Mixer motor heating circuit 1 OPEN
(2) Mixer motor heating circuit 1CLOSE
(1) Flow sensor heating circuit 1
VF
10
I
(10) Ground outdoor sensor