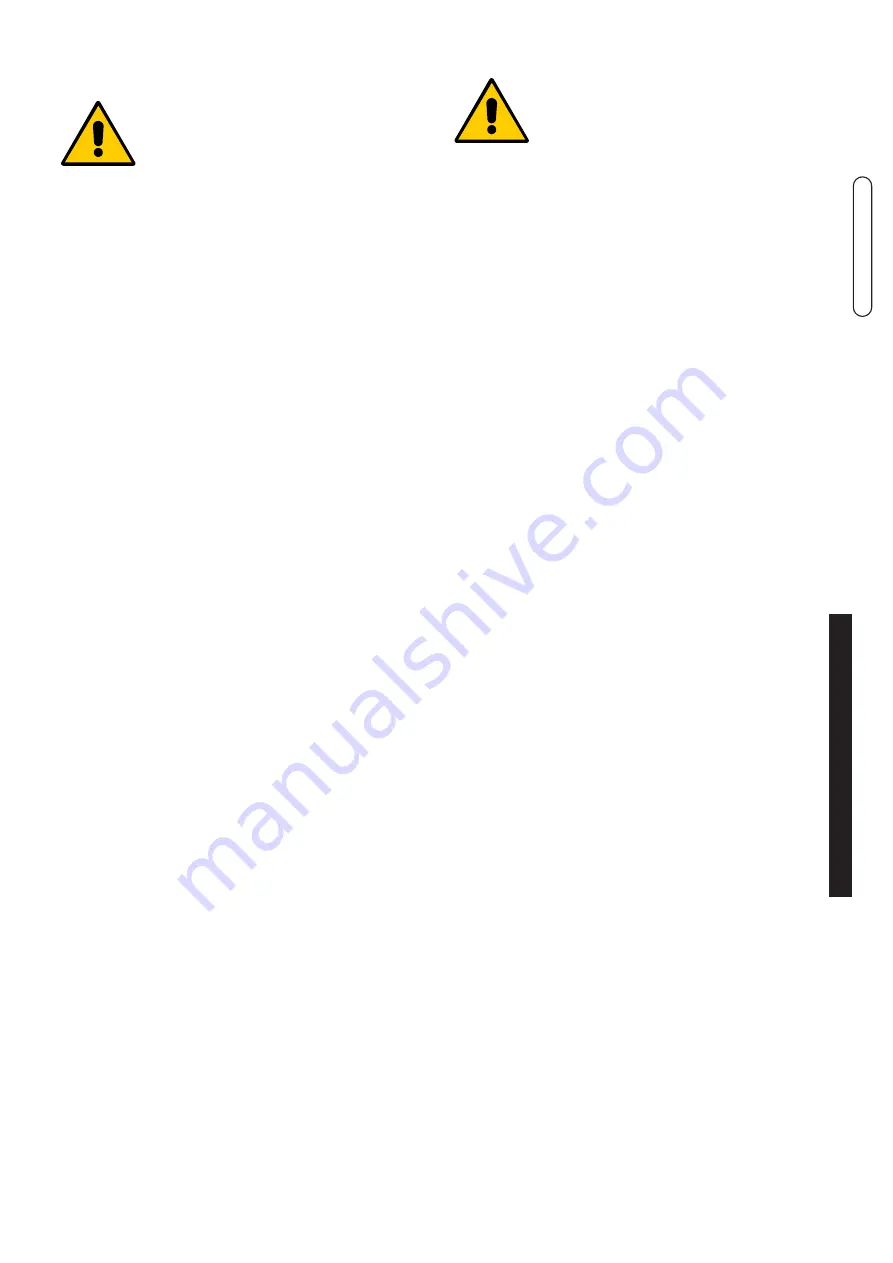
25
ENGLISH
Installation Instructions
- Terminal of collective duct must
generate a draft.
- Before carrying out any operation, di-
sconnect the electrical power supply to
the appliance.
- Before assembly, lubricate seals with
non-corrosive grease.
- The exhaust duct must be inclined,
in the case of a horizontal duct, by 3°
towards the boiler.
- Number and characteristics of applian-
ces connected to the collective flue, must
be adequate to the characteristics of the
collective flue.
- Condensation can flow inside the
boiler.
The maximum recirculation value al
-
lowed in windy conditions is 10%.
- The maximum pressure difference
allowed (25 Pa) between the inlet of the
combustion products and the air outlet
of a collective flue cannot be exceeded
when n-1 boilers work at the maximum
nominal heat output and 1 boiler at the
output minimum temperature allowed by
the controls
- The collective flue duct must be ade
-
quate for an overpressure of at least
200 Pa
- The collective flue must not be equip
-
ped with a draft-breaking-windproof
device.
N.B.: The non-return valve (clapet) is
a mandatory device in case of installa
-
tions in positive pressure collective flue
systems.
This is an optional kit not
present inside the boiler.
WARNINGS:
- The appliances connected to a collecti-
ve flue, must all be of the same type and
have equivalent combustion characteri
-
stics.
- The number of devices that can be
connected to a collective flue in positive
pressure is defined by the designer of
the flue.
The boiler is designed to be connected to
a collective flue sized to operate in con
-
ditions in which the static pressure of the
collective flue duct can exceed the static
pressure of the collective air duct by 25
Pa in the condition in which n-1 boilers
work at maximum flow rate nominal heat
and 1 boiler at the minimum heat input
allowed by the controls.
- The assembly of the ducts must be
carried out in such a way as to avoid con
-
densation which would prevent the correct
evacuation of the combustion products.
- A data plate must be present at the con-
nection point with the collective smoke
duct. Data plate must contained the fol-
lowing information:
- the collective flue is sized for
type C (10) boilers
- the maximum mass flow rate allowed
of combustion products in Kg/h.
- size of the connection to common
ducts
- a warning regarding openings for
air outlet and product inlet
of the combustion of the smokes
collective air under pressure;
such openings they must be closed
and it must be verified their tightness
when the boiler is disconnected
- name of duct manufacturer
collective smoke or its identification
symbol
- Refer to the regulations in force for
the discharge of combustion products
and local provisions
- The fume and intake duct must be appro-
priately chosen based on the parameters
reported below
FOLLOWS: Installation on collective flues in positive pressure